Today’s apparatus specifications seem to go on forever. Many documents are more than 100 pages in length, calling out every dashboard gauge, seat and interior trim color and referencing the NFPA 1901 standard throughout. While the old expression “The Devil is in the Details” certainly has merit, it is not surprising to work with apparatus committee members who admit that they have not read the entire vehicle specification at any point in the design process. Further, we can probably all recall attending some apparatus committee meetings where the focus seemed to be on the color of warning light lenses and graphics design rather than on the chassis and body components that could enhance safety and improve vehicle performance.
Builder details
How we arrived here is largely due to changes in the manufacturing and build process that are common in the industry. Did you ever notice that no two apparatus manufacturers’ specifications follow the same format when describing the vehicle components? Some may believe that this is done to discourage other folks from bidding; however, the real reason is that many apparatus builders use their specifications to develop the bill of material and engineering required to successfully build the vehicle with all of the options requested by the department.
Virtually all apparatus builders use software programs to develop their specifications, which start out as base models with options for virtually every component on the vehicle. If your department has not acquired a new unit within the past three or four years, chances are that many of the specific model numbers and components have been upgraded and changed as technology moved forward. This is particularly noticeable with diesel engine and electronic components where federally mandated standards have influenced all types of automotive designs.
Boiling it down
At some point in the specification-development process, the Word document can be distilled down to a component or stripper list that ranges from 10 to 15 pages and calls out each of the major components in single-line fashion. This component list may then be used by some manufacturers for review at the pre-construction conference and final inspection as a means to go over the entire vehicle. While this practice can save some time, this does not mean that the formal specification should be forgotten; rather, this is the document from which the terms of the contract were stipulated, and it should be utilized throughout the build process for reference and to confirm that all areas of concern have been addressed.
Starting with the boilerplate portion of the specifications, these first pages of the document are most important as they determine the “rules of the road”—rules that should be developed with specific verbiage to favor the legal interests of the agency purchasing the vehicle. Many areas should be addressed here:
- Requirements for bidders
- Engineering information
- Pre-construction conference
- Final inspection
- Certification testing
- Terms of acceptance and payment
- Delivery training
- Warranty requirements
Each of these areas is critical for the fire department to discuss and determine the process by which bids will be evaluated for compliance as well as which specific design criteria or overall dimensions are important. All of these areas need to be addressed up front, before the committee debates the merits of single- vs. two-stage fire pumps or the size of the water tank, etc.
For example, most manufacturers have developed base models of pumpers along with several body lengths and compartment dimensions. In order to have some degree of uniformity, whatever the standard compartment depth or door height might be, these numbers are called out in the specifications—at times to two decimal points. While this works for that builder, not all manufactures may offer a compartment size to meet this specific requirement. For this reason, the specification should include a listing of the critical dimensions, including wheelbase, overall length, height, width, length of the cab, bumper extension, rear step, body length and hosebed height from the ground. Each of these areas should list a minimum and maximum permissible dimension to permit a prospective bidder to offer a vehicle design to meet these needs.
In the cab
Cab design and components—such as frontal and side airbags, seating design and seatbelt hardware—have been developed to enhance the safety environment for the driver, officer and crew. Cab seating layout in the past was somewhat limited by the length of the cab and where the apparatus manufacturer determined the location of the forward-facing seats. With some departments operating with four to six personnel, it does not make sense to specify the longest cab available, which can add 12 to 18 inches of wheelbase, unless there are some specific requirements for interior EMS and tool storage.
Several apparatus manufacturers have designed their cab with multiple positions for forward-facing seats that do not limit you to having two seats bolted to a seat riser within six inches of one another. Placement of seatbelt retractors and belt assemblies has been designed to permit personnel to more easily buckle the seatbelt with full PPE without having to adjust their position. Given the continued number of fire/rescue personnel who are injured each year on apparatus, “Seated and Belted” should be the mantra of every fire department.
Remember the goal
When starting out on any new vehicle, it is important that the chief officers and stakeholders in the process determine the mission of the vehicle. This may seem simplistic, but there are many departments that, due to the inability to determine the principle characteristics of the apparatus, end up with a unit that was too large, overweight and underutilized.
Factors like fire station bay space, first-due response area roadways, terrain, bridges; gross vehicle weight limitations; tools and equipment carried all have a dramatic impact on how the vehicle should be designed and, more importantly, how it will perform over the next 10 to 15 years. The specification process should be a programmed and detailed one for everyone involved. Operational efficiency, safety and maintenance provisions should all be addressed as the apparatus committee works through the process.
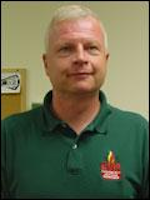
Tom Shand
TOM SHAND, who is a Firehouse contributing editor, is a 36-year veteran of the fire service. He works with Michael Wilbur at Emergency Vehicle Response, consulting on a variety of fire apparatus and fire department master-planning issues. Shand is a member of the Firehouse Hall of Fame.