The Apparatus Architect: Apparatus Purchasing Best Practices
For many departments, the past 18–24 months presented many challenges while they continued to provide fire/rescue services to their community. The effect of the COVID-19 pandemic caused departments to alter response protocols, acquire enhanced PPE and fire station cleaning to protect personnel, and adjust training regimens, among other changes in daily shift schedules.
Apparatus cleaning and disinfection after runs became part of the daily routine, with some departments embracing the Clean Cab concept, which can provide interior surfaces that are less porous and are easier to maintain.
One of the unexpected consequences of the pandemic has been an increase in delivery lead times for new apparatus; supply chain issues for some components have affected the entire apparatus industry. Some manufacturers now propose delivery times of as much as 18 months. Chassis and component shortages also mean that apparatus committees must adjust their fleet maintenance practices.
The Apparatus Architect reached out to several apparatus fleet managers who are in the process of acquiring new vehicles to learn from their experiences during the purchasing process. Richard Riley, who is the fire apparatus manager for the Prince George’s County, MD, Fire/EMS Department, and Zachary Smith, who is the deputy chief of maintenance for the Syracuse, NY, Fire Department, provided particularly intriguing responses to the questions that were posed to the apparatus fleet managers.
Acquisition process
THE APPARATUS ARCHITECT: What process does your department utilize to acquire new apparatus: write detailed specifications vs. use a nationally recognized purchasing group, such as Houston-Galveston Area Council (H-GAC) or Sourcewell?
RILEY: Currently, we utilize H-GAC for our purchasing of fire apparatus and ambulances. Our light vehicles, such as command vehicles and support vehicles, are purchased through the county fleet department. Those vehicles then are outfitted by our Apparatus Maintenance Division (AMD) through a number of county-certified vendors for lights, lettering and additional equipment.
We do have an apparatus standard that’s mandated through a departmental general order. This order outlines, regardless of a career purchase or a volunteer corporation purchase, a standard of parts, pieces and brands that shall be used. This greatly assists the department in standardizing fleet operations and repairs and having parts in stock.
SMITH: We have a base detailed specifications for the engines, minis, trucks and rescues that we have used for purchasing. Right now, we work with vendors to use those specifications to obtain pricing from a purchasing group. We then get three or more vendors to give us their pricing based on the published options, work with them on unpublished Syracuse-specific options and then obtain final pricing from each vendor. We find this process saves us months in time versus the traditional bid process.
Furthermore, most options already are published from the purchasing groups, and the costing is much more controlled. The downside so far has been the definition of what is covered under warranty and who owns each part.
The factory trips
THE APPARATUS ARCHITECT: What recommendations do you have for conducting a factory pre-construction conference?
RILEY: This trip is very important to the final product. The amount of taxpayer dollars that goes into each piece of apparatus requires this group to be dedicated to the process.
Our current team of personnel that makes these trips is a combination of field personnel and the team from AMD. We do have a constant field team that represents the officers and drivers; then we include the station personnel where the new apparatus will be assigned.
The AMD team is well-versed in all of the apparatus and sees the problems and repairs on each apparatus that arise in the course of their daily workload. Decisions made for the apparatus on the mechanical and maintenance side of the rig is influenced heavily by the AMD team. Field personnel provide their input and opinions based on the operational methods and practices of our department.
We pay close attention to our salesperson and that person’s understanding of the product and what it can and can’t do, based on what we want the rig to do operationally or mechanically. The manufacturer can provide great information through certified engineers on how an option that we choose will operate and any negatives to our choices.
In the Baltimore-Washington, D.C. area, we also rely on information from the area’s consortium of Fire Department Apparatus Managers and Chiefs, to see what it’s doing or trying in the members’ own departments. Those people provide valuable insight into all types of apparatus, ambulances and vehicles and what’s working and what might not be working. Obtaining this information helps us make informed decisions and ask the right questions at the pre-construction meeting.
We also like to do a lot of research on the internet prior to the visit. This is to see what manufacturers and departments are building and designing on their rigs and see whether that might work on ours. Almost all manufacturers and dealers now chronicle the progress of the units they have on order with pictures and web updates each week. We certainly look at those to have ideas and questions for our meeting.
This pre-construction process isn’t the most fun of experiences. It’s a long and detailed process that requires going over every component and design on your rig. You must take people who are going to apply themselves to the process and stay engaged. How you design and spec the rig at this meeting will determine the way it’s built and will operate long into the future.
SMITH: Plan to start early and spend the entire day working with plan personnel. Also, less is more: Bringing two to three experienced department members will be more productive than bringing a large group. Answer as many questions ahead of time as possible, including in regard to graphics, paint codes, the majority of tool layouts, and radio and computer mounting. The time at the factory is too valuable to be wasted on items that should have been set in the specifications to begin with.
RILEY: We currently take the inspection team from AMD and the employee-based team from the field. This usually encompasses three or four personnel, plus the representative from the station that’s receiving the rig. We have found with this established team that they know what to look for on the inspection and have established a relationship with the salesperson and the manufacturer’s check-out team. These fostered relationships make our deliveries much easier, as all parties involved know the expectations of our team and what we want for our final product.
We were forced to do some of our inspections virtually during the pandemic. We found that this wasn’t the best way to take delivery of our rigs and ambulances. The punch list always got longer once we saw it in person, and the unit now was out of the manufacturer’s facility/plant. We always wanted the punch list to be completed by the manufacturer and not the local dealer. Although we understood the challenges faced by manufacturers during this pandemic, we wouldn’t do a virtual inspection again unless there was a mandate, such as the national emergency that gripped our country.
SMITH: The same team that does pre-construction returns for final.
There is no substitute for an in-person inspection by the department. Sales or factory staff inspections never will be as thorough. At the end of the day, they have a different boss than the fire chief.
Standardization
THE APPARATUS ARCHITECT: Does your department have a standardized design for your engines and trucks, and, if so, what would you recommend for departments to consider to achieve this goal?
RILEY: We are in our sixth year of standardization of design and equipment for our engines, trucks and ambulances. The process evaluated the apparatus, apparatus components and the equipment. This involved input from the field personnel and the mechanics at AMD.
We looked at all the parts and pieces on the rigs and determined what brands, makes and models we felt worked for our department. We wanted to easily be able to repair this equipment and, more importantly, be able to get the parts for repairs in a timely fashion.
It takes a commitment from the organization to achieve this standardization, and for someone to say, “Starting today, this is what we are going to do,” requires a financial component, evaluation period and training.
We also learned that a constant evaluation of the decisions must take place. Maybe the choice is not working as originally planned, or a newer version is available that works better. So always keep evaluating every piece of equipment or every part for its value to the maintenance or operational mission.
SMITH: We do have standardized design—which is based on our operations as much as the apparatus design itself—for a mid-mount tower, elevated waterway and rear-mount ladder. To make small, effective changes, you must have a template to work from.
Use your basic fireground operations to design an apparatus for your department and then make small changes to that design.
Wish lists
THE APPARATUS ARCHITECT: Where do you see fire apparatus engineering and design concepts moving? What would you like to see made available to enhance your fleet operations?
RILEY: Our No. 1 concept is that we would like to see an on-board system that displays for the driver/operator what exactly is wrong with the apparatus. This would display on screen what exactly is the problem that’s illuminating the “Check Engine,” “Stop Engine” or the malfunction indicator light (MIL). This display wouldn’t be in a code that has to be referenced through a code sheet or a mechanics computer but is something that the driver could tell the mechanics is being displayed on screen. This system would work for the apparatus manufacturer’s systems, the engine systems and the transmission. This would help save a lot of time and effort in the diagnosis process of an ailing or downed fire apparatus.
Wish No. 2 would be a diesel exhaust fluid (DEF) system that didn’t cause numerous problems with apparatus and ambulances. This fluid system is one of the main contributors to out-of-service apparatus and ambulances in our fleet. Even with all the training and education and preventative maintenance on these systems, they still seem to be a major problem for our units.
We are waiting to see where all of the electric apparatus go and how they will operate in a busy urban or suburban department. As systems, designs and concepts keep moving forward, we have to make sure that the manufacturers devote the time and money to ensure that mechanics are kept in the loop and are trained to fix that manufacturer’s apparatus. This training shouldn’t cost departments out of their budget; it should be offered, so we can keep that manufacturer’s rig in service and reliable. [Apparatus manufacturers] coming out with all these new things is great for the fire service, but there are a lot of items that need just as much attention as the press release and product announcement—and that’s how to fix it, how to operate it and how to maintain it.
SMITH: We are looking at aerial flight envelope controls, electronic pump interfaces and full multiplexing of apparatus becoming standard. The safety of the firefighter came to the forefront in the past few decades; now, we are adding to that increased safety through electronics and moving apparatus operations more toward the small vehicles and touchscreens that the new generation of firefighters grew up with.
We would like to see more ergonomic considerations for heavy-call-volume departments. The [expectation that 95 percent of firefighters are male in consideration of] steps, handrails, seats, etc., needs to change based on the changing demographics of the fire service.
Apparatus purchasers shouldn’t have to pay for, nor ask for, many service panels throughout the vehicles.
The OEMs should make themselves available 24/7 to remotely connect to this apparatus in any firehouse, giving the service personnel the tools to rapidly diagnose and repair these million-dollar [vehicles].
The cost of the vehicles is growing exponentially, while the number of skilled technicians, the availability of parts and the actual brick-and-mortar repair stations are decreasing. The taxpayers expect us to always be there when they call, and that should never change.
No stone unturned
The complexity of new units requires the apparatus committee to consider all aspects of the vehicle when it develops requirements for new apparatus. Much information can be gleaned from networking with other agencies, which can be applied to enhance a department’s fleet replacement program.
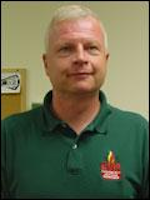
Tom Shand
TOM SHAND, who is a Firehouse contributing editor, is a 36-year veteran of the fire service. He works with Michael Wilbur at Emergency Vehicle Response, consulting on a variety of fire apparatus and fire department master-planning issues. Shand is a member of the Firehouse Hall of Fame.
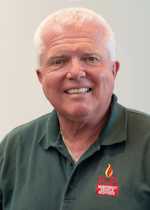
Michael Wilbur
MICHAEL WILBUR, who is a Firehouse contributing editor, retired as a lieutenant in FDNY, where he was last assigned to Ladder Company 27 in the Bronx. He has served on FDNY's Apparatus Purchasing Committee and consults on a variety of apparatus-related issues around the country. Wilbur is a member of the Firehouse Hall of Fame. For further information, access his website at www.emergencyvehicleresponse.com.