The quality and cleanliness of the air that we breathe shouldn’t have to be a concern, given manufacturing, technological and scientific achievements. However, it’s a very big concern.
Much research and information has been gathered and studied about air quality in the micro-climate of the fire station since the United States passed the Clean Air Act in 1970 and created the Environmental Protection Agency (EPA) to enforce it. Additionally, research into the health of first responders, their protection from carcinogens and cross-contamination, and cancer among them has led the way for emergency response architects and engineers to completely rethink how stations are designed. This rethinking has fundamentally changed decades of accepted practice.
For example, in 2020, the NFPA formed the Technical Committee on Emergency Responders Occupational Health to draft new procedures for firefighters (as well as for police officers and EMS first responders) and to include station design layout among the organization’s work. The NFPA considers these procedures to be so important that they asked the committee to have a draft by year’s end.
Where do we start?
Most new or seriously renovated fire stations can be divided into three zones:
- Hot zone: The apparatus bays and their support areas, such as a work room, bay storage and PPE storage;
- Cold zone: The living/administration areas; and
- Transition zone: A relatively new area concept that’s designed to address the movement between the hot zone and the cold zone.
The concept of transition zones is most in flux regarding what they are, what they should be, how they are designed and how they integrate into standard operating procedures (SOPs).
In the most general terms, cold zones have a greater treated air flow and, therefore, greater air pressure than the hot zones have. This air treatment keeps possible contaminants from emanating into the air through off-gassing from apparatus, equipment, tools or PPE and then flowing into the living side of the station. A cost-effective method to help safeguard this pressurized flow of air is to make sure that doors that are between hot and cold zones are fully weather-stripped and have a threshold, a door sweep and an automatic closer.
When responders move from the cold zone to the hot zone to answer a call, the clean and treated air will move with them. When responders return from a call, they will be traveling against the current of clean air into the cold zone, with a flow of treated air pushing contaminants to be exhausted into the hot zone.
Ventilation and filtration
The National Institute for Occupational Safety and Health defines diesel fumes as a carcinogen. It is vitally important to control or mitigate the negative effects on responders of diesel exhaust that’s generated by apparatus. There are many types of vehicle exhaust (VEX) removal systems, and each has its pros and cons in regard to how exhaust is captured, treated or filtered. The important thing for responder health is for designers and owners to utilize one or more of these systems in the bays and put SOPs into place to make sure that the systems are used. There are no rules or determinations for gasoline fumes that are emitted by tools or vehicles, but there is every reason to believe that research will be conducted and that these fumes—and exposure to them—also will need to be mitigated.
PPE storage is an area that’s in transition for designers. Current thinking has PPE confined to separate rooms, with air movement for drying, exhaust systems, HEPA filters, overhead fans, and other room specialties to control cross-contamination and off-gassing from exposure during events and to allow proper drying and storage. With the advent of “clean cab” scenarios, more and more departments are utilizing gross or specialized decontamination at the event. It's vitally important to responders' health that when they enter the apparatus cab they are clean, or as clean as can be. A new protocol is to bag PPE at the event, send it for proper cleaning and, hopefully, have a second set of clean gear back at the fire station ready for the next event.
The PPE room is being treated more as a transition zone than a hot zone. Our professional design advice is to include all of the systems that are outlined above in case they’re needed.
We shouldn’t overlook ventilation and filtration systems in the hot zone areas. Even with VEX systems, vehicles, hose, equipment and even cleaned PPE still can emit harmful contaminants. Ventilation or 24/7 filtration systems are an advisable option to consider. Advanced systems can incorporate indoor air quality (IAQ) sensors that automatically activate the system when air quality drops below acceptable levels. This approach, which might result in higher initial cost, is a more sustainable approach than “always-on” systems.
Evaluate cold zones separately
On the cold zone side of the station, building and mechanical codes most often will rule the day. Many of these areas are defined as “habitable” space and, therefore, require minimum standards for introduction of fresh air, air changes and exhaust requirements. The mechanical engineer who works with the architect will suggest various types of heating, ventilating and air conditioning (HVAC) systems. Like all systems, each will have its pros, cons, longevity, complexity, controls and, of course, initial budget and life-cycle costs.
Unintended consequences of new code requirements created tighter building envelopes that require careful consideration of ventilation and exhaust of contaminants. The EPA notes, “Much of the building fabric, furnishings and equipment, its people and their activities produce pollution.” The nature of firefighting and emergency response might increase this pollution load.
Various portions of the station should be evaluated separately. For example, if the station design includes individual bunk rooms, consideration should be given to individual controls for each room. Although this might be more expensive than one set of controls for a bank of bunk rooms, the individual comfort and well-being might be worth considering. In a building that has a shelf life of 50–75 years, the HVAC system, its controls, and all it offers toward responder comfort and health should be a decision that’s carefully considered. It’s unfortunate that in a world of budget realities, proper HVAC systems often suffer from value-engineering cuts. It’s the responsibility of qualified station designers to convey the pros, cons, and consequences of these decisions and how they affect the end users.
In some stations that have a training room or community room that might not be used regularly, some simple, cost-effective methods can be utilized to control air movement and minimize energy costs. For example, a carbon monoxide (CO) sensor in the return air duct can keep the system from constantly cycling on.
Many new and existing stations have fitness rooms, too. Whenever possible, treat fitness rooms via dedicated HVAC systems that have heat recovery. At the very least, make sure that there is adequate fresh-air supply and exhaust to control odor and to maintain a healthy, comfortable environment. As with training rooms, the use of CO sensors or other IAQ systems can help to save energy costs when the room isn’t in use.
The kitchen also is an area of great concern. It produces cooking odors. It’s one of the main gathering spaces in the station. It often is a very busy place. Although some states and jurisdictions consider a fire station kitchen a commercial kitchen, many don’t. A commercial designation requires an exhaust hood that has an Ansul suppression system above the stove, fryer or burners. (The suppression system doesn’t apply to this discussion, but it does affect the budget.)
A true kitchen exhaust hood (not recirculating) involves large volumes of makeup and exhaust air. The trick is to be able to supply makeup air as close to or within the hood itself, so the hood’s drawing of heated or conditioned air from the kitchen is minimized. A heat recovery system is advisable in colder climates. Because the kitchen often is open to dining and day rooms, moving large volumes of air can cause discomfort in all three rooms and cost the owner in energy usage.
In addition to the hood, general cooking odors in the kitchen need to be controlled by the building’s HVAC system. If your kitchen has a patio that has a grill, which might be utilized year-round, general heat and air conditioning should be specified to manage the outside air flow from persistent use of the exterior door when using the grill.
Bathrooms, too, should be designed to include adequate ventilation, exhaust, negative air pressure and heat recovery.
What you can do today
Minor, but important, rooms also must be considered. For example, the janitor’s closet is No. 1 on the EPA’s list of indoor contaminant sources. An exhaust fan that runs constantly should be considered to manage odors and contaminants from cleaning products. During the winter in many locales, a heat recovery system in the ductwork can save on the energy cost of exhausting treated, heated air.
Instead of a room that’s dedicated to storing volatiles, such as oil, paint and various fluids, consider a ventilated storage cabinet that’s made specifically to store volatiles. These are rated for this type of storage and can save the cost to supply HVAC and exhaust to an entire room.
Cost, value and HVAC systems always have been hot topics in station design, but with the influx of new research, SOPs and the focus on responder well-being, the quality and movement of air in the station will continue to take on more importance. What can you do today to protect your responders? Get an IAQ test, perform an airflow pattern test, introduce a transition zone(s), change filters and maintain equipment and observe VEX protocols. Then, breathe easier.
About the Authors
Dennis A. Ross, AIA, is the director of Emergency Services Market at H2M architects + engineers. He is National Council of Architectural Registration Board (NCARB)-certified. Ross is a member of the American Institute of Architects, the NFPA and the International Code Council. He is licensed in 14 states and is an honorary member of the Kingston, NY, Fire Department. His expertise in public forums, project management, land use, budgeting and construction and his focus on solutions to difficult problems has enabled Ross to knowledgeably write and speak on a variety of fire station design issues. He co-authored “Chief Fire Officer’s Desk Reference and Fire Station: Architectural Insight to Planning, Design & Construction.” Ross is the only architect to attend the NFPA Technical Committee on Emergency Responders Occupational Health.
David J. Pacheco, AIA, who is an elected fire commissioner, is director of operations, senior architect, vice president and partner at H2M architects + engineers. An adjunct professor at Rensselaer Polytechnic Institute, his broad leadership experience and design expertise has enabled him to knowledgeably write, teach and counsel on all aspects of emergency response architecture. He is NCARB-certified, licensed in 10 U.S. jurisdictions and is a local director of the American Institute of Architects. He has been a juror for national fire station design awards, and Pacheco serves on the ASTM E54 Committee on Homeland Security Applications.
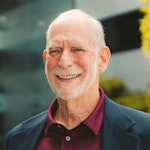
Dennis A. Ross
Dennis Ross, AIA, is a Technical Advisor and past Emergency Services Market Director at H2M architects + engineers. Previously, he was a founder and co-owner of a nationally recognized, award-winning firm exclusively dedicated to the design of emergency response facilities across North America. He has over 40 years of focused experience in construction and development, which allows him to assess projects from multiple points of view.
He is NCARB certified; a member of the American Institute of Architects, National Fire Protection Association (NFPA), and the International Code Council; licensed in 14 states; and an honorary member of the Kingston Fire Department. His expertise in public forums, project management, land use, budgeting, construction and focus on solutions to difficult problems has enabled him to knowledgeably write and speak on a variety of emergency services station design issues. Dennis has authored many articles and presented at even more conferences. In 2001, he received the Business Council of New York State’s and National Federation of Independent Business’ annual award for “New York State Small Business Advocate of the Year.”
Dennis is currently serving on the NFPA Technical Committee on “Emergency Responders Occupational Health,” which is tasked with developing a new Standard for Contamination Control, NFPA 1585. Dennis led the task group for Chapter 5, Emergency Services Organization Facilities. In 2022, he was appointed to the NFPA - Architects, Engineers, Building Officials (AEBO) commitee as an Executive Board Member.
David J. Pacheco
David J. Pacheco, AIA, who is an elected fire commissioner, is director of operations, senior architect, vice president and partner at H2M architects + engineers. An adjunct professor at Rensselaer Polytechnic Institute, his broad leadership experience and design expertise has enabled him to knowledgeably write, teach and counsel on all aspects of emergency response architecture. He is NCARB certified, licensed in 10 United States jurisdictions and is a local director of the American Institute of Architects. He has been a juror for national fire station design awards and serves on the ASTM E54 Committee on Homeland Security Applications.