Station Design: A Detached Decontamination Building Examined
For a moment, assume that the phrase fire station isn’t in your vocabulary, but you must tell someone about how you are trying to protect the life and safety of a community by housing people and equipment in a centralized location. Because these people will be put in harm’s way, they must be well-trained, equipment must be maintained, and both must be available at a moment’s notice. Durable and low-maintenance structures are needed to support this activity. Simple, right?
Now layer in what is known relative to the occupational hazards of first responders. When designed, the facility should anticipate sleep-deprivation concerns, behavioral-health and gender considerations and radio-frequency-radiation risks as well as public access with concern regarding, in general, an increasingly hostile public. Furthermore, the individuals and equipment will be exposed to carcinogens and pathogens that will be brought back to the facility. The stress on these workers is high, so a low-stress environment also is important.
By the way, you have a limited budget to achieve this goal.
While breaking down these specific requirements, Central Valley Fire District (CVFD), which is located in Belgrade, MT, came up with a unique approach.
Many considerations
When funds are limited, community and departmental values play an extremely important role in the design process. When CVFD considered its project, people who were involved looked at how their prioritized values would influence the station.
Should the station be designed as a permanent 50–80-plus-year facility that has built-in resiliency to accommodate change? Is it better to design a lightweight, disposable facility that would be rebuildable in 20 years and relocated based on dynamic community growth patterns? Would it make sense to take a modular approach to allow for expansion and adaptability? How would the answers to these questions mesh with the public’s perception of a fire station?
Also: Should contaminants knowingly be brought into the facility then attempted to be isolated, captured and removed? Or are aspects of operations ready to be rethought—grounded in evidence-based design—to manage the change that’s necessary to wash away set habits?A developing concept
CVFD knew that it needed a long-lasting, resilient facility that’s located in a stable response area, and firefighter health and wellness, coupled with good stewardship of public funds, would be paramount. That said, how could the department move beyond what currently was being considered in most facilities relative to “Hot Zones”? Was there a new way by which stations could be designed?
From the start of the project, Chief Ron Lindroth was a strong opponent of bringing source contaminants into the station. Based on recent studies and decades of personal experience, he knew that if key decontamination and cleaning functions occurred in the station, it just would be a matter of time before these contaminants would find pathways into the clean living and administrative areas. This “just don’t do it” mindset triggered the overall concept of decoupling disinfecting and cleaning procedures from the main station by providing an outbuilding for these functions. It was believed that by developing a detached decontamination building, in which PPE, SCBA and apparatus is cleaned, contaminant isolation could be optimized. As an added benefit, firefighters would be nudged into a higher level of awareness that these tasks carry daily exposure risk. (Risk-awareness often is forgotten when all functions are combined into a single facility.) By making this activity special and independent from the core station, it stands out in everyone’s mind.
It was determined that the facility also could function as a vehicle wash bay. Unlike most stations, where apparatus washing is forced inside because of stormwater pollution issues, the detached decontamination building could further prevent hazardous contaminants from being washed onto the apparatus bay floor, where equipment checks and restocking of apparatus occur on a daily basis. (It’s difficult to imagine that pancake breakfasts and station tours are allowed without similar mitigation measures that are employed at the CVFD facility.)
Questioning everything
Initially, it was thought, “How can we afford a separate facility?” Early in the design process, the skeptics were right, at least at first. Building two like facilities would cost more. However, did they really need to be the same? Must the detached decontamination building be designed to an essential-facility standard? Did it need to be faced in brick? Did it need to have the sophisticated lighting and mechanical systems that the core facility would have? The clear answer was no. This could be a very simple, understated, utilitarian outbuilding that doesn’t have a public face, has a lesser life span and could be constructed at half of the cost per square foot than the main station.
Along with decontamination and cleaning features, such as extractors, wash alcoves, pressure washers and drying racks, the design of the detached building includes changing areas and steam showers. With an understanding that toxins can build up in a firefighter’s body over time, the showers were incorporated as part of the post-call rehabilitation process.
Is the detached decontamination facility a cure-all to eliminating the “rainbow” of potential cross-contamination, where the deep red zone falls outside of the station? It never is that simple, just like the notion of red, yellow and green zones is usefully wrong if taken literally, as exemplified by the transmittance of COVID-19 within stations. We still have degrees of contamination—or spectrums of color—throughout a facility, but we are exploring how to provide a better and safer environment.
Because CVFD’s facility tackles the problem differently, it is hoped that it furthers the dialog and brings additional attention to the hazards that are faced and potential ways by which departments can address these concerns through design.
Could these decontamination and cleaning functions be equally separated within a single facility? Perhaps, but at what cost? How could an approach such as this even be considered in an urban setting or for a department that has dozens of stations? Would locating a detached building at the training facility for all to use including other agencies be an option?
Questions have been asked about how this facility has performed during the pandemic. Although it does little to prevent direct human-to-human transmission beyond provisions for hand and boot washing and good ventilation in both structures, the detached decontamination building has allowed for better isolation of used PPE, for decontamination and cleaning, and for sterilant fogging of apparatus and equipment outside of the operational bays.
With health and wellness in mind at the onset of the pandemic, UVC lighting also was installed to further mitigate potential pathogens and contaminants within the core facility.
Although there is a tremendous amount of industry thought on how to reduce station contaminants, the question needs to be asked, “When is clean, clean enough?” Although established personal exposure limits for hundreds of substances are identified by Occupational Safety and Health Administration and National Institute for Occupational Safety and Health, agreed-upon best practices that are relative to contaminant zoning only go so far. If boots are tested for contaminants, what are we testing for? What is an acceptable and unacceptable particulate level on boots after cleaning? Intuitively, one might say just take them off, but change is difficult with limited hard data. We know that things always can be cleaner and safer. However, without a defensible metric that establishes minimum standards, a department unknowingly might be going down a break-the-bank rabbit hole in the best interest of health and wellness.
So where is the point of diminishing returns? Is prevention less expensive than the cost of a future claim? How can further studies be encouraged to guide departments in a scientific way? Testing, education, training and change management will be critical to ensure that future facilities are future-ready to ward off both acute and chronic shocks over their life span.
Think outside of the box of tradition. The time to act is now.
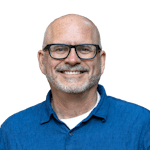
Brian Harris
Brian Harris AIA, LEED AP, NCARB, is principal/president of TCA Architecture + Planning and is a co-founder of the Station Design Conference 1-on-One sessions. He has been instrumental in the design of more than 325 fire facilities in 18 states, won more than 65 design awards and authored many forward-thinking fire-facility planning and design articles. Harris speaks frequently at national fire facility conferences and is the director of design education for the Washington Fire Chiefs fire facility section. He designed the first LEED-certified fire station and the first LEED training facility in the United States and worked on the first two Net Zero-Energy fire stations in the country.
Ron Lindroth
Ron Lindroth has more than 40 years of experience in the fire service, during which he served in all ranks of emergency services across a wide breadth of rural, urban and combination departments. He currently is the chief of the Central Valley Fire District (CVFD). Lindroth began his career in 1976 as a wildland firefighter with the U.S. Forest Service. In 1986, he began a 24-year tenure at the Poudre Fire Authority in Fort Collins, CO. Prior to taking his position at CVFD, Lindroth served as the fire chief of Steamboat Springs, CO, Fire Rescue. He has advanced degrees in fire science and fire service leadership.