Essential facilities have pursued “green” building strategies and certifications for decades. New thinking about how to support the mission of critical facilities through the lens of autonomous operations/resiliency, total cost of ownership, and responder health/wellness has expanded the vision for what an ideal essential facility might look like.
The Living Building Challenge (LBC), which generally is considered the world’s most stringent green building standard, might at first glance seem to be far removed from the difficult, daily realities and demands that an essential facility is expected to support. A deeper look, however, suggests that the underlying principles of the LBC contain a practicality and toughness that support the design and development of outstanding, next-generation, 21st century critical facilities.
What is the Living Building Challenge?
The LBC includes seven topic areas: place, water, energy, health and happiness, materials, equity and beauty.
Projects may certify entirely or partially under the LBC. There also are targeted zero-energy and zero-carbon certifications. The certification requirements can be found at living-future.org/lbc-3_1/certification.Without doing a deep dive into the LBC certification requirements (and, perhaps, holding your eco-preconceptions at bay), it’s helpful to consider some of the underlying philosophy that’s behind the LBC.
Net positive: Much green and environmental thinking focuses on how to reduce our impact on the environment, as if humanity is fundamentally at odds with the planet. The LBC turns this on its head and pursues a net positive approach through designing and building in a way that leaves the world a better place than we found it and gives more than it takes. As a result, LBC buildings are deeply efficient and collect the natural assets that are available at each unique site.
Use natural, simple systems first: The best LBC buildings often hearken back to the pre-electric, pre-fossil-fuel era. They take advantage of natural heat, daylight, cold and wind to serve the building before they use mechanized systems. This means that many LBC buildings are reasonably habitable without any powered inputs.
What does good look like?: This is a common question in the LBC ecosystem. Rather than starting with prescriptive code compliance or detailed certification requirements, agencies and their designers are given aggressive goals, such as net-positive energy and water performance, and are asked to use creativity and community-learning to find solutions.
Connect with nature: The highest-performance buildings connect people to nature rather than isolate them from it. The LBC recognizes that people perform best when they are connected to nature through views, fresh air, natural materials and an array of other experiential strategies.
What is included?
Currently, an ideal next-generation essential facility fully provides the core programmatic functions of emergency services while it supports and protects resources for sustainable operations. It provides seamless service communications as well as the rehabilitation and tools that are necessary to adequately prepare for the next event.
We suggest three additional elements for an expanded vision of a next-generation essential facility: resilient and autonomous operability; restorative environment; and lowest long-term total cost of ownership.
Resilient and autonomous operability speaks to the matter that, if any building should be operable during an emergency, it should be an essential facility, at least partially (think post-severe earthquake, firestorm, hurricane or any circumstance in which power and public services are unavailable for a long period of time).
Related to energy and off-grid operability, the LBC requires net-positive energy performance. For energy, this means that the building actually produces more power than it uses over the course of one year. It also requires a small amount of battery backup storage. However, this typically assumes a building that is tied to the electric grid.
A thoughtful and knowledgeable design team can combine LBC net-positive energy requirements and project resiliency goals to build a facility that can operate autonomously from the grid, at least for core functions. To achieve net-positive energy performance, buildings need to radically reduce energy use. This often is done by substantially improving the exterior of the building with better insulation and air sealing. If combined with well-positioned and specified windows and heating base loads, a facility can operate through passive solar and internal heat gains without mechanical heating. An essential facility can continue to operate even when the electrical and natural gas grid is down and when diesel fuel for the generator is unavailable. Designed properly, solar panels can recharge the batteries during the daytime, which allows the facility 24/7 operations.
Similar to energy, the LBC requires net-positive water performance. In part, this means that the facility collects all of the water that it needs through wells or rainwater, with hydraulic balance with the aquifer where available. In practice, this means that LBC projects include a large cistern as well as potable-grade filters. In the face of water-supply disruption (a possible outcome of a major earthquake or extreme drought), such systems could second as an emergency drinking water source for the broader community.
When it comes to a restorative environment for the health and wellness of first responders, essential facilities should be a refuge for firefighters, medics and police officers. First responders must contend with heat stress, toxic exposure, pathogens, and emotional and physical trauma. The stations that serve them should help with their rehabilitation and recovery to maximize mission readiness.
The LBC materials and health requirements substantially align with these goals. The LBC includes what is called the Red List, which prohibits materials that have chemicals that have known health concerns from being used in buildings. The Red List includes vinyl and fire retardants, which create highly toxic smoke when they are burned, aligning the LBC twofold with first responders’ health. Many Red List-free materials are found on the Declare database at declare.living-future.org.
In conjunction with this is the premise of the Central Valley Fire District in Belgrade, MT, where the decontamination and cleaning process was decoupled entirely in a separate building outside of the core station. A video of their process can be found at glatfelters.wistia.com/medias/0zecb4jd9g.
An important and reasonable question about the LBC is, “How much does it cost and how is it paid for?” Looking at this question holistically, including costs that relate to long-term durability/replacement cycle and operating costs, will result in lower net costs to the station operator. Considering that an operating budget often is more difficult to obtain than capital budget, this view of cost is even more compelling.
The LBC/next-generation building does cost more to build, however, these upfront costs are more than recovered through operating savings and the increased durability of the facility. Operating savings can be well-understood and predicted, even to the degree that some energy companies will guarantee energy savings. Designed right, the LBC/next-generation building should be more durable. A better-sealed and insulated exterior requires much more care during construction, resulting in less heat loss and gain, better weatherproofing, and less potential for water intrusion, corrosion and rot. Simpler and higher quality mechanical systems, such as hydronic distribution, have fewer moving parts and have less room for failure.
With an intense focus on community and emergency-responder safety, pushing the boundary of facility design in an integrated and holistic way better informs the design of next-generation facilities. This helps us all to become better ready for the future.
About the Authors
Brian Harris, AIA, is the principal/president of TCA Architecture + Planning Inc., having led in the design of more than 150 fire facilities in 10 states. He won numerous design awards and authored many articles on fire facility planning and design. Harris is a frequent speaker at national fire facility conferences, and his career includes significant firsts in the fire facility design industry. He was the architect of record for the first LEED-certified fire station in the country, the first LEED-certified training facility in the country and the first LEED Platinum net zero energy fire station.
Brad Liljequist, LFA, is the zero energy program manager for McKinstry, where he leads the company’s zero energy efforts nationally and managed the zero energy elements for Catalyst, which is a McKinstry developed project that will be the world’s largest Zero Energy building when the project receives its certification. Previously, Liljequist directed both the energy and community programs for the International Living Future Institute and developed the first certified multifamily zero energy project to be located in the United States; that project is called zHome. He also developed the Issaquah, WA, Fire Station 72, which is the winner of the national ASHRAE Technology award.
Examples in Public Safety
Mosier Center, Mosier, OR
This project was designed by Minarik Architecture with support from fire station design specialists TCA Architecture + Planning (TCA) and McKinstry. It combines a city hall, a fire station and a community center. It is targeting LBC Zero Energy (ZE) Certification. It will take advantage of the strong westerly breezes for daytime natural ventilation and of the low nighttime temperatures to cool the building, which will be retained by a well-sealed and insulated envelope. The solar array, which is adequate to offset annual energy use, will provide electricity to the station during the day and send any surplus to the electric grid.
Cincinnati District 3 Station
This 39,500-square-foot police station, which was designed by Emersion Design and CMTA, achieved LBC ZE Certification via a remarkable 20 percent net-positive surplus of 62,000 kwh/year that’s provided to the electric grid. The building uses ground-source heat pumps to substantially reduce its heating and cooling load. The 20-year operating expense savings for the $16 million facility (delivered via design/build under its existing budget) was $2.2 million. The operating energy use intensity, excluding solar production, was 26.7 kbtu/sq ft/year, which represents a 66 percent reduction from the 79.4 kbtu/sq ft/year baseline.
City of Bellevue Fire Station 10, Bellevue, WA
This 25,000-square-foot project is being designed by the City of Bellevue and Bohlin Cywinski Jackson and supported by fire station specialist design partner TCA. The project is tackling the integration of five key project goals: protected, prepared and healthy community; community connection; civic presence; firefighter health and wellness; and sustainable design. The team is evaluating the integration of LBC core metrics with a baseline Leadership in Energy and Environmental Design (LEED) certification and Salmon-Safe Certification. The highly integrated design process is testing performance metrics against natural site amenities, resiliency, firefighter wellness and broader civic goals, which will connect, rather than isolate, the facility and its inhabitants.
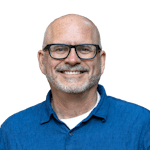
Brian Harris
Brian Harris AIA, LEED AP, NCARB, is principal/president of TCA Architecture + Planning and is a co-founder of the Station Design Conference 1-on-One sessions. He has been instrumental in the design of more than 325 fire facilities in 18 states, won more than 65 design awards and authored many forward-thinking fire-facility planning and design articles. Harris speaks frequently at national fire facility conferences and is the director of design education for the Washington Fire Chiefs fire facility section. He designed the first LEED-certified fire station and the first LEED training facility in the United States and worked on the first two Net Zero-Energy fire stations in the country.