Richmond’s fire department was all volunteer from 1830 to 1872. The first organized fire company in 1830 began with 15 members signing up. The first fire pump, on wheels and pulled by a rope, had already been purchased in 1829. From 1872 to the present, the fire department has been fully career. By the 1960s, Richmond had six fire stations in service. Five of those stations have been converted to other uses, including Station 1, which is a fire station-themed restaurant owned by one of the department’s current members. Only Station 4 is still at the same location at 801 South L Street.
Today, the Richmond Fire Department, under the innovative and dedicated leadership of Chief Jerry Purcell, operates from five fire stations with 82 full-time staff positions—78 of which are currently filled. Firefighters staff five engines, two trucks, one rescue, a hazmat unit, and three ALS medics, along with two BLS on a day-to-day basis. Richmond Fire Department covers a first-due area of 55.95 square miles and protects a population of 66,000 people. Miscellaneous equipment includes a battalion chief vehicle, two grass/brush trucks, a water rescue unit, a hazmat/special ops unit and an EMS utility task vehicle. The department also operates an unmanned aerial system (drone). Richmond responded to 10,483 calls for service in 2018. Of those, 8,925 were rescue/EMS calls, which makes up 85 percent of the total responses. Call volume has more than doubled in the last 10 years.
Hazmat team overview
Organized in 2004, an initial “batch” of technicians were trained for hazmat responses via funding through EMA/LEPC from federal funding in the aftermath of 9/11. Initially, team training was completed monthly but fell off as members lost interest. In 2014, the department, with the help of the International Association of Fire Fighters (IAFF), trained a new “batch” of technicians and training once again resumed a monthly schedule. The team has stayed steady at between 15–20 members since 2014. Hazmat training is now moving toward training all members of the department on a regular basis and team trainings once per quarter. The Richmond Hazmat Team is a local team, however, they provide mutual aid to all counties surrounding Wayne County, and in the event of a large-scale incident, would respond anywhere requested.At a minimum, hazmat team members must show annual proficiencies donning/doffing PPE, atmospheric monitoring and decontamination. Over the last couple years, the training focus has been on the “most likely to be involved” substances locally (anhydrous ammonia, chlorine, hydrocarbon fuels). All firefighters are certified to operations level. Richmond’s Hazmat Team is not a dedicated team, meaning the number of hazmat personnel on duty at any given time varies on each shift. There are 24 personnel assigned each day per shift, five to eight are technicians, with the balance being ops-certified. When the team is dispatched, on-shift personnel are moved as necessary on apparatus and a call is sent to off-duty personnel via cell phone. There are 18 technician-level personnel available citywide, but given that all firefighters are trained to the operations level, every firefighter plays a role on the activation of the team. If needed, mutual aid is available from Madison County Hazmat Team, Indiana Department of Homeland Security and Indiana National Guard, 53rd Civil Support Team. Annual hazmat responses vary widely—some years there are one or two team call outs, other years there are none. Engine companies typically handle fuel spills and gas odors on shift without requiring a team call out.
Over the last several years, Richmond has developed a plan and constructed a new training facility, which is an ongoing project. The training center will also be used by other departments in the county and the Richmond Hazmat Team. I attended a hazmat training program at the facility this past April involving the handling of liquid propane leaks.Water injection for LPG leaks
Provided here is an overview of the process of stopping liquid leaks involving both fixed and transported liquid petroleum gas (LPG) containers. This information is intended as an informational presentation and is in no way meant to provide training on the use of the water injection or flaring systems or other associated procedures. It is up to your department to determine the need for this process and associated equipment. Once a need is determined, those personnel who will utilize the water injection and flaring systems along with other procedures dealing with LPG must be thoroughly trained in utilizing the procedures and equipment by a knowledgeable instructor. Like any other tool in the hazmat toolbox, it will not be necessary or required in all instances. Personnel must know when use is proper and when use is not needed or too dangerous to use. LPG is a flammable gas and appropriate precautions need to be taken, such as controlling ignition sources and monitoring for the lower explosive limit (LEL) like any other flammable gas or vapor.
LPG exists in a container in both a liquid and vapor state. Every LPG container has a vapor space above a liquefied gas that is kept as a liquid by the pressure in the tank. This vapor/liquid relationship is the same regardless of the orientation of the container following an incident. Liquid LPG leaking from the tank creates 270 times more vapor released than a straight vapor leak from the same tank. LPG vapors are heavier than air and when released from a container will sink to the ground and pool in low areas such as basements, sewers and low-lying terrain.If the tank fails, and all of the liquid is released from the tank at once, the LPG immediately converts to a vapor. In this circumstance, water injection is not a tool to use. Water injection is only utilized when valves or piping on a container have failed and liquid is leaking from the container. Working in a vapor cloud caused by an LPG leak might seem very dangerous, however, there is not enough oxygen for ignition to occur because the mixture of oxygen and LPG is too rich.
Safety is of primary concern and monitoring still needs to take place and ignition sources controlled when deciding to approach the LPG tank. Propane, as it is commonly called, is actually a mixture of several LPGs, including the volatile hydrocarbons propene, propane, butene and butane. A typical commercial mixture may also contain ethane and ethylene, as well as a volatile mercaptan, as an odorant added as a safety precaution. Water injection leak-stopping procedures will work on any of these mixtures as well as the pure compounds.
Water injection only works on liquid LPG leaks and does not work on vapor leaks. Specialized tools are required to perform the process and training in the use of these tools and the concept of water injection is required. This process is utilized only after it is determined there is no other way to control a liquid leak and the incident location will not allow for letting the LPG release on its own.Digging into the details
Water injection involves the forcing of water into a container with a pressure greater than that of the LPG tank’s static pressure. This is most effectively accomplished with an engine company supplying the water. These gases are liquefied for commercial purposes. More of a gas can be transported and used in a liquefied form than as a compressed gas alone. LPGs are stored and shipped at ambient temperatures, meaning whatever the temperature is around the container, so will be the temperature of the liquid inside. Water that is injected into a container should be cool so that it doesn’t heat the LPG liquid, causing more vapor to be produced and compounding the situation.
Pressure within the container keeps the gas as a liquid. If the liquid is released from the container, all the liquid will very quickly be converted to a gas. One gallon of propane will expand to more than 270 gallons of highly flammable gas. Generally, hydrocarbon compounds do not mix with water and they are lighter than water, so liquid hydrocarbon compounds will float on the surface of water. Water weighs approximately 8 pounds per gallon and LPG approximately 4 pounds per gallon. When water is injected into a container, it goes to the bottom of the tank and LPG floats on the top of the water. As long as water is continually injected into the container, water will leak from the tank rather than LPG, stopping the vapor production of the leak. It is the physical characteristics of water and liquefied petroleum gases that allow for stopping liquid leaks in containers by injecting water.Using proper tools, flaring of containers is conducted to safely remove vapor from the container reducing the internal pressure and lessening the chances of a total tank failure, sometimes referred to as a BLEVE (boiling liquid expanding vapor explosion). Water is injected until the container is 80 percent of its capacity with water and the pressure is continually controlled and monitored.
Specialized tools are required to perform water injection and flaring operations. Most departments do not carry these tools. Water injection will provide your department with additional hazardous materials tools that cannot be accomplished with other tactics. I was impressed with the procedures and effectiveness of water injection and the safety of the process including the flaring of containers. After looking at the LPG exposures in your community, it might be time to add this new tool to your hazardous materials toolbox. This tool should not be used without personnel being thoroughly trained by knowledgeable instructors to use the water injection process.
Richmond Hazmat Team—At a Glance
Historical blast
On April 6, 1968, at 1:47 p.m. two tremendous explosions rocked the downtown area of Richmond killing 41 citizens, including seven children, and injuring more than 127. Five families suffered multiple losses of life, including one family that lost a mother and two children.
Ground zero on that fateful day was the Marting Arms Sporting Goods Store, located at the corner of 6th and Main Street in the heart of downtown. Guns, ammunition, black powder and primers were among the goods sold from the business. A firing range was also located in the basement of the store. Witnesses described the first explosion as “muffled.” It caused a severe vibration of the walls of Marting Arms and lifted the building slightly off its foundation. Investigation into the cause of the explosions determined that a gas leak occurred in the building and the leaking gas was ignited by a gunshot in the firing range. The second explosion, the more powerful of the two, was touched off by the first, igniting gunpowder and primers stored in the basement.
One person who was in the building at the time of the explosions survived. Jack Bales was standing next to his childhood friend Greg Oler at the rear counter of the store. He saw his friend fall through the floor and never saw him again. Oler died at the scene.
“There were about one or two seconds between blasts,” Bales said. “When the first one hit, I moved to cover my head and I saw Greg go down. Then the second one hit. When I was in the hospital, I think the second day, my parents came and told me that they found Greg’s body in the rubble in the basement.”
As a result of the two explosions, three buildings were completely destroyed, many others were damaged by the explosion and resulting fires. Window glass was broken for more than three blocks and the blast was heard over a mile away. Nothing but a hole in the ground remained where the sporting goods store had been. Adjoining buildings were ripped apart and fires raged through the business district. Twenty buildings had to be condemned, 125 buildings were damaged, and the estimated dollar loss was $15 million (more than $102 million in today’s dollars).
Mutual aid responded from surrounding areas of Indiana as well as Ohio. This aid included civil defense personnel, fire departments from as far away as Eaton and Dayton, OH, along with state and local police agencies. Fire departments responded from throughout Wayne County, including Boston, Centerville, Cambridge City, Greens Fork, Fountain City, Hagerstown, Dublin, Milton, Webster and Williamsburg. Other departments responded from neighboring counties and from Ohio to man now empty fire stations in Richmond, to handle any additional calls and provide assistance at the scene. These departments included, West Alexandria, New Madison, Hollansburg, Trotwood and Dayton, OH; and Liberty, Brookville, Everton, Lynn, New Castle, Lewisville and Anderson, IN.
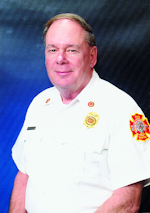
Robert Burke
Robert Burke, who is a hazardous materials and fire protection consultant and who served as a Firehouse contributing editor, is a Certified Fire Protection Specialist (CFSP), Fire Inspector II, Fire Inspector III, Fire Investigator and Hazardous Materials Specialist. He has served on state and county hazmat teams. Burke is the author of the textbooks "Hazardous Materials Chemistry for Emergency Responders," "Counter-Terrorism for Emergency Responders," "Fire Protection: Systems and Response," "Hazmat Teams Across America" and "Hazmatology: The Science of Hazardous Materials."