Natural gas leaks that result in explosions are a real and present danger in the fire service. Most municipal jurisdictions dispatch several units for an alarm of “smell of natural gas” inside a structure—and for good reason. The consequences of a leak finding an ignition source in an enclosed structure can be catastrophic.
Gas leak basics
Gas leak calls can be small or large, accidental or intentional. Most commonly the call is due to an “odor” complaint. Natural gas has an odorant added called mercaptan. This odorant is added at 1 part per billion, which is more than enough to provide that sulfur smell we are all too familiar with.
Types of emergency responses to natural gas include:
- Appliance leak or absent pilot light
- Leaks in commercial structures or institutions
- Construction breaks (homeowners or contractors working or digging)
- Accidents involving regulating stations
- Natural disaster or weather-related incident
- Over-pressurization or routine release during service
- Criminal intent (gas used for illegal activity or being stolen)
- Pipeline problem
- Issues at production facility
- Chemical-assist suicide
First-in considerations
Whether or not your agency assigns multiple units or a single unit response to the first alarm, the actions of the first-in will greatly influence the resolution to the emergency. Following are several first-in considerations:
- Scene safety
- Ensuring a water supply
- Approaching from upwind
- Proper size-up
- Rescue considerations
- Ignition sources identified and secured
- Gas detection monitoring
- Ordering of additional resources
- Evacuation considerations
Incidents of note
Every year there are several significant natural gas related incidents. On Jan. 15, 1998, a shoe store in Phoenix, AZ, near Third Street and Indian School Road was leveled by an explosion. Battalion Chief Phil Yeager told The Daily Courier that a construction crew severed a line while drilling under a sidewalk, and gas filled the vacant building and ignited. According to news reports, three workers were injured, one critically, when a line they were attempting to repair found an ignition source and sent 100-foot-tall flames in to the sky during rush hour. The blast could be felt at Phoenix Fire Station 9 around the block from the incident.
On Sept. 9, 2010, a natural gas line ruptured in San Bruno, CA, causing an explosion that leveled a neighborhood and killed eight people. The resulting eight-alarm fire response was challenged by breaches in the water supply, multiple casualties, and craters in the street that blocked access. It is reported that during the days prior to the explosion, residents complained of the smell of natural gas.
Recent PFD gas incident
On a clear day in September 2015, a single engine from the Phoenix Fire Department (PFD) was dispatched to a report of a “pole” fire. Engine 58, led by Captain Phil Johnson, responded to a one-story drive-through liquor store located off the main road and accessed by an asphalt driveway. The engine company arrived on scene to find people pointing at flames coming out of the ground at the base of a sign at the entrance to the property. The sign was held up by two metal poles with concrete bases set in the asphalt. The reporting party from the business also said they smelled gas inside the store. Colorful flames burned at the base of one of the sign poles while dust blew from cracks in the asphalt near both sides of the sign giving the indication of gas leak. The Engine 58 crew established a water supply, pulled a protection line and focused on ensuring that all persons were out of the structure and immediate area.
Although not on duty the day of the explosion in 1998, the 19-year veteran captain recognized that this was no ordinary gas leak and was not going to take any chances. Captain Johnson, also trained as a hazmat captain, called for a hazmat response, which also included a safety officer (known as C957) and a battalion chief.
The engine crew shut off the gas to the structure and set up a safe perimeter. During the process of making sure all occupants were accounted for, the crew noticed that a flag on top of one of the sign poles was making contact with overhead electrical lines. They also noticed what appeared to be a fresh utility line trench extending from one sign pole to the corner of the business. The reporting party also stated that they had intermittent power outages at the business over the last few days and had turned the power off to the sign. Dispatch was contacted for both the local gas and electricity providers to report to the scene.
While the first-in crew waited for hazmat and the local utility representatives, the fire at the base of the sign pole continued to burn while bubbles appeared to off-gas at the cracks in the ground. The gas providers have a term known as “push,” which is used to describe gas escaping from the ground that usually presents as dust and dirt being blown into the air at the surface.
The Engine 58 crew stood by with a hoseline ready while colorful flames persisted at one sign pole and the “push” appeared at the base of both sign poles. A gas leak with explosion hazard meant pulling a hoseline, but an energized electrical fire meant to stay clear until the electrical problem was isolated or controlled. The one confirmed ignition source was burning and was either ignited by an electrical spark or was an electrical fire. This was not going to be a routine call.
Getting to work
Captain Johnson initiated the Incident Command System and briefed the arriving resources. Phoenix HazMat Squad 44 was assigned hazard sector to investigate the report of a gas leak at the structure while the local power provider de-energized the power lines. The expectation of the hazard sector was to clear the building, the only enclosed space, and confirm that there was no explosion hazard. The utility company representative was assigned to remove the power problem.
The electric utility representative opened the switches and reported that the whole circuit was dead. Almost instantly the fire at the base of the pole went out, although a visible sign of dust “pushing” from the base of the other pole remained. A theory developed that perhaps the electricity grounded down the sign pole and caused a breach of the gas line. During the same time the hazmat team members surveyed the structure with their monitoring equipment and found no presence of LEL but did get some hits for carbon monoxide (CO).
The gas utility crew started by researching maps of their lines and surmised that perhaps there was an old abandoned line that cracked or popped due to the grounding electricity. The gas utility used their natural gas detectors and had readings as high as 40 percent around the areas at the base of the poles. The "push" continued even after the electricity was disconnected. With safety measures in place, the gas company began a pattern of pogoing where they drill holes in to the earth and measure the "push" to find the location of the leak. During the pogoing operation, the gas company workers were still receiving high readings for gas on their detection devices at the inspection holes.
They continued obtaining readings for gas to ensure that there was not a leak, which meant extending the operation to completely isolate any potential line. The gas company located their main in the middle of the street and did two remote digs to squeeze and clamp the line in two locations, completely isolating the area. Even after this operation, they continued to get readings up to 40 percent on their gas detectors.
The lower explosive limit (LEL) is the lower end of the concentration by volume a particular gas will ignite. The upper explosive limit is the other end of the explosive range, meaning that when outside of this range, the gas is “too rich” to ignite. Every flammable gas has a range in which it can ignite. Natural gas is mostly made up of methane, which has an explosive range of 5–15 percent of its volume in air. The gas-detection devices used by natural gas providers are calibrated for methane, as this is what they are more commonly working with. The gas-detection devices carried by hazmat teams and other first responder teams are often calibrated to methane or a “pentane equivalent mixture” to cover a large range at the lower limit. It is important to recognize that LEL readings will only be accurate to what the meter is calibrated to detect, so if there is a reading, it could actually be higher. The difference in readings of LEL based on the calibration gas is referred to as “correction factor.”
Solving the mystery
Even after the gas company isolated its main in the street, the "push" continued. At one point, a gas representative walked near one of the posts and reported feeling the sensation of “electrical arcs” to his body. The power that both the fire department and the gas representatives thought had been secured was still energized. Further, the flag that made contact with the overhead line was still touching the line that had been reported to be de-energized.
The power company was contacted again, and their dispatch reported that they were busy rerouting power throughout the area. After some urging, the power representative returned to the scene and was asked to remove the flag from the pole as was previously requested but told the power disconnect would take care of the problem. Upon removal of the flag, the visible "push" from the base of the poles stopped almost immediately. The power that everyone was sure had been removed was still energized. The overhead lines were 7,200 volts phase to ground.
Utility workers recovered baseball-sized pieces of glass in the ground at the base of the sign poles. Sand will turn to glass at approximately 3,200 degrees F. The evidence suggests that the high-voltage power caused the burning of the ground, but it is unknown if the amount of volts was continuous throughout the incident. The high temperature likely caused melting and off-gassing of the asphalt, resulting in release of hydrocarbons.
Lessons learned
The electrical hazard was recognized and addressed early and was part of the safety concern for the incident. It is always important to have a representative remain on the scene from the electric company when possible. Electricity will find the path of least resistance when seeking a ground. In this case, the flag touching the overhead line created the path for the electricity to ground. It is unknown why the overhead electrical line remained energized after opening the switches and why the protection relay had not tripped the electrical substation circuit breaker in the first place.
Induction can be a serious danger. This is electricity in even a non-energized line due to static electricity, wind or proximity to other high-tension lines. After interviews with electricity experts, it is unlikely that nearby power or induction caused the line to be energized. To operate safely, always consider the line to be “hot” until absolutely proven otherwise.
The Engine crew that was on scene for the entire incident witnessed the flames go out when the power was initially turned off, and there were several reasons to believe there was a gas line rupture. First contact with persons on scene reported a smell of gas as well as the visible and detected “push” from around the sign poles. With 20/20 hindsight of the incident, it was likely the electricity burning the asphalt that caused the release of hydrocarbons giving clues that mimicked a natural gas leak. The CO levels received by the hazard sector inside the structure may have been products of combustion transmitted through the nearby conduit or open window of the structure.
As with any incident, it is easy to pick apart and criticize after the fact and after everything has played out. In this case, this was clearly an unusual incident that had several very qualified people scratching their heads during and after the conclusion.
The safe resolution to this unusual call was due to the good decisions early on by an experienced crew. These factors involved:
- Early recognition of hazards
- Request for additional resources
- Evacuation and rescue plan
- Setting up incident command and dividing into sectors
- Ongoing risk analysis and safety briefings
Having read this incident, the following are things to consider for your first-due:
- Know your utility providers. Some may be part of your city government; others may be contractors. Nationwide there are variations in terminology and protocols.
- Do your first-in crews carry gas-detection monitors? If so, are they trained in proper use and limitations? If not, do they know when to appropriately call for hazmat?
- Consider a plan for keeping a utility rep on scene. Many providers have hours of the day with a skeleton crew and are unable to commit to a scene due to staffing or other emergencies, such as during a disaster. Meet with your utility and work on a preplan. Request the utility rep to verify that the electrical lines are de-energized after opening switches and remove foreign objects from the electrical lines.
In sum
Trust your instinct and training. In this incident, the Phoenix crew knew first-hand the dangers of a gas explosion and recognized the electrical component. Although the energy was not completely isolated when they expected, they remained aware that it was a possibility while trying to figure out the gas leak.
Sidebar: Gas Emergency Info
Natural gas properties and terms
Flammable range: 5–15 percent by volume; lighter than air but can accumulate in a structure
Push: Used to describe escaping gas
Pogoing: Perforating ground with half-inch round bar and probe with fiberglass pole to find leak
Common hazmat gas monitor reads
LEL: lower explosive limit
CO: Carbon Monoxide
H2S: Hydrogen Sulfide
O2: Oxygen
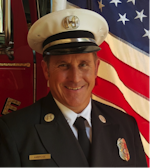
Phil Ambrose
Phil Ambrose is a captain/paramedic/hazmat specialist for the Glendale, CA, Fire Department as well as the founder of HazSim. Ambrose has more than 20 years experience in hazmat and a bachelor’s degree mechanical engineering from Loyola Marymount University.