Thermal protective performance (TPP) generally is considered firefighting PPE’s thermal protection rating. Total heat loss (THL) is firefighting PPE’s “breathability.” The two ratings have been the main measuring sticks in the decision-making tree for bunker gear selection for many, many moons.
When discussing priorities in PPE selection, firefighters often comment, “If it meets NFPA, it should protect us just fine.” However, NFPA is a minimum standard. In the case of PPE specification and selection, it should be considered an important starting point. Why just a starting point?
TPP
There are minimum TPP ratings for just about everything that we wear: hoods, helmet ear flaps, coat, pants and gloves. (Boots are rated on radiative protective performance; helmets undergo a 500 degree F oven test.)
TPP is a value of the time to a second-degree blister burn in a flashfire situation. If an item’s TPP is 35, then the time to second-degree burn is 17.5 seconds in a flashfire situation. As TPP increases, THL decreases.
The original calculation only goes to 60 TPP. Alice Stoll and Maria Chianta conducted burn injury research in the late 1950s and early 1960s at the Naval Air Development Center’s Aerospace Medical Research Department. U.S. Navy sailors volunteered to be burned on their forearm. Stoll and Chianta used heat exposures on human (and animal) skin to determine the level of heat energy that would create a second-degree burn. For their work, they defined a second-degree burn as the point at which a blister forms. The result of their work came to be known as the Stoll Curve, which quantifies the level of heat and the duration of time that’s required for a second-degree burn.
Author’s note: Computer-generated scales exceed 60 TPP, but it’s reasonable to ask why those are needed? One’s awareness of the thermal environment would be reduced by hear that has a TPP that’s higher than 60, and, of course, that environment would be unsafe based on prior firefighter injuries and fatalities. The ability to breathe would be reduced greatly, too.
There also is the fact that TPP is measured when a three-layer composite swatch (outer shell, thermal liner and moisture barrier) is exposed to a convective/radiant heat source. Although the base composite of a turnout coat and pants is of three layers, the TPP throughout the coat and pants might be higher in places of reinforcement, such as the patch, pocket, knee pad and reflective materials. (Of course, a decrease in THL applies to those areas of reinforcement.)
TPP and THL values of the three-layer composite won’t match the TPP and THL values for the actual worn garment. Furthermore, because higher TPP reduces one’s ability to sense the heat in the environment, it’s reasonable to ask, should you be in the environment?THL
Every available composite is tested for THL, which consists of thermal resistance (Rct) that’s recorded by testing on a dry plate. This equates to the capability of the composite to transfer heat away from the wearer. Evaporative resistance (Ret) is recorded by testing on a wet plate and indicates the composite’s capability to transfer moisture away from the wearer. The THL value (Qt) is calculated using the thermal resistance and the evaporative resistance.
I believe that a lot of THL results from the bloodborne pathogen resistance (BPR) requirement for PPE and the overheating/increased cardiac stress that came with early barrier products. As firefighters attended more and more medical responses and extrications and confronted more fluids in all-hazards environments, concerns for contamination through responders’ gear came to the forefront.
I experienced the predecessor of the current moisture barriers when I came on the job in 1988. As I remember it, I was given a bunker coat that was a few years old. The barrier was a polyurethane product that didn’t allow anything through but didn’t allow anything to escape either. As it degraded during normal use, the moisture barrier came apart and fell into the bottom of the barrier. (You could feel the bunching of the material in the bottom.) This rendered the rest of the barrier ineffective.
Synthetic rubber also was a purported advancement in breathability that failed miserably. Wearing it reminded me of wrapping a potato in plastic wrap before microwaving it. I suspect that the THL was very low.
As we evolved and as firefighters demanded more breathable/comfortable gear, moisture barriers evolved. THL and the breathability/comfort that’s associated with moisture barriers now are much better, as is the durability.
Again, it’s important to realize and be aware of that inverse relationship of TPP and THL: As THL increases, TPP goes down; as TPP decreases, THL goes up. So, although THL is a starting point, we must be cognizant of the wide range potential of the actual value. Twenty points plus or minus the value is supposedly acceptable.Turnout gear measurements
The minimum TPP for a coat and pants is 35, with no maximum. Although they aren’t measured above 60, layering theoretically can raise the TPP beyond 60.
As noted, a TPP of 35 equates to 17.5 seconds before pain/second-degree burn in a flashfire situation. A TPP of 60 equates to 30 seconds, 120 to 60 seconds and 150 to 75 seconds.
Barrier hoods have a minimum TPP of 20, with a THL of 325. Higher TPPs in hoods reduce the wearer’s ability to sense the outside thermal environment.
Gloves have a TPP but no THL. Gloves should have a barrier in them that allows heat, vapor and, yes, moisture to release from the inside. A legitimate barrier product (not polyurethane) in gloves will keep the TPP but make the glove safer by not holding in the moisture in and still keeping out the moisture.
Boots have a temperature rating but will be more comfortable and safer with a legitimate barrier product.
Protection vs. comfort
TPP and THL are starting numbers in a process that must include actual wear and fire exposure. We as a profession must be aware of that and still recognize the relationship (inverse) between TPP and THL.
For me, the protection factor still is primary, with a realistic view of the comfort and breathability that’s needed to function as intended on the fireground or anywhere else that operations dictate.
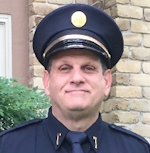