Centrifugal Fire Pumps: Single-Stage vs. Two-Stage
Centrifugal fire pumps long have been the backbone of pumping apparatus in the fire service because of their efficiency and their versatility. They come in various configurations, so departments must choose the configuration that best meets the needs for their fire suppression challenges (structural, high-rise, industrial, wildland, refineries, etc.).
When choosing a configuration, the first decision must be based on the need for a single-stage pump or a two-stage pump.
Unlike positive displacement pumps, centrifugal pumps must have either a priming system or a positive pressure water source that’s introduced to evacuate air out of the pump.
Centrifugal pumps use incoming water pressure to adequately supply firefighting operations. Depending on the speed of the impeller, add discharge pressure can be added. If your firefighting situation requires 175 psi pump discharge pressure and your incoming water pressure is 75 psi, then the pump only needs to work hard enough to generate an additional 100 psi of discharge pressure.
Careful analysis required
Single-stage fire pumps, as the name implies, have a single impeller. The impeller size dictates the discharge capacity of the pump. These impellers can have a single eye (inlet) or dual eyes. The number of eyes doesn’t affect pump capacity (see Table 1). The highest-capacity pumps are pedestal-types that have single-eye impellers.Single-stage pumps don’t have a transfer valve nor internal flapper valves to direct water flow, which translates to fewer moving parts. Fewer moving parts translates to less expensive to manufacture, which reduces cost to the purchaser, less maintenance and less operator training.
Two-stage pumps have two impellers on a common shaft, and both impellers have a single eye. There are two modes of operation: capacity, which also is called parallel, and pressure, which also is called series. The operational modes describe how the pump impellers operate.
In capacity mode, intake water flows into both impeller eyes simultaneously (working in parallel) and then is discharged into the discharge ports on the discharge side of the pump. In pressure mode, water enters the eye of the first impeller, which develops the first half of pump discharge pressure. The water then is discharged from the first impeller into the eye of the second impeller, which develops the second half of the pump discharge pressure (working in series).
Changing the operation mode is done with the transfer valve. As the transfer valve is actuated and the water flow inside of the pump changes, two flapper valves close to cut off the capacity flow path and redirect the water internally. Operating in pressure mode cuts the rated discharge capacity of the pump in half (see Table 2).With more moving parts, the two-stage pump is more complex to build, which increases cost and maintenance. Training pump operators on a two-stage pump is more time consuming than training that’s involved with single-stage pumps, and the department must have protocols in place and reinforced by training on pump operations.
Two excellent online videos that were produced by Waterous show water flow paths through a single-stage full-bodied pump and a two-stage full-bodied pump (watch them below).
Single-stage full-bodied pump
They are great to help to understand the flow of water in each of these pumps. Darley and Hale use slightly different routes and transfer valve models in their pump bodies that are based on their design and engineering standards, but the basics are the same. US Fire Pump currently only makes pedestal-type single-stage pumps.
Increased horsepower and torque
Two-stage pumps were the norm in the fire service for decades. This began to change late in the 1980s, as diesel engine technology improved. These improvements were driven largely by the need to make diesel engines more environmentally friendly. As design and operational changes were made, available horsepower and torque increased. The differences between the available horsepower and torque of the old-technology diesel motors and the available horsepower and torque of today’s diesel motors is illustrated in Table 3.The improvements in diesel motor performance has allowed the migration to single-stage pumps from two-stage pumps. Higher horsepower and torque ratings on the newer engines enable the single-stage pumps to operate more efficiently.
Current industry estimates are that approximately 85 percent of the fire pumps that are sold today are single-stage pumps. About 30 percent of the single-stage pumps are pedestal-type. Pedestal-type pumps are centrifugal pumps that lack an intake and discharge body. The pump is an impeller that’s enclosed in a housing that has an intake inlet and a discharge outlet. The apparatus builder must design and fabricate all inlet and discharge waterways. Examples would be the Darley ZSM-2500, the Hale 8FG, the Waterous S-100 and the US Fire Pump HVP.
Single-stage pumps are more efficient at higher flow rates and less efficient at higher discharge pressures. If high fire flow rates are required, it’s the application (amount) of extinguishing agent that extinguishes, in which case a single-stage pump would be the better application. If high pressures are needed to move water through long lays of small diameter hose (wildland) with lower flow rates, then a two-stage pump might be a better application.
Some departments choose two-stage pumps because of their flexibility to pump high pressure/low volume or high volume/lower pressure. However, a careful analysis of a department’s needs might determine that today’s single-stage pumps adequately will deliver the performance that the older two-stage pumps that have less-efficient engines did. Two-stage pumps are more efficient at higher pressures but lose efficiency at high flow rates. Furthermore, if firefighting applications require very high flow rates (typically in excess of 2,000–2,250 gpm), then today’s larger, single-stage, pedestal-type pumps probably are a better option.
Response area data
How does one decide on what’s best for a response area? Don’t necessarily specify “what always was used.” Talk to pump manufacturer representatives about their product offerings, consider single-stage versus two-stage performance, ask lots of questions, attend training on pumps and get educated, so an informed decision can be made. Take stock of your response area:
- What is the height and type of construction of the tallest building?
- What is your typical incoming hydrant pressure?
- What is the typical layout of your suction and discharge hose diameters and lengths at the fire scene?
- What types of nozzles does your department use to apply the extinguishing agent?
With this data, one should be able to calculate the required flow and pressure from the pump to deliver an adequate water supply to keep the firefighter safe and to control the fire on the highest floor of a building. The needed water supply can be compared with the pump manufacturer’s data sheets, to provide direction on whether a single- or two-stage pump is required.
Rural departments should keep in mind that an elevation change in topography is no different than an elevation change that’s created by a building. Put another way, 200-foot vertical change that’s encountered while trying to supply water to the 20th floor of a building is no different than a 200-foot vertical change that’s dictated by a steep roadway.
Single-stage pumpers in series
In the early 2000s, Hale conducted field tests at buildings in Chicago and San Diego to get some hard data regarding what could be done with both single-stage pumps and multiple-stage pumps: 500 gpm flow at the fire floor with residual pressure was the goal. This was accomplished at the 25th floor of a building with a pump discharge pressure of 235 psi, which is well within the operational range of a single-stage pump and the operating pressure of the hoses and fittings of most, if not all, fire departments. Most fire departments’ maximum pump discharge pressure in the field should be 250 psi because that’s the maximum operating pressure of hose.
If pumping operations require multiple stages to increase pump pressures, two single-stage pumpers can pump in series to create the same pressures as a two-stage pumper can produce. Using two single-stage pumpers, the first-due pumper hooks up to the building standpipe system to supply water to the building, with the second-due pumper establishing a water supply and pumping to the first-due pumper. Always be mindful of the hose and appliance pressure restrictions when planning for this type of operations.
When specifying a 1,500-gpm or larger fire pump, always consider the plumbing and discharge sizes. Frequently, departments specify a large-capacity pump and plumb it so that it only is capable of delivering capacities of a 1,000-gpm pump. If you specify a large-volume pump, make sure that it’s plumbed to take advantage of the discharge potential. Table 4 shows water flow in gpm through ridge steel pipe at 75 psi. The 1.5-inch and 2.5-inch lines are older but common valve and plumbing sizes. The 2-inch, 3-inch and 4-inch lines are the valve and plumbing sizes that, in my opinion, should be what’s used on today’s higher-volume fire pumps.
The following are suggestions for when specifying the plumbing:
- No 1½-inch valves or piping; 2-inch valves and 2-inch piping should be the smallest that’s specified. Most departments transitioned to 1¾-inch hose, some to 2-inch, long ago; it’s time to do the same with pump discharges.
- Only 2½-inch valves and piping should be used on the pump operator’s panel (NFPA requirement); all other valves should be 3 inches or larger; this is much better for higher flow rates.
- Specify at least one 4-inch discharge with a 4-inch valve and piping for large-diameter-hose supply.
- Piping size should be the same as valve size, never smaller.
- Use the discharge adapter to make the transition to a different size. Example: Discharge piping shall terminate with an aluminum NST adapter 3-inch female swivel by 2½-inch NST male, on a 30 degree downward angle. These are tapered and provide a smoother transition from larger to smaller.
Prepare to break from the past
Many options exist for the choice of pumps. As one prepares a specification, doing the research and exploring all options will allow for the best performance on the fireground. Simply specifying what’s been used in the past might not be the best option for your department.
This article is part of the Apparatus Supplement 2023. The entire supplement can be found here.
Keys to Specifying a Single-Stage vs. a Two-Stage Pump
There are numerous reasons to buy a single-stage pump in place of a two-stage pump:
· The gallons per minute of an extinguishing agent flow is what puts a fire out, not the ppi.
· Single-stage pumps have fewer moving parts to maintain.
· Complexity of two-stage pumps drives the price higher.
· Single-stage pumps are more efficient at higher flows.
Some of the reasons that a department would choose a two-stage pump:
· Only one apparatus is available when called to tall buildings.
· Department uses high-pressure hose reels.
· Two-stage pumps are more efficient at higher pressure but at the expense of available flow.
· Wildland firefighting using 1-inch hose with long lays.
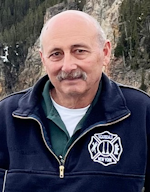
Jeffrey D. Gaskin
Jeffrey D. Gaskin is president of Big Red Trucks Fire Apparatus Consultants. He is a retired captain from the Scarsdale, NY, Fire Department. Throughout his career, Gaskin has been involved in apparatus acquisitions, from needs assessment through specification-writing. He also is a fire apparatus mechanic and holds certifications from Allison Transmission, Detroit Diesel, Hale Pump, Smart Power, Spartan Chassis, Sutphen Fire Apparatus and others. Gaskin is certified by the Emergency Vehicle Technician Certification Commission in six areas: Fire Apparatus Inspection, Maintenance and Testing (F-1); Design and Performance Standards of Fire Apparatus (F-2); Fire Pumps and Accessories (F-3); Aerial Fire Apparatus (F-5); Allison Automatic Transmission (F-6); and Hydraulic Systems (F-8). He can be reached at [email protected].