Improving Apparatus Maintenance with Thoughtful Specs
Proper maintenance of apparatus begins with good specifications and picking a manufacturer that values quality engineering and use of quality components.
Fire apparatus continues to get more complex and high-tech year after year, and manufacturers are constantly looking to make maintenance easier for firefighters and mechanics.
“E-ONE believes that providing adequate service access is a key element in product design and development,” said Joe Hedges, Product Manager for E-ONE, one of the nation’s largest apparatus builders, based in Ocala, FL. “Hinged pump panels are available to provide greater access to plumbing [and other] components.”
For those specifying apparatus, selection of body material can make a big difference in the future maintenance on fire trucks.
At Midwest Fire, an apparatus builder in Luverne, MN, bodies and tanks are constructed from polypropylene.
“That means apparatus bodies and tanks are going to be maintenance free,” said Brett Jensen, vice president and general manager of Midwest Fire. “That means there’s no rust or corrosion. And, you can take a sledge hammer to it and you’re not going to dent it. For a body material, it doesn’t get any better.”
Paying Attention to Details
Some apparatus builders, like E-ONE, pay attention to details that help with long-term maintenance.
Hedges said the company has standardized mechanical pump seals in place of pump packings, which require regular adjusting to prevent leaking, thus eliminating a maintenance item.
E-ONE has also started using maintenance-free bushings in place of pins that require routine greasing, Hedges said, adding that E-ONE has also moved to Torx fasteners throughout the apparatus construction, which are less likely to strip than Phillips head fasteners.
Hedges said E-ONE makes “every effort to provide access to manual overrides on electric valves.”
And speaking of electric components, Hedges said E-ONE and IDEX, in a joint project, developed AXIS Smart Truck Technology which is standard on all custom chassis apparatus.
“AXIS is connected to major vehicle electrical systems to provide real-time information relative to the health of the apparatus that can be accessed from any web enabled device,” Hedge said.
At Midwest Fire, Jensen said virtually every apparatus they build has multiplex as a standard electrical system. Multiplex allows for on-board apparatus diagnostics through a series of wires and nodes located throughout the truck.
“Rural departments don’t generally have maintenance people on staff,” Jensen said. “With multiplexing, they can jump right in push a few buttons, do some troubleshooting and then do the repairs.” He added that multiplexing will also designate exactly where an electrical fault is located.
Designed for Easy Maintenance
Some apparatus at Midwest Fire have some “old-school” hard wiring which is very easy to diagnose, Jensen said.
“We are doing mostly tanker/pumpers and we are trying to make them as simple and easy to maintain as possible,” Jensen said.
As firefighters and purchasing agents specify apparatus, they should keep in mind future service requirements.
“Often, manufacturers are asked to provide options or compress areas like a pump modules that can compromise service access,” Hedges said. “Awareness and respect for preserving required service access should be paramount for both customers and manufacturers when developing custom built apparatus.”
Jensen, who has been in the fire truck business for 26 years, said he has seen some horrendous designs for pump houses and panels as firefighters try to squeeze so much equipment into as little space as possible.
“Sometimes things are so packed in, you can't even fit an arm in there,” Jensen said.
That’s why Midwest Fire tries to standardize the pump house size and layout as much as possible, Jensen said.
“If we run into problems with length restrictions, we’ll shave a little off the body, or lose some compartment space,” Jensen said. “We’d rather do that, rather than short the pump house.” He added that if customers are insistent, Midwest Fire will meet their requests without compromising safety and with the customer’s full understanding of a spec decision's potential impact.
Building on Frames, Not Around
Jensen said Midwest Fire, which builds the majority of its apparatus on commercially available cabs and chassis, designs and builds bodies and installs fire equipment on the frame rails rather than around them, which means components that need servicing are fully accessible, as designed by the Original Equipment Manufacturer (OEM). That means spring shackles and lubrication points are not obstructed by any fire equipment installed after the chassis is built.
When obstruction is unavoidable, both E-ONE and Midwest Fire build in access panels to restore accessibility for maintenance and repairs.
Jensen said Midwest Fire has very large removable panels that provide access to pump and plumbing equipment.
As a custom cab builder, E-ONE makes its own cabs and chassis and Hedges said the company has hinged overhead consoles in the cab for easy access to repair, or add, any components as necessary.
Midwest Fire, which uses commercial cabs and chassis, has less custom components in the cab, but does make it custom center console, Jensen said, adding that fire related equipment contained within it is accessible by a hinged top.
The center console in the cab is about the only significant modification Midwest Fire makes to commercial cabs and chassis, Jensen said, adding that it’s never a good idea to make too many modifications, especially to frames.
“We try to never modify a chassis,” Jensen said. “You run into warranty issues. Besides, they are the professionals. They have hundreds of people to engineer and build the frames.”
The same goes for front bumper extension, Jensen said. He said Midwest Fire always tries to have the cab and chassis manufacturer custom build the truck with extended front frame rails.
“That’s the best, when we can get them from the manufacturer,” Jensen said, adding that it’s not always possible and the company has to fabricate the bumpers from scratch. When that happens, Midwest Fire puts everything back the way it was from the factory, especially tow hooks, he said.
Routine Maintenance Still Required
No matter how much attention fire truck purchasers pay to specifying apparatus, there’s no such thing as a maintenance-free truck.
Hedges said it’s vitally important for firefighters and mechanics to follow the manufacturer’s recommended service and inspection intervals for the entire apparatus, including the chassis, pump, plumbing, aerial, generators and all other components.
“This includes not only fluid level check and filter changes, but also inspection of brake pads and shoes, cleaning and lubrication of the aerial, for example,” Hedges said.
Hedges said batteries are critical components to monitor and digital battery analyzers can be used to determine not only if the battery is good, but also its remaining life.
“With the battery banks used in today’s apparatus, one dead battery may go undetected, but may, in some cases, start draining the life out of the other good batteries,” Hedges said.
Other general items that need routine checking are tire pressure, which can be monitored with a simple valve stem indicator, or electric readouts in a multiplex system, and air cleaners which need to be replaced or cleaned at recommended intervals.
Hedges also said apparatus maintenance personnel should use de-icing agents on the vehicle underside thoroughly each Spring.
“This should be done routinely if [apparatus] is used in coastal cities where ocean salt water can be present on roadways,” he said.
And, if the vehicle is used in high water, fluids need to be checked for contamination and replaced as needed, while always using the manufactured recommended fluids and lubricants.
Apparatus Familiarity
Jensen said it’s important that firefighters and mechanics be familiar with the routine maintenance of their apparatus. That’s why he advocates factory training.
“We do our deliveries right here at the factory,” Jensen said. “Customers come here and we go through everything from top to bottom. We try everything out in the test bay and train them on how to access things and how to maintain them. It’s all part of preventative maintenance.”
Jensen said Midwest Fire has employees that service apparatus the company builds in a five-state area and the technicians pass along discoveries they make in the field to the engineers.
“They have no problem coming in and saying 'This is a poor design and you need to fix it,'" Jensen said. “So we do. I don’t think we could get away with making our truck anything but accessible for maintenance.”
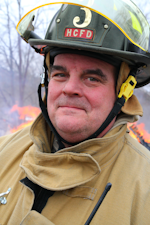
Ed Ballam
Ed Ballam served as associate editor for Firehouse. He is the assistant chief of the Haverhill Corner, N.H. Fire Department, and a National Registered EMT. He is also a Deputy Forest Fire Warden for the New Hampshire Division of Forests and Lands. Professionally, he's been a journalist for over 35 years working for a variety of publications, including employment as managing editor of a national fire service trade journal for more than a decade.