Station Design: The “Clean Bay” Concept: A Breath of Fresh Air in Firehouse Design
Not all threats to firefighter safety are visible to the naked eye. What’s more, they can pose risks long after the final flames were extinguished.
Every piece of apparatus and equipment that was in reasonable proximity to a fire event likely is contaminated with toxins and carcinogens, so it should be systematically cleaned upon return to the station. Regardless of whether cleaning is done with a garden hose or a pressure washer, a significant portion of the harmful particles become aerosolized and contaminate the floors, walls and air that are within the apparatus bays. In other words, rather than removing these hazards, personnel essentially shift them from the surfaces of the apparatus to the surfaces of the bays.
What’s apparent but not adequately addressed in most stations is the imperative to effectively clean apparatus bays themselves to properly expunge harmful materials. Similar to a “clean cab,” bays that adhere to the “clean bay” concept are designed with hard, durable, nonporous surfaces, fewer difficult-to-reach nooks and crannies, and less clutter.
Floors
The bulk of the contaminants that are removed from apparatus with a hose or pressure washer washes onto the floor, where a great deal of residue remains, suspended in water, and runs into drains. To ensure an appropriate slope (approximately 2 percent) and reduce ponding, we recommend that trench drains run the full length of the building in every apparatus bay. Both sealed concrete and epoxy floors are durable and cleanable, whereas rubber and quarry tile systems can trap contaminants in the joints.
Walls
Bay walls should be constructed using materials that can withstand frequent scrubbing and rinsing. All walls that are shorter than eight feet tall are subject to being hit by water that splashes off of contaminated apparatus, so this zone needs more frequent cleaning with a direct hose stream regardless of conformity with the remainder of the clean bay principles.
Epoxy-painted concrete block, epoxy-painted precast concrete and ceramic tile work well for bay walls.
We recommend that ducts, power and data conduit, and plumbing be concealed behind walls to eliminate difficult-to-clean nooks and crannies that are created when these items are surface-mounted.
Rubber wall base isn’t recommended, because its adhesive eventually fails when repeatedly exposed to water. Even epoxy flooring tends to crack when it’s wrapped up the wall because of the differential movement in a space that sees wide temperature swings. Tile base can work, but we recommend simply using a sealant joint between the floor and walls.
We frequently see laundry appliances, SCBA compressors, cleaning supplies and even sterile EMS supplies stored along the walls of the bays. Departments should have a goal of storing nothing along bay walls, both to avoid contamination of those items and to make cleaning easier. We are strong proponents of providing dedicated rooms for those functions, which retains ease-of-access via doors that open onto the bay floor.
Even spaces that are expected to be dirty, such as a maintenance workbench, are most appropriately located behind a door that can be closed during various decontamination activities.
Main doors into the apparatus bays should be made of hollow metal, because wood doors can’t handle repeated washing. We recommend armor panels to reduce the incidence of small scratches that will start rusting.
Hinges should be nonferrous. We recommend setting hollow metal frames flush with the face of the bay wall to eliminate another corner to clean around.
Bay doors should be resilient and able to withstand regular cleaning. Overhead sectional doors and their tracks and wind braces include many horizontal surfaces and crevasses and even inhibit mopping where the tracks meet the floor. High-speed roll up doors also have tracks that can be challenging to clean, although the equipment at the door header can be concealed with an easy-to-clean stainless steel box. Four-fold doors have fewer places for carcinogens to hide and are more conducive to cleaning the floors.
Ceilings/roofs
We toured countless firehouse vehicle bays that contain porous materials on the ceilings, including acoustical ceiling panels, unpainted/unsealed wood elements, and fabric banners and flags. All of these porous materials should be avoided, because they absorb carcinogens and moisture, which are released over time.
Most fire stations that we tour use open-web steel joists/trusses to support the roof. These provide countless ledges for contaminants to rest on, out of reach of easy cleaning. An ideal roof structure is precast concrete T’s, because there are no horizontal surfaces, and it can be pressure-washed easily. Conduits, piping and ductwork can be grouped together in the space that’s between two T’s and enclosed with an epoxy-painted gypsum ceiling. Yes, this type of ceiling can be dropped below roof trusses—a tempting value-engineering target—but it’s important to maintain enough height to dilute airborne contaminants in a large air volume. Another approach to roof support is long-span steel deck, which can reduce the number of joists greatly. Some of these products have channels that can be used to conceal conduits and pipes.
Other considerations
Exhaust systems play a key role in the clean bay concept. Direct-tailpipe connections capture diesel contaminants but don’t capture carcinogens that float in the air of the bays. Filtration systems, on the other hand, clear any airborne particulates regardless of source (albeit after firefighters have had an opportunity to breathe them in). This makes filtration systems an important tool in the clean bay toolbox. If your station is in a temperate climate, a purge-exhaust system that has an unducted makeup air system can replace the entire apparatus bay air volume with outdoor air within 30 minutes.
Selection of your mechanical systems affects the cleanability of your bays, too. Although inexpensive, an overhead radiant tube system creates a long horizontal surface—which doesn’t get hot enough to destroy carcinogens—and is challenging to clean. Simple unit heaters typically don’t include filtration, so contamination spreads throughout the interiors of those units. A radiant floor system, however, is fully concealed and creates nothing additional to clean.
Natural light should be abundant in the bays, so dirty areas are identified easily. Equipment for washing bays should be separate from cleaning equipment for the living quarters. Bay washing equipment stored along bay walls is the one exception to the store-nothing-along-bay-walls mindset. Convenience of this equipment is important, and because it’s within easy reach, it’s straightforward to keep clean.
The National Fire Protection Association found that wet soap scrubbing is an effective way to combat fireground contaminants. We recommend periodic scrubbing of bay walls with soapy water and a brush, followed by a gentle rinse with a garden hose. (Pressure-washing is less labor-intensive but re-aerosolizes the contaminants.)
Floors should be cleaned after every event. Hard-trowelled and polished concrete floors can meet slip-resistance recommendations and are easy to mop. If epoxy flooring with texture is used to increase traction, you should plan a location to store a powered floor scrubber.
Twice-yearly pressure-washing of the upper bay walls and any exposed equipment, ducts, pipes and conduits is a reasonable baseline, although the need should be evaluated based on call volume and the specifics of the department.
Economically effective
Using these clean bay concept strategies, departments can take the next step toward reducing job-related cancers that occur in first responders. It’s one of many ways that the intentional design of firehouses can promote the physical and mental well- being of their occupants, often with little or no additional cost.
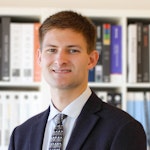
Brandon Adams
Brandon Adams is a project architect at BKV Group who focuses on government projects in various counties throughout Virginia. Some of Adams’ work included aiding in the design process of a new, LEED Silver-certified fire station in Fairfax County and working on the master planning of a new courthouse complex in Warrenton. Prior to working at BKV Group, he worked on multifamily residences in the Tidewater region of Virginia. Adams is a recent graduate of the University of Virginia, where he earned a Master of Architecture and a Bachelor of Science in Architecture.
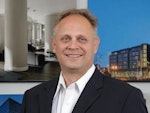
Mark Manetti
Mark Manetti, AIA, LEED AP, is partner in charge and senior project manager with BKV Group. Manetti has years of experience planning, designing and documenting fire station projects. His clients include some of the nation’s most forward-thinking fire departments, which keeps him at the forefront of innovation in fire station design. Manetti is an advocate for resiliency in government projects and has in-depth knowledge of applying sustainable standards to fire station projects.
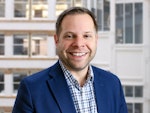
Craig Carter
Craig Carter, AIA, LEED AP BD+C, is lead facility planner and firematic expert with BKV Group, which is a full-service design firm that has offices around the country. Carter has 21 years of experience in architectural design, documentation and construction administration with a focus on public-safety projects. He has worked on more than 80 fire station projects and won several design awards that celebrate the functionality and beauty of the projects. Carter combines a deep knowledge of the history of public-sector design with an up-to-date knowledge of the latest national trends.