The Apparatus Architect: New Apparatus Purchasing—Five Mistakes to Avoid
We always have emphasized the importance of defining the mission of an apparatus prior to the development of specifications and to apparatus committee meetings with manufacturer representatives.
Beyond the importance of being able to justify the financial expense, we must ensure that, when the final product is placed into service, it meets the operational needs of the fire department—not just simply be the new vehicle to replace the oldest unit in the fleet.
In today’s difficult financial climate, it is more important than ever to specify apparatus that meet the needs of the response area while enhancing the safety and operation of the vehicles. Designing apparatus that serve the department and community into the future with a developed apparatus replacement program makes the procurement process go smoothly. Along the way, there are five gaffes that should be avoided.
According to plan
Lack of planning isn’t a strategy for success. Departments that rely on municipal funding—in whole or in part—must be in a position to justify their budgets, particularly with respect to capital purchases for new apparatus. Any department, regardless of the size of its apparatus fleet, should have a documented replacement plan for all vehicles. The plan should include initial vehicle cost, maintenance, fuel and insurance costs, vehicle usage, mileage, age and condition. Using this data, the department should be able to develop a profile of actual vehicle expenses to determine the annual cost of ownership for each vehicle that’s in the fleet.
Several fleet management software packages provide modules that can produce the information that’s needed to assist department personnel to quantify vehicle performance and life-cycle costing. The data then can be utilized to determine the appropriate time frame for apparatus replacement.
The program should be reviewed and approved by whomever controls the financial resources in the community. In this manner, there should be no surprises when requesting funding for new or replacement apparatus during the budget process.
Hiring a third-party expert to conduct an independent fleet evaluation might offer some value to your department.
Committee members
The expression “too many cooks spoil the broth” is appropriate with respect to personnel who serve on the apparatus committee. Too many personnel on the committee can make achieving consensus on major issues difficult.
The committee should consist of four to seven personnel. They should represent a cross section of department members and should include: company officers, drivers or engineers who will operate the vehicle; department maintenance personnel; and at least one member who has experience in apparatus procurement. Fleet managers or personnel who have an automotive or heavy-truck background can be beneficial.
The inclusion of this cross section of department members paves the way for detailed follow-up conversations and preconstruction meetings after contract.
Punitive constraints
Don’t rely on a single source for technical information.
It isn’t unusual for a department to choose one vendor as the preferred vendor out of the several prospective vendors with which it meets. The department then utilizes the preferred vendor’s specifications as the bid specifications for the new apparatus. However, virtually all apparatus manufacturers employ technical writers and engineers to ensure that some of their proprietary designs are incorporated and described in their specifications. So, using one manufacturer’s specifications—for example, requiring a 4,200-square-inch windshield as a “no exception” component, or detailing compartment depth of 25.88 inches—would be difficult to defend when reviewing other competitive proposals.
Whether your department chooses to use a manufacturer’s specification or develop its own for use in the bidding process, instances in which alternative components or design criteria can be proposed should be defined clearly. “Exceptions” should be noted in the bidder’s proposal that details what is at variance with the department’s specifications and why the requested component can’t be supplied. Where necessary, supporting technical information should be supplied for evaluation by the apparatus committee. The number of exceptions that a vendor might need to take with respect to the department’s specifications should be of lesser concern. The emphasis should be placed on the quality of the supporting technical information.
The apparatus committee should develop a detailed tool and equipment inventory, including size and weight of each item, along with the auxiliary appliances and hose load. Included with the bid specifications, this information helps to reduce the opportunity to have an overweight or out of balance apparatus once the apparatus is placed into service.
A former retail clothing store chain’s slogan was “An educated consumer is our best customer.” This is most appropriate with respect to fire apparatus marketing and sales. For example, a department develops specifications for a single-axle, 75-foot, rear-mount quint and receives multiple proposals from vendors that offer 75-, 77- and 79-foot models. Each vendor claims that its vehicle(s) meets the intent of the department’s specifications, but what is the difference among these aerial devices other than the rated vertical height? For the answer to that question, you can ask: What is the operating range of the device from above to below the horizontal? How was the vertical height measured? What is the rated tip load of the aerial device, and is this unrestricted at any elevation? What is the outrigger stance, and what are the operational limits when the outriggers are short-jacked? What is the flow rate on the aerial waterway, and what is the operating range of the aerial monitor?
Each of these operational issues has much more influence on how the aerial device can be set up and deployed at an incident—and probably more important—than the claimed vertical reach. Don’t always assume that the greater number, claimed weight loads or performance characteristics will prove to be reality.
After the bid proposals are opened, the apparatus committee should develop a comprehensive spreadsheet to identify, compare and contrast the major components and features that are on the apparatus. During the bid review process, it might be difficult to determine how a spread of, let’s say, $60,000–$80,000 can exist between bidders. Unless you read all of the details in each vendor’s proposal, you easily might be misled into thinking that each bidder is supplying exactly what your specifications requested.
Preconstruction conference
The preconstruction engineering conference is where all of the details of the vehicle are reviewed. It provides the opportunity to determine final design configurations for dashboard instrumentation, cab seating, pump panel and body compartment layouts, etc. Committee members who attend the preconstruction conference should be limited to the four or five who worked through the entire process and are in a position to make decisions on final configuration.
When possible, the department should conduct the preconstruction conference at the manufacturer’s plant. Members’ ability to tour the facility provides access to the various applicable engineering disciplines. Each discipline should provide a business card, so if issues arise during the build, you can contact the engineering segment that’s responsible for those issues. In the case of the department placing an order from a manufacturer for the first time, allow a minimum of two days on site.
Although some in the department might view the preconstruction trip as a destination vacation, nothing could be further from the truth. From personal experience assisting at hundreds of engineering conferences, an 8- to 10-hour day isn’t uncommon. At least one person should document the various discussions. Notations should be made both within the specifications and the blueprints to indicate changes and modifications that are made during the meetings.During the preconstruction conference, there should be technical documentation that was required as a part of the department’s boiler plate, including a weight analysis, an electrical load analysis, an engine performance scan and vehicle turning radius charts. The layout of adjustable shelves, trays, tool boards and other compartment accessories requires each of these to be located within a specific compartment during the meeting. If the department desires to duplicate an existing layout or observes a specific arrangement that it favors, digital images and dimensions of the compartment and equipment mounting locations assist the sales and engineering personnel. Any modification to the specifications—whether it affects the final cost or not—should be documented in a change order for approval by the department.
No shortcuts
Well-designed fire apparatus requires planning and dedicated input from each member of the apparatus committee. Departments’ satisfaction with their new vehicle(s) is the result of hard work to develop the specifications and to work with the manufacturer’s sales and engineering personnel to review and detail all aspects of the apparatus.
Changing things after a unit is built incurs considerable cost. Spending time upfront pays big dividends.
Third-Party Fleet Evaluation
Utilizing a third-party subject matter expert (SME) to analyze a department’s apparatus fleet might be advantageous.
First, generally, work with an outside consultant on developing a comprehensive fleet replacement program for all suppression and support vehicles can uncover facet of operations, maintenance records and support from available financial resources that might have eluded the department.
Second, a review that includes an SME normally uncovers unknown areas of concern with respect to corrosion issues or other maintenance issues that require attention in corrective action. It also can identify areas of safety concern, which minor enhancements to the apparatus would enable corrective action.
There can be a downside to a third-party fleet evaluation. In some instances, the fleet replacement plan that results from this evaluation initially might be at odds with the common consensus among the senior officials who are in the department. This would require follow-up discussions to address the areas of concern that the department members and other stakeholders might have.
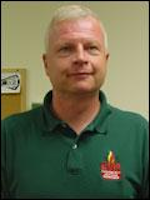
Tom Shand
TOM SHAND, who is a Firehouse contributing editor, is a 36-year veteran of the fire service. He works with Michael Wilbur at Emergency Vehicle Response, consulting on a variety of fire apparatus and fire department master-planning issues. Shand is a member of the Firehouse Hall of Fame.
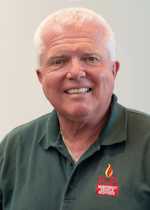
Michael Wilbur
MICHAEL WILBUR, who is a Firehouse contributing editor, retired as a lieutenant in FDNY, where he was last assigned to Ladder Company 27 in the Bronx. He has served on FDNY's Apparatus Purchasing Committee and consults on a variety of apparatus-related issues around the country. Wilbur is a member of the Firehouse Hall of Fame. For further information, access his website at www.emergencyvehicleresponse.com.