Specifying a New Apparatus: Don’t Waste Money on Unnecessary Items
Note: This article is part of the Firehouse 2024 Apparatus Supplement. To read the entire supplement, click here.
Consider this: An apparatus committee convenes for the first of what will be numerous meetings to assemble specifications for a new apparatus. It was made clear to the committee that costs for new apparatus are at an all-time high and that the committee members absolutely must keep the cost of the department’s new apparatus as reasonable as possible. Historically, the volunteer side of the fire service has more flexibility when it comes to the matter of budgeting. However, with the cost for funding public safety these days, that’s situation is changing. This isn’t an easy directive to follow, given the complexity of today’s apparatus. How does an apparatus committee accomplish this task?
Multiple considerations
It often is at least 15–20 years that passed since a piece of apparatus that’s to be replaced was put into service at a department. In what ways have the various aspects of the fire protection district changed over those couple of decades?
Don’t downplay the importance of the answer to this question. Districts change over such a period of time, sometimes more than apparatus committee members realize.
Next, move to the apparatus that’s being replaced. My recommendation is that all of the members of the committee do this on their own, because each of them will have different answers to questions.
- What on the apparatus works and what doesn’t for the department’s current operations?
- What functions/features/components must be carried forward to the new apparatus?
- What functions/features/components shouldn’t be carried forward to the new apparatus?
- What is lacking on the current apparatus that must be incorporated into the new apparatus?
Be brutally honest going through these steps. The answers to all of these questions are going to have a big effect on developing a specification that serves the needs of the protection district today and throughout the life of the vehicle.
Stay focused
Multiple apparatus salespeople/representatives will (or should) visit to discuss their company’s products and offerings. These meetings can be a valuable source of information. Exploit that.
Two different classifications of items will become apparent quickly: needs and wants. Needs are features and components that should be included in the apparatus. Wants are things that somebody desires but have little value operationally and add to the overall cost of the vehicle. Some committee members will pitch their wants as “needs.”
How do apparatus committee members navigate through this process successfully? Understand your responsibilities. From the sales side, this is a business. Make no mistake about that. Salespeople are friendly, engaging and knowledgeable about their product, as it should be. However, their responsibilities and loyalties are to their dealership, also as it should be. The members of the apparatus committee must remember that they also are in a business transaction and, therefore, must maintain a professional relationship with all of the people who are involved from the beginning of the process to its end. That said, the committee is spending taxpayer dollars and, therefore, is involved in a legal process that has protocols and procedures that are detailed in state, county and local procurement laws.
Staying on point is difficult. As they move through the specification development process, apparatus committee members can do several things to ensure that their department gets the apparatus that serves its needs and to assist in keeping costs from running away. Keep in mind that every decision that the apparatus committee makes and every line that its members put into a specification have a cost associated with them. Furthermore, every decision can create a domino effect on other factors.
Looking back on budgeting, municipalities that are served by volunteer departments tend to be more lenient on their department than municipalities that are served by career departments are on theirs, but that creates challenges. Below are the most common ones that I encounter. Although volunteer departments certainly don’t have the market cornered on these items, experience has taught me that these challenges are more prevalent with volunteer departments and can affect the cost of new apparatus significantly.
‘That’s what it’s always been’
This viewpoint isn’t limited to any one aspect of a piece of apparatus, and it’s something that many apparatus committees seem to latch onto.
There are times when it’s appropriate to consider the reasons to hold on to some department traditions, but planning the functional and operational aspects of new apparatus isn’t one of those times.
What the department protects, how many members turn out to respond, how and on what the members train, and the amount and types of responses all change. Along with those changes are the changes in and capabilities of apparatus. Is a two-stage fire pump being specified because the department always had one? The department might not need one with today’s single-stage pumps and diesel motors. Two-stage pumps are more expensive than a single-stage version. Further, two-stage pumps have more internal moving parts and require more maintenance, and pump operators need a higher level of training. So, not only does the specification of a two-stage pump cost more initially, it costs more every year that a department owns that pumper. Extrapolate that mindset over the entire vehicle.
Mutual aid
It isn’t an apparatus committee’s responsibility to design and equip new apparatus or to spend taxpayer dollars to protect another community. The committee’s responsibility is to design and specify apparatus for its department’s protection area. That said, this changes when a signed intermunicipal agreement for shared services is in place.
What if …?
An apparatus committee can “what if” itself into countless situations, and this has cost may fire departments lots of money, with no real return on investment and plenty of headaches.
You must understand and accept that a department never can prepare for every incident that it will encounter.
Along those lines, if an incident is unusually large and/or complex, one piece of apparatus probably won’t make a difference operationally or in the outcome.
Say an apparatus committee insists on a Type B foam system that delivers 3 percent concentration at 1,000 gpm. Why? “We have a tire wholesaler who has a warehouse in town that’s stacked floor-to-ceiling with tires.” Getting past the fact that tires are a Class A fire, the committee offers up a second reason: “The train yard has a diesel repair shop on the property.” OK, but does the railroad have a Type B foam on the property for the department’s use? “No, we asked them to do that, but they refused.”
The “what ifs” could go on for pages and include stories about hugely oversize electric generators that are used to power certain buildings in a power failure. There might be more foam stories and discussion about complex HRT systems on heavy rescues and items on tool lists that are questionable. All of this doesn’t address the operational challenges.
What’s more, the department relies on its county’s training center to supply the additional foam for “what if” scenarios. It takes 60–90 minutes to reach a scene, and they can make foam at maximum flow for 2 minutes and 20 seconds.
Be realistic about what’s requested on apparatus and whether it can be supported operationally. Unless all of the secondary requirements that are needed for the “what if” scenario to be successfully managed and mitigated are considered and planned, putting a “what if” into operation and supporting that operation until the completion of the incident probably won’t be possible.
Three areas of lighting
Operational lighting (headlights, turn signals, marker lights, cab interior lights and all other Department of Transportation (DOT)-required lighting) is the first area of apparatus lighting. As the purchaser, a department has options as to the make and model of different fixtures as long as they meet DOT requirements.
More time and energy is spent on the second area of apparatus lighting—emergency lights—than on any other part of the apparatus.
Is a $ 7,000 light bar needed? Backed up by two minibars over the cab crew doors?
How many lights must be on each side of the apparatus? Is the back of the apparatus so well-lit that drivers who arrive after the new apparatus is on scene are blinded?
Educate yourself. Take the lighting supplier catalogs away from members or members who want everything that’s in the book.
The third area of apparatus lighting is scene lighting. It has improved in the past several years and took a giant leap with LED lights.
Do product research. Several lighting manufacturers make excellent products that are competitively priced and are backed by good warranty programs.
Recently, I compared two competitors’ models of a particular 12-volt scene light. There was about a 1,600-lumen difference between the two fixtures. The level of output of the fixtures was negligible. What wasn’t negligible was the $1,800 per fixture price difference between the least expensive and most expensive fixture. Specify two of the more expensive fixtures on each side of a vehicle and two on the back and a committee costs its department $10,800.
Trends in apparatus
The blackout package has been one of the biggest trends over the past few years. Put another way, it’s a fad, and fads fade. In addition, like so many other decisions, specifying a blackout package might have unintended consequences. A blackout package weighs about 0.75 lbs./sq. ft. when applied at a thickness of ⅛ inch.
Bigger isn’t always better
Does the department need that 15-liter motor on the new apparatus? It might for certain applications in the fire service, but those applications are more exceptions than the rule.
That 15-liter motor weighs about 1,000 lbs. more than its 12-liter cousin. That’s a big load difference on the front axle of the apparatus.
Is the 8- or 10-man cab still being considered despite the fact that it rarely, if ever, is full?
Each of the considerations that are noted above are expensive. Furthermore, any one of them could push a specification into heavier axles, bigger brakes and bigger tires because of the weight that’s added to the vehicle. Besides adding even more to the cost of the apparatus, the additional weight can change the way that the vehicle drives.
In the know
Review the department’s responses over the past 20 years, so the types and quantities of calls are known. Specify and build to what’s needed to serve and support the department’s operations.
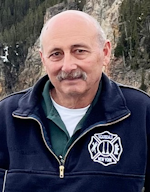
Jeffrey D. Gaskin
Jeffrey D. Gaskin is president of Big Red Trucks Fire Apparatus Consultants. He is a retired captain from the Scarsdale, NY, Fire Department. Throughout his career, Gaskin has been involved in apparatus acquisitions, from needs assessment through specification-writing. He also is a fire apparatus mechanic and holds certifications from Allison Transmission, Detroit Diesel, Hale Pump, Smart Power, Spartan Chassis, Sutphen Fire Apparatus and others. Gaskin is certified by the Emergency Vehicle Technician Certification Commission in six areas: Fire Apparatus Inspection, Maintenance and Testing (F-1); Design and Performance Standards of Fire Apparatus (F-2); Fire Pumps and Accessories (F-3); Aerial Fire Apparatus (F-5); Allison Automatic Transmission (F-6); and Hydraulic Systems (F-8). He can be reached at [email protected].