Shoring Systems for Structural Collapse - Part 2
In Part 2, we’ll focus on a few more shoring systems and attain a greater understanding of this type of operation. The first system we’ll look at is the Window/Door Shore. This shore can be built two different ways. One will allow for access to the structure, while the other will not.
As you will see in Figure 1, the opening in this window/door shore has been blocked by cross bracing. The cross bracing’s main function is not to keep us out, but to provide stability against torsional loads. This system is built in place. If you look at the diagram, you’ll see connections were made by means of triangle gusset plates and 2x4 cleats. Although they look different than the 6”x12” gussets we spoke of in Part 1 of this article, they are performing the same job.
The second method of building this shoring system is referred to as the “ALT Window & Door Shore” (see Figure 2). One huge difference between the two is that the “ALT” shoring system is built remotely then placed in the opening to be shored. When this method is used, the shoring system needs to be built smaller than the size of the opening (approximately 1 ½ inches less in each direction). Wedges are then placed on one side and the bottom (shim where necessary), allowing you to fit the system in place. If shims are needed at the top, try to avoid wedging the bottom of the system. Why? If we are shimming the top of the system, as we drive the shims in place we’re creating an up-and-down force. We would like the force traveling downward (as well as the overall load) to see a flat surface in which to transfer the load. One of the biggest benefits of this system is that it can be built in a safe area away from the collapse zone.
Now let’s venture forward into the family of raker shores. We’ll look at several different raker systems you can build, all utilizing the two most common raker angles of 45 or 60 degrees. Before we begin to tackle this shoring system family, however, you must understand a few things. The raker is the diagonal piece of lumber that runs from the upright to the sole plate. In laymen’s terms, it’s the piece of wood that connects the wall to the ground. The actual purpose of this raker is to transfer the load captured by the upright down to the soul plate and into the ground. It’s the same double-funnel principal that was featured in Part 1 of this article, just turned a bit sideways.
Alright, let’s dig in! The first raker shore we’ll look at is a solid sole raker (see Figure 3), named so because the sole plate of the raker runs on the ground from front to back. Let’s look at the diagram and pick a few things apart. The sole plate of the raker runs into what is called a thrust block. This component terminates the captured load into the ground and is generally made of the same lumber of which the shoring system is made. A minimum of 4x4 lumber is, however, specified. The job of the bottom cleat and top cleat is simple. Between the bottom cleat and the raker is where we’ll drive a set of wedges. The upward force of the wedges will provide a pushing force through the raker to the load we’re capturing. The top cleat terminates the load at the capture point, while the bottom cleat helps to terminate the load into the soul plate and subsequently into the ground.
Both ends of the raker are cut, not only with the raker degree angle, but with what are called return cuts. These cuts provide a flat surface for the wedges to sit against. With that being said, let’s reveal the secret of how we create the angle cuts needed on the raker to sit flush on the upright and soul plate. First we determine a capture point. This is the spot we want the top of the raker to hit. Basically, it’s the starting point for the load transition from the wall to the ground. Let’s say that measurement is eight feet. If we’re building a 45-degree raker, that number gets multiplied by 17, thus giving you the raker length in inches. If you’re building a 60-degree raker, the magic number is 14. If you ever forget which is which, remember that if you multiply 14 by 8 your number will be lower than if you multiplied 17 by 8, thus creating a shorter piece of wood and a tighter angle. Both sides of the 45 degree raker will have 45-degree cuts on them, equaling 90 degrees, while a 60-degree raker will have a top cut of 60 degrees and a bottom cut of...you guessed it 30 degrees. Who said you’d never use geometry once you left high school? The 60-degree raker does save space because of the shorter rake, but its load capacity is less than that of the 45-degree raker.
You’ll also notice a mid-point brace in the diagram. This brace must be added if the raker is 11 feet or longer. Being that rakers are always built in pairs, horizontal bracing will be used to tie the systems together. Horizontal bracing, like mid-point bracing, is made from 2x6 lumber. Our placement points for horizontal bracing are at the top and bottom of the raker. This bracing will fight the effects of lateral loads. We will also add cross bracing to the system, which is nothing more than creating an “X” on top of the horizontal bracing. This also is made from 2x6 lumber and its job is to resist any torsional loads.
A flying raker (see Figure 4) is utilized when neither the soul plate nor the upright can sit flush on the wall or ground due to rubble. It, like any raker shore, can vary in its degree (45 or 60). The public service announcement for today is that “this is only a temporary shore.”
You’ll notice in Figure 4 that the raker is going into a trough. The trough terminates the load and helps to direct it into the ground and thrust block. If you look between the trust block and the trough, you’ll see a pair of wedges. These wedges will provide an upward force, helping to support the intended load. The design load for a flying raker is approximately 1,000 pounds, which is significantly less than that of a solid soul raker. So you may be saying to yourself, “Why use it if it’s weaker and only temporary?” It’s used as a means to create a safe haven to then construct a solid sole raker or a split sole raker (which we’ll discuss later). Once this system is in place, you can clear any debris that is on the ground and then begin to build permanent systems. The last bit of information I’ll throw out there regarding the flying raker is that, unlike other rakers, this system must be connected or “anchored” to both the wall that it’s supporting and to the ground.
The last raker system we’ll look at is the split sole (see Figure 5). This may look like a solid sole raker at first; however, look at the sole plate, there isn’t one. The 2x6 pieces of lumber are acting as the sole plate here. This is done in the event there is minimal debris on the ground that’s preventing you from running a flush sole plate.
When all is said and done, there is a raker shore to fit most situations. Paratech makes a product called Paratech Long Shores that can be used to build raker systems (see Figure 6). The Deployable Raker Kit comes complete with wall and sole plates. You can leave these systems in place, or use them as a quick way to support the structure or create a safe haven in which you can then build a lumber system inside. It is very versatile and very smart.
There are two aspects of shoring operations that you need do adhere to each and every time you’re faced with this type of operation. The first being rescuer safety. Never enter a collapsed or damaged structure until you’ve taken the necessary steps to provide a safe working environment for yourself. Next, your shoring systems must be built to spec 100% of the time. If there’s one thing you should have taken away from this and the last article, it’s the double-funnel principal. This article touched on shoring systems that transferred loads from point “A” to point “B” in directions other than vertically, such as the raker shore. The bottom line is whether you’re building a simple crib stack or a raker shore system, you need to understand the funnel principal and respect it. Next month we’ll look at a few final shoring systems to wrap things up.
Until then, stay safe and stay progressive.
MICHAEL R. DONAHUE is a 14-year veteran of the fire service assigned to Rescue Company 1 in Elizabeth, NJ. Mike is the owner and founder of Progressive Rescue, a company dedicated to further firefighter's in all aspects of the job. He holds the title of rescue specialist with New Jersey's Urban Search and Rescue Team (NJ-TF1) and he is actively teaching at Middlesex Fire academy and the Middlesex County College as their Fire Science Program Coordinator. Mike has been on two Firehouse.com podcasts: The Buzz on Technical Rescue: Rope Rescue Operations and The Buzz on Technical Rescue: Special Operations Roundtable. He has taught as a HOT instructor at Firehouse Expo and is the Specialized Rescue Forum moderator for Firehouse.com. You can reach Michael by e-mail at [email protected].
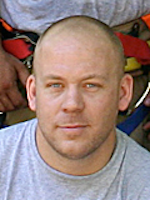
Michael Donahue
Owner and founder of Progressive Rescue, Mike Donahue is a 13-year veteran to the fire service. In those thirteen years Mike has experience as both a volunteer and federal firefighter and has been a career firefighter in the City of Elizabeth for the last 10 years, the last seven of which and currently working out of Rescue Company 1. Mike holds the title of Rescue Specialist with New Jersey's urban search and rescue team (NJ-TF1). You can find Mike actively teaching at Middlesex and Somerset Fire Academies as well as Middlesex County College as an Adjunct Professor and the Fire Science Program coordinator. He is actively involved in writing new course programs for the various organizations he teaches for. Mike has reviewed several text books for publishers such as Delmar and Jones & Bartlett. Mike has also co-written the new rope program for Jones & Bartlett and taught Rope Rescue Made Simple at Firehouse Expo 2010. Mike also is a monthly columnist for Firehouse.com covering the area of technical rescue. His teaching techniques and cutting edge style have gained the respect from many of his peers. Mike's passion, experience and desire to educate emergency service providers prove to be the driving force that has made him so successful. Progressive Rescue prides itself on providing the most cutting edge, diverse instructional programs available. We strive to provide your department with the most comprehensive, dynamic learning experience available at a truly competitive price. You can reach Mike by e-mail at [email protected]