As a fire chief and editor-in-chief of Firehouse®, I have visited or been invited to numerous apparatus factories around the country. Seeing the latest types of apparatus with new features is certainly a benefit when attending conferences and expositions around the country. Where else could you view, evaluate, discuss and inquire about possible options, additions and required items on new apparatus? These opportunities are vital to apparatus committees seeking to make a purchase in the near future.
Coming up the ranks within the fire service, I have been involved with purchasing in different ways. During my tenure of more than 20 years, our fire department purchased two engines, two ladders, a squad (half engine/half rescue), renovated a heavy rescue and purchased a pickup truck and several SUVs. Anyone involved in this process picks up the small and major details along the way. Here are some of the tips I have picked up and can share with anyone who is going to serve on an apparatus purchasing committee.
1. The need
Advise the people with the purse strings that you need a new piece of apparatus well in advance. You can’t walk in today and say you need a new piece of apparatus that costs hundreds of thousands of dollars and expect them to give their approval tomorrow. The first thing I remember when I took over as fire chief in 1988 was having to prepare an operating budget, a capital budget and a 10-year plan. That’s when I read about giving plenty of notice about very large purchases. It doesn’t always work out when it comes to the fire department agenda and the municipal budget. When our new mayor was elected, he was advised that the fire department needed a new pumper. He wanted a new artificial-turf soccer field. Guess which item was purchased? His agenda was more important than ours.
2. What are you going to buy?
Do your homework. Make sure you look at several types of models and different manufacturers and visit the departments near you to talk with the people who specified the apparatus, operate them and maintain them to see what their comments are. Take the time to ride on the rig and see how it performs and how the apparatus is set up for a ladder and pumping for an engine. Look at all the aspects of the items they had specified or added, especially if it is a specialty unit such as a heavy rescue.
3. What are your specific needs?
Discuss your varied ideas with the manufacturer’s representatives and find out all the options they offer before the process begins, not after you see the finished product in the factory. We had a rescue truck undergo a renovation mainly for the problems with the chassis and body. Nobody had ever mentioned all the added extras that were available until we saw them on other rigs in their factory and plant. If we had only known about these items, it would have streamlined the renovation, not adding them at the last minute.
We purchased a new aerial ladder with an extended cab. The cab was going to have about 12 more inches in length, four for the driver and eight for the jump and flip seats. I wanted to make sure that even if the manufacturer had to cut into the through compartment that ran from side to side of the apparatus that the firefighters in the flip seat had space to don their self-contained breathing apparatus (SCBA). The builder said that might cut into the compartment, robbing space. I said I needed the firefighters to wear the SCBA 100% of the time. Maybe we would use something from the through compartment 5% of the time. It was about what we needed, not what they wanted to give us.
4. Saving time, but doing it right.
Make use of available technology. This allows you to go online and review, add or change the specifications immediately, thus refining a process that was cumbersome and lengthy. What takes a few minutes today used to take weeks of mail going back and forth between you and the apparatus representative.
5. They can add it. Can you afford it?
Price out all the items you want. Can the manufacturer provide 10 of these items? Yes, but there is always a cost. Ten times $750 equals $7,500. Does your budget allow that or can you operate reasonably with two? Can the funds be used in a better way to provide something else?
6. Review
Go over the specifications with a fine-tooth comb. Once they have been awarded, what’s in the contract becomes the letter of the law. If the manufacturer cannot make something work, they will come back with a compromise.
7. The small details – make sure they understand
Pre-build meetings are important, just like every other aspect of the project. Discuss your thoughts and ideas about how you envision the operations and procedures to work so the manufacturer can help you build exactly what you want. Many apparatus could not fit into a firehouse because someone forgot to measure the height of the apparatus door the rig would need to fit in. You are going to use the apparatus for 10 to 30 years, depending on where you are located. Be smart, and do it right the first time.
8. Final check
Factory visits made before paint and final inspection will allow you to physically check each line item in the specification, detail and location of each piece of equipment and make sure they have been installed in the right place and that they work. No matter how long it takes on your inspection visit, you have to make sure everything is according to “spec.”
9. The sale after the sale
Much effort goes into putting an apparatus committee together. These many steps include: Investigating the various types of rigs that are available and right for your operation. Visiting and talking with other departments who operate these units, working with the manufacturers, writing the specifications, putting it out for bid, the acceptance process, awarding the bid, pre-build meetings, inspecting the rig and accepting the rig and training on the new apparatus.
Some departments, depending on use, replace their apparatus every 10, 12, 14, 20 years or more. To maintain the rig for all those years is what some manufacturers call “the sale after the sale.” Continual maintenance and upkeep are much more of an effort than the initial process mentioned above. Make sure you have a manufacturer or place where the rigs can be maintained that is fairly close by and has emergency service.
10. Purchasing a safe, effective apparatus to last a long time
Many fire departments can only afford to operate and replace apparatus that are 20 or 30 years old. The changes made in recent years through the use of technology are light years ahead of the older, “antique” rigs we had been using only a few years ago. Engines, transmissions, lighting, seatbelt warning systems and warning devices are just a few of the items that have made new apparatus “state of the art.” Don’t skimp on time or energy to get the best piece of apparatus you can afford that will serve your department and the citizens you protect with the best that it can be for many years and responses to come.
HARVEY EISNER is editor-in-chief of Firehouse® and a retired assistant chief of the Tenafly, NJ, Fire Department, which he joined in 1975 and served as chief of department for 12 years. He also was a firefighter in the Stillwater, OK, Fire Department for three years while attending Oklahoma State University. Eisner is an honorary assistant chief of the FDNY and program director for the Firehouse Expo and Firehouse World conferences. He has covered many major fires and disasters and interviewed numerous fire service leaders for Firehouse®. He edited the books WTC – In Their Own Words and Hot Shots, published by Cygnus.
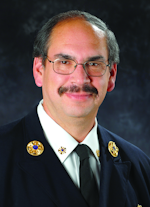
Harvey Eisner | Editor Emeritus
HARVEY EISNER was named Editor Emeritus of Firehouse® after serving 15 years as Firehouse's Editor-in-Chief. He joined the Tenafly, NJ, Fire Department in 1975 and served as chief of department for 12 years. He was a firefighter in the Stillwater, OK, Fire Department for three years while attending Oklahoma State University. Eisner was an honorary assistant chief of the FDNY and program director for the Firehouse Expo, Firehouse World and Firehouse Central conferences. He covered many major fires and disasters and interviewed numerous fire service leaders for Firehouse®