Here we are as a profession: knee-deep in COVID and all of the proposed trimming and cutbacks of budgets because of the effect that the pandemic is having on the economy. True, the reality of the job might have been morphed a little because of the emphasis on COVID response and mitigation.
However, the line firefighter’s day-to-day need for firefighting PPE hasn’t changed—not with the increased use of plastic materials in household goods, furnishings, etc., the drastically reduced time from ignition to flashover, and a down-turning economy that can lead to higher incidence of accidental and intentional fires.
As a guy who gets on the rig every third day (for the past 32 years), I believe that firefighters want to be protected in a manner that allows them to rescue savable people, to protect savable property, to perform extinguishment of the fire and to go home at the end of the shift in the same condition that they were at the start of their tour. Universally, when I talk to firefighters, the consensus is, first and foremost, they want to be protected from the fire. Yes, they want lighter, more breathable and better fitting gear, but protection always seems to be number one.
One important note to that statement: Many firefighters believe that “as long as it meets NFPA, its good.” The fact is, NFPA standards are minimum standards, and they apply to our entire protective ensemble: helmet, hood, coat, pants, boots and gloves. We always should aspire to go above the minimum to a place that enables firefighters to do their job in a manner that is effective, efficient and safe.
Specification and selection
It always has struck me as kind of silly that the people who wear and use the gear don’t have significant, if not total, involvement in the research, evaluation, and selection of the protective clothing and equipment that they wear. In the upcoming down economy, it might be more important than ever to be able to justify what we—the people who actually squirt water on the fire, drag the hose, climb the ladders, pull the ceiling, and do the search and rescue—select to wear on the job.
I always hear, “Well, 85 percent of our calls are EMS.” OK, but what percentage of our deaths or burns are from the fire? What percentage of our cancer is from a byproduct of the fire? For me, firefighter death and injury in the fire or from the fire isn’t a percentage but a numbers game, and one is too many!
So, we need new (fill in the blank)? Why? Age? Increasing injuries? Better materials? Better design or innovation? All are legitimate needs.
How many do we need? Do we need replacements because of damage or aging? Do we need a second item that’s to be worn while the first receives an advanced cleaning as set out in NFPA 1851: Standard on Selection, Care, and Maintenance of Protective Ensembles for Structural Fire Fighting and Proximity Fire Fighting—or also because science, national standards and, now, some legality dictates that firefighters have clean gear to do their job—and not just bunker gear, but gloves, boots, hood, earflaps and helmet. A second pair of boots? Some departments have recognized the need. Helmets? I guess that we really don’t need two, but we do need to have two sets of soft goods, including earflaps, to ensure that the helmet always is in service while one set of the “guts” of the helmet is being cleaned.
How do we enable this process to engage the firefighters who wear that gear while also proving and providing justification? We don’t want bunker gear specifications that are based solely on “meeting” NFPA or on the opinion of a person who hasn’t been to a fire since George W. Bush was president.
Form a firefighting PPE committee. (It might also be called a research and development committee.) Fill it with personnel of various rank, experience, age, sex, duty assignments and geographic station locations.
Do research. A ton of resources is available online: government agencies, professional organizations, manufacturers, fabric/fiber producers and safety/testing/certification organizations.
Make site visits if you can. Manufacturers and fabric/fiber producers like to have potential customers visit. If you can’t facilitate that because your department is small, consider forming a mutual specification collaborative in which small entities or departments agree on a same specification. Then, have a vendor/manufacturer presentation day, so the attraction for the manufacturers is the presence of numerous departments—even if you don’t have a mutual specification.
Also, go to a trade show or conference if you can. The value of seeing everything in one spot can’t be overstated. The ability to do real-time comparisons and Q&A of the industry people can’t be overstated.
Into the fire
Now that you have your information and education, what are your personnel’s priorities? Thermal protective performance (TPP)? Total heat loss (THL)? Fit? Function? Durability? Establish your numbers.
One thing about numbers: TPP is a fair indication of thermal protection within a couple of points. I remember a senior truck captain testing some new material composite in a gas fired training building. He had a lower TPP composite of 39, and he raved about breathability and comfort. Then we put him as part of a larger evolution group into a gas fired training building that was in the range of 550 degrees F at the thermocouples. About two minutes into the evolution, he came flying out of the side door, patting his arms and pulling off his gear. I asked him how he liked that “comfortable” gear. I can’t print the reply, but now he was in favor of keeping the TPP rating that we were using.
We must subject everything that we wear to a realistic heat and function evolution. We should practice like we play.
On the other hand, THL varies quite a bit from year to year lately. Because we’re told there could be a 20-point (or more) variation plus or minus from the published THL number, it’s at best a guide more than a hard number. Thermal barrier wickability, material weave of thermal barrier and shell and moisture barrier greatly influence “breathability.” Fortunately, materials and weaves advanced significantly over the years. Consider that there are naturally moisture-wicking materials for your thermal barrier and materials that have a moisture-wicking finish. Shell material also has different weaves for durability and protection, along with having a durable water repellent (DWR) applied.
Finishes inside and outside aren’t forever. As a smart friend of mine said, consider the shell like a tablecloth, not a tabletop. It isn’t impervious. You decide what you want to try. Outer shell, moisture barrier, thermal barrier? Boots, gloves, helmets and hoods? There is a lot to pick from, and it can be somewhere between confusing and overwhelming.
Finding a knowledgeable person who has nothing to gain by giving you information or an opinion can be very valuable. The same goes for places that tested or used things that you are considering. Remember the old saying: telephone, telegraph, tell a firefighter. We are our own best sources for information. There are many conscientious, standup, honest people in the firefighting PPE industry, but the distributor representative is trying to sell you; the manufacturer representative is very proud of his/her product over everyone else’s.
The best way to get buy-in and valid recommendations for specifications is to subject products to actual usage, both staged and every day. At first glance, a product might feel great, fit fantastically, look cool, but when it’s subjected to the heat that we feel in a fire or to the on/off/use/wash cycles, a firefighter can get burned. I participated in staged live-fire evolutions where burns were encountered in the same spot on everyone who wore test bunker gear and hoods.
We must put these products through their paces before specifying and purchasing them. We must make sure that the product that is sent is the product that we requested. If you can, request an extra item of everything after the process to see how all of the layers react. Also, insist that the NFPA 1971 Technical Data Package be submitted to you for any item that was requested/submitted for evaluation. Include a clause in your invitation to participate that any item that’s selected by evaluation might be sent for repeat 1971 certification testing at the manufacturer’s expense.
Up for the challenge
There is a lot that goes into selecting any PPE that firefighters use—more than this space allows. That said, educate yourself via a discerning eye and ear but be cautious of everything that you see and hear. Engage the people who use the items in their everyday responses to facilitate evaluations. Evaluate items the way that you use them or simulate it as closely as possible.
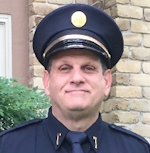