The negative implications of an unorganized fire station might run a close second to the negative implications of an unorganized firefighter. Given that the apparatus bay typically is one of the largest areas in a firehouse, keeping it efficient and clean is crucial to how a department functions. Thankfully, companies that specialize in apparatus bay storage are putting their best foot forward to come up with ways that they can aid their fire service partners to achieve an optimized and orderly space. This includes products and strategies that pertain to turnout gear, SCBA and spare hose.
Big on brawn
Although the physical strength of Groves’ Ready Rack locker systems that the Cary, IL, Fire Protection District (CFPD) employed in its apparatus bay for decades never disappointed, the vendor’s investment in increasing the lockers’ robustness falls right in line with what CFPD Assistant Chief Brad Delatorre has experienced from his regular communication with the company.
“They’re always eager to hear our feedback,” Delatorre tells Firehouse. “We can call them for retrofitting for some additions or just remodeling, and they always are eager.”
Compared with the original Ready Rack system, the durability of Red Rack mobile, wall-mounted and freestanding lockers was increased. Furthermore, the lockers provide more versatility, because departments have flexibility in their specification of width and depth.
The collaboration between the CFPD and Groves also extended to the department’s desire to incorporate ways to afford the potential for enlarging storage capacity to accommodate future needs. Delatorre says Groves didn’t hesitate to figure out methods that its racks could be configured for that purpose.
The open-air architecture of the original Ready Rack system and how it helped with gear management always has been well received, but mobility has been sought increasingly more. Departments are able to alter the height of each individual shelf within their locker and build more shelves per area using Red Rack. The Red Rack system also can be quickly converted into a security unit, which wasn’t possible with the original Ready Rack system.
Groves President Kristine Thune says that the ever-changing needs of the fire service are at the heart of her company’s and its products’ continuous evolution. Leading the way in “innovative storage solutions for fire departments” always has been the goal, Thune adds.
Although the fire service continues to recognize that a separate turnout gear room is a wise station design decision—including to keep turnouts away from direct sunlight and UV rays, which can damage the garments over extended periods of time—many older stations don’t yet have that luxury. Hence, Groves’ development of a custom cover to protect turnout gear from UV rays.
“UV radiation from the sun degrades the fibers and protective barrier on the gear,” Thune notes. Groves’ custom cover helps extend the life of turnouts, she says.
Exposing turnout gear to direct sunlight for an extended period causes it, as with most clothes, to fade and to weaken the strands that comprise it, Thune explains. When the fibers on the PPE clothing begin to break down, a firefighter’s risk of injury increases.
Groves created something that would fit perfectly over the lockers to filter out UV lighting while still being sturdy enough to withstand the harsh conditions of the firehouse. Groves decided on a PVC laminate material that was long-lasting but also waterproof, tear-resistant, antimicrobial and self-deodorizing.
“Groves cut, sewed and stitched them to suit our lockers,” Delatorre says.
Hose storage
When the Fort Atkinson, WI, Fire Department began the final work on its newest facility, methods to minimize damage to turnout coats, boots and gloves, including spare items, were prominent matters of consideration. The solution: Spacesaver’s high-density mobile storage (HDMS) system.
Maximizing hose storage capacity was a goal as well. Spacesaver, which also is headquartered in Fort Atkinson, custom-manufactured a shelving
solution for the hose that not only provides high-capacity storage but also makes access to the hose easy for the department’s members.
According to Spacesaver’s Jacob Carter, the system stores twice as many hoses while requiring less floor space.
The Fire Hose Rack System accommodates 1½-, 1¾- and 2½-inch handlines and keeps them upright and rolled, to prevent any sharp edges from touching the hose.
The design of the system provides for expandability via 24-, 30-, 36-, 42- and 48-inch-wide sections that can be relocated and reconfigured. A canopy top acts as a dust shield to keep hoses cleaner than they would be without it and provides space for additional storage when reinforced.
SCBA storage
When the Roseville, MN, Fire Department (RFD) was designing a new station to replace three small, outdated stations, reducing repetitive trips to and from apparatus in the process of refilling SCBA cylinders was a goal. RFD Assistant Chief Neil Sjostrom tells Firehouse that GearGrid was consulted. The result was the department’s purchase of the supplier’s mobile SCBA storage unit.
“The system ensures safe storage and movement of our spare cylinders,” Sjostrom says.
Although one might conclude that the setup of a system whose purpose is simplistic in functionality is equally simplistic, that couldn’t be further from the truth.
“GearGrid provided invaluable assistance for the system’s proper installation,” Sjostrom notes.
He tells Firehouse that his department never really considered the importance of properly storing spare cylinders and air packs. Further complicating matters, the department’s fleet has been downsized. Where once everything was stored on apparatus, in-bay storage of the most innovative sort was required to relocate cylinders and air packs from vehicles to a fixed location.
“We didn’t identify on the front end the need to properly store this equipment both safely and in a manner that was space-conscious,” Sjostrom admits. “It was GearGrid’s suggestion that we employ their mobile storage cabinet for these two items as part of our conversations with them about storage needs.”
The devil is in the details
GearGrid’s emphasis on order and organization in the apparatus bay is all-encompassing, down to what some might consider the most mundane of facets in the area. The company’s Broom & Wash Center was conceived and designed with the goal of providing “the ultimate modular and flexible solution” for storing the tools and implements that members need to keep the bay neat—although it also can be used for holding gear for special, non-fire incidents.
The attention to detail that GearGrid, Groves and Spacesaver—and other experts that operate in the same space—apply to serve the needs of fire departments should serve as inspiration to members of all ranks to leave no stone unturned. Opportunities to organize apparatus bays afford the means to add to efforts to increase the safety of firefighters and the efficiency of operations.
Hose storage
When the Fort Atkinson, WI, Fire Department began the final work on its newest facility, methods to minimize damage to turnout coats, boots and gloves, including spare items, were prominent matters of consideration. The solution: Spacesaver’s high-density mobile storage (HDMS) system.
Maximizing hose storage capacity also was a goal. Spacesaver, which also is headquartered in Fort Atkinson, custom-manufactured a shelving solution for the hose that not only provides high-capacity storage but also makes access to the hose easy for the department’s members.
According to Spacesaver’s Jacob Carter, the system stores twice as many hoses while requiring less floor space.
The Fire Hose Rack System accommodates 1½-, 1¾ - and 2½-inch handlines and keeps them upright and wound, to prevent any sharp edges from touching the hose.
The design of the system provides for expandability via 24-, 30-, 36-, 42- and 48-inch-wide sections that can be relocated and reconfigured. A canopy top acts as a dust shield to keep hoses cleaner than they would be without it and provides space for additional storage when reinforced.
SCBA storage
When the Roseville, MN, Fire Department (RFD) was designing a new station to replace three small, outdated stations, reducing repetitive trips to and from apparatus in the process of refilling SCBA cylinders was a goal. RFD Assistant Chief Neil Sjostrom tells Firehouse that GearGrid was consulted. The result was the department’s purchase of the supplier’s mobile SCBA storage unit.
“The system ensures safe storage and movement of our spare cylinders,” Sjostrom says.
Although one might conclude that the setup of a system whose purpose is simplistic in functionality is equally simplistic, that couldn’t be further from the truth.
“GearGrid provided invaluable assistance for the system’s proper installation,” Sjostrom notes.
He tells Firehouse that his department never really considered the importance of properly storing spare cylinders and air packs. Further complicating matters, the department’s fleet has been
downsized. Where once everything was stored on apparatus, in-bay storage of the most innovative sort was required to relocate cylinders and air packs from vehicles to a fixed location.
“We didn’t identify on the front end the need to properly store this equipment both safely and in a manner that was space-conscious,” Sjostrom admits. “It was GearGrid’s suggestion that we employ their mobile storage cabinet for these two items as part of our conversations with them about storage needs.”
The devil is in the details
GearGrid’s emphasis on order and organization in the apparatus bay is all-encompassing, down to what some might consider the most mundane of facets in the area. The company’s Broom & Wash Center was conceived and designed with the goal of providing “the ultimate modular and flexible solution” for storing the tools and implements that members need to keep the bay neat—although it also can be used for holding gear for special, non-fire incidents.
The attention to detail that GearGrid, Groves and Spacesaver—and other experts that operate in the same space—apply to serve the needs of fire departments should serve as inspiration to members of all ranks to leave no stone unturned. Opportunities to organize apparatus bays afford the means to add to efforts to increase the safety of firefighters and the efficiency of operations.
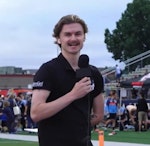
Ryan Baker
Ryan Baker is a writer and associate editor with prior experiences in online and print production. Ryan is an associate editor for Firehouse with a master's degree in sciences of communication from the University of Wisconsin-Whitewater. He recently completed a year of teaching Intro to Public Speaking at UW-Whitewater, as part of his graduate program. Ryan acquired his bachelor's degree in journalism in 2023 from UW-Whitewater, and operates currently out of Minneapolis, MN. Baker, also writes freelances for the Ultimate Frisbee Association (UFA) in his free time, while also umpiring baseball for various ages across the Twin Cities Metro Area.