The Apparatus Architect: Soliciting Bid Proposals for New Rigs: Keys to Success
Developing vehicle specifications is a time-consuming process no matter the type of apparatus. It requires the expertise of experienced personnel as well as input from fleet mechanics, apparatus engineers and other stakeholders.
Over the years, the acquisition process changed. Once, the common practice was for a detailed specification to be written by the department without bias toward a particular manufacturer. Today, using a nationally recognized purchasing consortium, a department can choose its preferred vendor and request an array of options and configurations.
The apparatus manufacturing industry is operating with an extensive production backlog of vehicles to build, with some delivery times extending into 2027. Compared with when an apparatus could be built and completed within 12–14 months, manufacturers must project their labor and material costs several years out. If you have observed the cost of routine consumer products during the past 18 months, the effect of inflation is readily apparent. The apparatus industry is no different, with the result being double-digit increases in the cost of new apparatus.
In January 2024, the new NFPA 1900: Standard for Aircraft Rescue and Firefighting Vehicles, Automotive Fire Apparatus, Wildland Fire Apparatus, and Automotive Ambulances took effect. This will be followed by the January 2027 Environmental Protection Agency diesel engine emissions regulations. Both create an immediate effect on availability. Several of the most common diesel engines in various horsepower ratings no longer will be produced. (The replacement models still are under development at this point.)
Given the effect of inflation, along with frequent adjustments that can be expected in material costs, departments that are soliciting bids for new apparatus will find that, in some cases, the proposal price that’s offered likely will be firm for a period of 30 days or fewer.
Start early
Fleet managers and those who are responsible for the procurement process must develop and update their apparatus replacement plans to align with the extended delivery schedules and anticipated final costs. The planned life cycle for front-line and reserve units must be adjusted. This results in extended service life along with increased repair and maintenance costs, to keep vehicles in good condition and in conformance with NFPA 1910: Standard for the Inspection, Maintenance, Refurbishment, Testing, and Retirement of In-Service Emergency Vehicles and Marine Firefighting Vessels. When the financial resources aren’t sufficient to adequately fund the replacement schedule for apparatus, it’s imperative that chief officers work with internal and external stakeholders to adjust the replacement plan, to ensure that it can be implemented.
Whatever methodology your organization utilizes to procure new vehicles, plan to start the process early to avoid unanticipated price increases as well as to secure a production slot for the apparatus. The planned life cycle for the replacement unit shouldn’t be predicated on who can build the rig the fastest, nor should you favor a preferred vendor that can’t provide a fixed price for the unit or requires a prepayment without providing a performance bond to protect the monies that are paid to it.
Although using a purchasing consortium to select your preferred vendor ensures that you will obtain the model of vehicle that’s desired, this might not provide the lowest price for the vehicle, depending on the design and configuration. Fleet standardization should be the goal, particularly with respect to hose, tool and equipment layouts, major components and vehicle dimensions. What’s standard in your fleet with respect to electronic components, pump panel instrumentation and valves, along with major chassis components, should be incorporated into the final version of vehicle specifications.
Customization
With the rising cost of new apparatus, consideration should be given to reviewing the configuration of your engine and ladder company units with respect to the degree of standardization versus customization to achieve the desired result. An analysis of how the final cost of the apparatus rolls up based on the degree of customization and one-off engineering projects provides valuable information on which to make sound decisions.
For example, your current engines might have bumper hose trays to accommodate preconnected attack lines that have a specific dimension. However, you might find that this varies from the manufacturer’s standard dimensions, even if by a small amount. The result of this tray design to meet your specifications costs almost double that of the standard design. It’s difficult to remove personnel preferences and opinions when discussing apparatus design, but the degree of customization affects the overall cost.
What’s standard equipment in your fleet might not be standard with your preferred manufacturer. To alleviate issues at the preconstruction meeting when the planned configuration and components might not be available, consider meeting with the sales engineer prior to contract to review the specifications from bumper to back step to confirm that the unit can be built as planned.
With the extended delivery times, the date for the preconstruction meeting might not take place for some time after the contract is awarded. Some components, particularly vehicle lighting and electronic equipment, might be out of date when the unit goes into production. Some of the enhancements to components that were implemented after the preconstruction meeting might be offered at little or no cost increase when compared with the originally desired model. However, if a significant amount of time passed between the contract signing and the preconstruction meeting, you can anticipate increased costs for the replacement component.
Each apparatus project should have a contingency fund that can be utilized with discretion as needed to absorb the cost of change orders at the preconstruction meeting and for unanticipated changes during the production cycle. Changes made after this point should be discouraged, because they become increasingly costly and can delay the planned completion of the new apparatus.
Time and initiative
If your department desires to obtain competitive bids for your new rig, the preferred method is to develop your own specifications to include requirements for technical documentation, warranty terms, training, delivery and acceptance, among other items. Submitting a list of critical apparatus dimensions, including overall length and height, wheelbase, cab and body lengths and hosebed heights, provides guidance for manufacturers to follow. This information, along with a technical description of the principal components on the vehicle, gives a prospective bidder everything that it needs to provide a proposal.
Unfortunately, because of the increased usage of consortium contracts and bids that are awarded using tag-on provisions, fewer departments develop their own technical specifications and instead rely on input from outside resources. That said, if your department takes the time and initiative to develop apparatus specifications that are tailored to meet your and your members’ needs, the proposals that you will receive will provide an opportunity to discern the degree to which the manufacturers’ specifications deliver what you requested, probably with a wide variation in cost and number of exceptions or clarifications to consider.
We recently encountered a department that bid a custom chassis, 1,500-gpm engine that has a short wheelbase, a low rear hosebed, and a specific range of dimensions to cover the maximum overall length and height in conjunction with fire station limitations. Several bidders noted compliance with the dimensional requirements. However, when the department evaluated one of the blueprints that was submitted with the proposal, it found that the vehicle would exceed the height and length requirements. Similarly, a specific make and model of valves on the fire pump were listed for each discharge by the department, including the preferred method of actuation. Of the five bids that the department received, only one manufacturer offered exactly what was specified; the others offered what was considered as standard for their apparatus builds—and didn’t note an exception or clarification as to why the requested valves wouldn’t be supplied.
Continual updating
No one manufacturer may be able to provide 100 percent of a department’s desired design. However, conducting a prebid conference to allow prospective vendors to comment on your requirements can afford a forum for a healthy exchange of information for all parties. Working on apparatus-related projects, whether on a new unit or evaluating the fleet for rebuild candidates, is a time-consuming project and must be updated continually to keep pace with changes in the apparatus industry as well as government regulations that affect how you operate and maintain your services to the community.
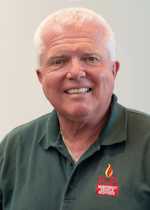
Michael Wilbur
MICHAEL WILBUR, who is a Firehouse contributing editor, retired as a lieutenant in FDNY, where he was last assigned to Ladder Company 27 in the Bronx. He has served on FDNY's Apparatus Purchasing Committee and consults on a variety of apparatus-related issues around the country. Wilbur is a member of the Firehouse Hall of Fame. For further information, access his website at www.emergencyvehicleresponse.com.
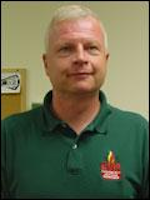
Tom Shand
TOM SHAND, who is a Firehouse contributing editor, is a 36-year veteran of the fire service. He works with Michael Wilbur at Emergency Vehicle Response, consulting on a variety of fire apparatus and fire department master-planning issues. Shand is a member of the Firehouse Hall of Fame.