The honor and pride of the fire service always has been about the calls that we run and the camaraderie of our crews, as it should be, but little attention is brought to the logistics of a fire department.
The business of sustaining a department can be a daunting task, given limited means of generating revenue and relying on a tax base. Add the rising cost of apparatus, bunker gear and all of the supplies that are needed for crews to be successful, and one can ask, “How can the budget keep up?”
In 2016, Cobb County, GA, Fire and Emergency Services purchased a vacant, 110,000-sq.-ft. building that was a glass manufacturer. The original vision for this facility was to increase bay space for the apparatus shop and to create warehouse space and for future plans of an in-house laundry center. Today, the Cobb Fire Annex is home to apparatus maintenance, support services, facility maintenance, an EMS warehouse, small-engine repair, an air laboratory and an indoor physical agility training center. With the extra square footage, the department entered into lease agreements with Ten-8 Fire & Safety and Gear Wash by Fire-Dex, truly making the Cobb Fire Annex the business hub of the department.
The Annex
The office and work areas were designed to accommodate workflow and productivity. As you enter the office space, you get a business feel that captures the fire department culture. There is a large collaboration room that’s designed to facilitate better communication among staff, to host preconstruction meetings for new apparatus and stations, and to provide an area for vendors to drop off products for testing and evaluation. The design and look of this portion of the building create a high level of pride and ownership, with more of a business mindset.
Staff have bought in to the idea of reducing costs and how to run the department’s business in a more effective and efficient manner. One of many inefficiencies was the multiple locations of logistics shops. The department started consolidating logistics with the original purchase of the building, but there still were areas that could be grouped at the Annex.
Apparatus maintenance
The largest portion of the floor space of the Annex is home to the apparatus maintenance shop. It’s divided between the department’s apparatus maintenance team and Ten-8 Fire & Safety.
The apparatus maintenance team side is made up of six service bays where four vehicle maintenance technicians repair and maintain a fleet of more than 100 vehicles. Along with the techs, a shop supervisor and a parts manager each focus their efforts on preventative maintenance and minor repairs.
With a large portion of the department’s fleet made up of Pierce apparatus, the lease of the Ten-8 Fire & Safety side (7,000 sq. ft.) allows the department to partner with its local dealer, providing on-site warranty repairs and major repairs. This fleet comprises 42 engines, 13 ladder trucks, 3 technical rescue team squads, 5 specialty units, 15 rescues, 7 battalion chief vehicles as well as utility trucks and support vehicles.
This partnership has yielded more than just revenue for the department and faster turnaround time on repairs. With a discounted flat hourly rate for repairs, no travel time charges and a discount on parts, the department averages a cost savings of more than $120,000 per year.
Furthermore, the information-sharing and factory support emerged as a major advantage, facilitating hosting a wide range of in-house training for the department’s emergency vehicle technician (EVT) program and factory training. The EVT program gives the department’s employees the chance to further their education, provides career advancement, and helps the department to meet strategic and accreditation goals. By Ten-8 Fire & Safety hosting factory training, the department has increased the staff’s exposure to Pierce-specific training and has saved the training budget $25,000 annually.
PPE laundering and repair
With the success of the apparatus lease agreement, the department looked at other business opportunities.
A goal of the department was to have an in-house laundry service to help to become compliant with NFPA 1851: Standard on Selection, Care, and Maintenance of Protective Ensembles for Structural Fire Fighting and Proximity Fire Fighting. After evaluating the cost, it was decided to advertise another lease agreement for a laundry service to lease space inside of the Annex. The agreement eventually landed with Gear Wash by Fire-Dex. This has been another success, because it allows the department to use the revenue from the lease to pay for the cost of deep cleanings and all bunker gear repairs.
Support services
The revenue from both lease agreements has helped with the increasing costs of running a fire department, but it isn’t as impactful on reducing inefficiencies. With the remaining square footage of the Annex, the department brought all of logistics under one roof. Most of this space is occupied by support services and facility maintenance.
Support services is tasked with capital purchases, accountable equipment, bunker gear, small-engine repair, the air lab operations, product research and delivery of goods.
The captain of support services oversees the group, which is made up of a lieutenant, two engineer positions, two firefighters, a fiscal technician, a warehouse technician and part-time staff. This group’s daily functions consist of apparatus design and purchasing and product replacement, repair and purchasing. They also manage bunker gear purchases and maintenance, and repair of that gear as well as of hose and SCBA.
The small-engine repair shop performs the preventive maintenance and repair for the department’s saws and hydraulic tools.
The air lab is made up of 720 sq. ft. of conditioned space and warehouse space where hose repair, SCBA repair and SCBA testing are conducted. Air lab staff also perform annual facepiece fitting and testing.
Facility maintenance
The facility maintenance group manages repairs and renovations for 33 department locations (29 stations, the training center, the public fire safety village and fire headquarters). The group consists of a manager and seven building trades technicians, four of whom are mobile and three who are assigned to specific locations. The group also coordinates with a variety of subcontractors and vendors for repairs that are outside of their scope of work. This work—overhead doors, HVAC, vent hoods, pest control and roof maintenance—is done under maintenance contracts and price agreements. The group processes more than 40,000 maintenance requests per year.
PAT facility
In 2019, physical agility testing (PAT) was moved to the Annex, to meet the goal of a climate-controlled fitness test.
The previous testing area was on the training grounds, where the department had to dedicate the training building for two to three months to run all 700 firefighters through the test. (This is the same test for pre-hires and return-to-work.) The building also had to be cleaned and set up and had five staff members to proctor the annual test.
Now, the test can be conducted year-round, indoors and with one proctor, without interrupting the fire training grounds and saving the department overtime by not needing the extra staff.
EMS Warehouse
The department’s EMS warehouse was moved to the Annex in 2021 with the use of CARES Act funds to construct the warehouse, which has an internal pharmacy. The EMS warehouse was built separately to add a higher level of security/limit access. This is largely because of the security requirement from the Drug Enforcement Administration for the pharmacy, which requires narcotics to be behind two separate locked doors.
Change of workflow
All of the moves that are described above changed how the department delivers products to the stations and conducts daily business. Now, field personnel come to the Annex for their PAT; to get their SCBA facepiece tested, sized and tested for N95 mask; and for EMS recertification. Personnel also can drop off gear for their annual NFPA 1851 deep cleaning and inspection.
EMS deliveries are being consolidated with support services deliveries, and other support functions are benefitting from the consolidation of space and equipment, which ultimately reduces the cost of doing business by eliminating unnecessary deliveries.
More opportunities
The department continues to look for other opportunities. The department recently selected Front Line Mobile Health as the NFPA Annual Physical provider and is working through the details of the possibility of another lease agreement. This is the latest example of the department finding another way to be more efficient and creating a business mindset within logistics. These practices will allow the Annex to continue to be the business hub for years to come and will sustain the department’s response goals through logistics.
At least $250,000 saved annually
Previous leadership saw an opportunity and purchased a 50-year-old facility that was, at the time, oversized and quite ugly. Some believed that the department never would use all of the space, but since then, this facility has been transformed into a state-of-the-art fire logistics center. It’s difficult to measure in total how much the department has saved by joining all of logistics under one roof, but doing so has limited scheduling conflicts for field personnel, improved workflow and greatly improved staff morale. At minimum, it’s safe to say that more than $250,000 has been saved annually.
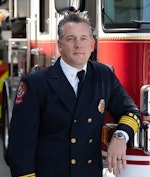
Adam Storey
Adam Storey is a division chief with Cobb County, GA, Fire and Emergency Services, where he has served since 1997. He also is the executive officer for the director of public safety. As the chief of logistics, Storey is responsible for capital improvements, facility maintenance, apparatus maintenance and support services. he holds a bachelor’s degree in human resource management and an associate degree in business administration and is a graduate of the University of Georgia’s Carl Vinson Institute of Government’s Management Development Program.