Note: This article is part of the Firehouse 2024 Station Design Supplement. To read the entire supplement, click here.
Over the past few years, the fire service learned much about the dangers of contaminants that travel from the fireground back to the station. Research and experience have taught us that, along with gross decontamination at the fireground, a well-designed decon space in the station is essential to firefighter health and safety. Scientists and product development researchers continue to identify new and better ways to clean PPE and to better protect the health of firefighters.
Our May 2023 article, “Turnout Gear & Equipment Cleaning,” described some of the nuts and bolts of planning a decon laundry. What you’ll find below provides an update on the science of decon and describes the challenges and some of the solutions that can be put into practice.
Contaminants
Discussions about contaminants can sound like alphabet soup, with strings of letters that stand for chemical compounds that generally are used in manufacturing heat- and water-resistant coatings and flame retardants. What’s important to remember is this:
- These chemical contaminants are persistent. They remain on PPE after cleaning and can lead to cross-contamination at the station and can be brought home. Researchers are looking to improve the cleaning process, so more of these chemicals are removed. The NFPA is examining cleaning procedures through its PPE Cleaning Validation study, exploring the question “How clean is clean?” and asking departments to document their cleaning procedures.
- When in contact with the human body, whether through inhalation, ingestion or skin absorption, these chemicals can lead to cancer and other illnesses. Effective decon is needed to address the high incidence of cancer in the fire service.
- As medical calls increase, so does exposure to microbial contamination. This includes viral and bacterial infections, including resistant strains, such as MRSA. Pests, such as bed bugs and lice, also can be brought back to the station and are difficult to eliminate. In addition to the emphasis on chemical clean-up, sanitizing procedures also must be part of the decon laundry regimen.
What we’re learning from research
We know we have a problem. In response, colleges, governments and industry are working hard to determine the most effective methods to clean PPE, equipment and personnel. Many studies, small and large, are contributing to a growing body of knowledge that will improve safety. Topics range from studying the pathways that are taken by contaminants, to improvements in PPE materials, to changes in cleaning methods. One example of research examining contaminant pathways is a deeper look at skin absorption.
If it’s on you, it’s in you
The skin is an understudied and often underestimated route of exposure to a multitude of hazardous toxicants that firefighters routinely encounter. Understanding the quantity and rate of dermal absorption of specific toxicants is extremely important to help to inform risk-mitigation strategies.
Dr. Caroline Smith, who is the director of the Thermal and Microvascular Physiology Laboratory at Appalachian State University, is taking a novel approach to investigating dermal absorption in firefighters by placing very small catheters between the layers of their skin. This technique allows sampling of the fluid that sits between the cells, to assess what penetrated the skin. Current research conducted by Smith’s team, in collaboration with Indiana University Bloomington, shows dermal contaminant absorption at the neck and forearm following training burns with acquired structures. The quantity of contaminants that were sampled under the skin, including flame retardants, such as polybrominated diphenyl ethers (PBDEs) and polycyclic aromatic hydrocarbons (PAHs), is much greater following structural training burns.
Based on these findings, we know that skin decon should be completed as soon as feasible at the fireground, targeting high-exposure areas, such as the neck and wrists, and follow-up procedures should take place at the firehouse upon return.
Other skin areas also are susceptible to contaminants that either pass through the PPE or remain on and in PPE and station wear after laundering.
Clean isn’t always clean enough
Recent studies showed that as much as 50 percent of PAHs and a significant portion of semi-volatile organic compounds (SVOCs) and heavy metals can remain in PPE after it is laundered. Other studies concluded that the surfactants/soaps and techniques that are used during the laundering process might not be effective at removing organophosphorus flame retardants (OPFRs), PAHs and PBDEs at the concentrations that are used. Some studies indicate that cross-contamination in laundering can increase the contamination levels in some items and that contaminants might remain in the washing machine and contaminate subsequent loads of wash.
It was found that clean station wear that was laundered with contaminated PPE became cross-
contaminated and could contribute to increased concentrations of SVOCs in fire station dust. A conclusion is that personal clothing shouldn’t be washed in the PPE washer extractor but in a separate machine that’s reserved for this purpose. Another study found that normal laundering didn’t reduce the rate of PAHs that off-gassed from the moisture barrier or outer shell.
To address the limitations of wet wash, fire departments and independent service providers must follow the recommended procedures for an advance cleaning per NFPA 1851: Standard on Selection, Care, and Maintenance of Protective Ensembles for Structural Fire Fighting and Proximity Fire Fighting. Machine settings are important to achieve this. Field inspections that were conducted by Tonya Herbert, who is the owner of Florida PPE Services and Thin Red Line Decon, found machines where the cycle for outer shells was only about 30 minutes, whereas the NFPA-recommended cycle is about 50 minutes. Some machines had a wash time of four minutes and two rinses of two minutes each, rather than the NFPA recommendation of a wash program of 12–15 minutes and three rinse cycles of five minutes each.
There are variations of procedures that are used by some gear-cleaning facilities and departments, including the use of a soak tank as part of prewash procedures. This involves soaking outer shells for approximately an hour in a mixture of water and detergent. Herbert found that with presoaking, approximately 95 percent of SVOCs can be removed as well as nearly 75 percent of heavy metals.
Advances in cleaning methods
In contrast with the approximately 50 percent of PAHs that can remain in PPE fabric after conventional laundering, PPE washing machines that use liquid carbon dioxide (LCO2) as the solvent remove nearly 100 percent of PAHs and as much as 75 percent of heavy metals. Where conventional water-cleaning techniques stop at the surface of a waterproof layer, the smaller molecules of LCO2 penetrate between the fibers of waterproof layers to remove toxic organics, metals and other NFPA-specified substances. These washing machines operate at low rpms, which prolongs the lifespan of PPE.
The LCO2 machines don’t use the agitation and spin processes of the washing machines that use water. Studies that were conducted at the Wilson College of Textiles at NC State University found that LCO2 had minimal effect on the mechanical strength of the outer shell material or the repellency. Unfortunately, the machines generally cost more than $700,000 and, thus, are out of reach of most departments. However, some private cleaning providers offer this service, and regionalized, municipal shared cleaning facilities that use LCO2 are in the planning stages. Depending on department size, needs and financial situation, LCO2 could be used for routine cleaning or could be a great option for twice-yearly advanced cleaning with conventional washing in between.
With an oxidizing power 3,000 times more effective than bleach, ozone (O3) is the second most powerful oxidant in existence. Ozone gas is used in mold remediation, air sanitizing, equipment sterilization, water purification and commercial laundering. Adding ozone to the washer cycle was shown to remove 99 percent or more germs, including viruses and bacteria. A number of ozone generator systems are designed for installation in fire stations. Ambient air, in conjunction with the use of high-voltage plates, is broken down, so that oxygen molecules are reformed into ozone.
SCBA, boots & gloves
A variety of machines emerged on the market that rapidly and thoroughly clean SCBA equipment, boots and gloves. Some are washing machines. Some are submersion tanks that use ultrasonic technology for the cleaning process.
Ultrasonic cleaners: Ultrasonic cavitation bubbles gently clean dirt and grime in the tiniest crevices, using only a water-based solution.
High-temperature vapor: Cres Guard makes a device that allows PPE to be exposed to 185 degree Fahrenheit air at 65 percent relative humidity. The company’s data indicate a nearly 100 percent elimination of bacteria after a 15-minute cycle. The manufacturer will complete testing this year to demonstrate that the system doesn’t harm the PPE.
Hot Zone showers: Preliminary exposure reduction at the fire scene is essential, but it isn’t full decon of the responder’s body. Stations need showers in the Hot Zone, with the goal of removing the maximum possible quantity of contaminants from the skin. The current consensus is that the water should be cool to temperate, not hot, and that the shower should occur as soon as possible after arriving back at the station.
Shower stalls in the Hot Zone should be single-occupant and designed for complete privacy.
Undergarments that are worn on scene are considered contaminated. Each firefighter should have a locker that’s near to the showers, where a clean set of street clothes can be stored. At the completion of the shower, the contaminated undergarments should be washed in the residential-style washer at a high temperature and dried in a residential style dryer. These machines should be used only for this purpose.
Protecting the station
Keep in mind that contamination can travel. It’s critical to thoroughly clean all PPE as soon as possible after returning to the station and to store it in an enclosed, well-ventilated space that’s isolated from living spaces. At least one report about contamination control indicates that fire station dust is a potential source for inhalation and even ingestion exposure, particularly when hands aren’t washed prior to eating. Another study found that a suspected carcinogenic flame retardant was discovered in vacuum cleaner dust at concentrations that were among the highest of any that were reported previously in residential and occupational settings in the world. The report from the study advised that regular cleaning of fire stations (e.g., via more cleanable surfaces, including floor coverings, particularly in turnout gear locker rooms and apparatus bays) might be effective in reducing contamination.
What you can do
Continue to follow advances in research. Right now, our understanding of risks and solutions still is growing. Based on what we know now, keep the following front and center as you plan:
- Clean all PPE, equipment and apparatus soon after returning to station.
- Clearly layout and label Hot/Warm/Cold zones.
- Make sure that the decon area is easy to get to and inviting to use; isolated and well ventilated; well lit; designed with adequate work and storage space; and equipped with smooth, easy-to-clean surfaces and that all of its pipes and conduits are buried in the walls. This includes the ceiling.
- Follow NFPA 1851 instructions on temperature, amount of gear per wash load and flush cycles.
- Add a presoak stage to the firehouse’s step-by-step laundering process for turnout gear.
- Wash personal items separately.
Last, but very important: Understand the dynamics of change and your role in helping personnel to understand and embrace new procedures. The more that you understand about research advances and recommended practices, the better that you will be at facilitating the department’s acceptance of change. If the majority of users, both veterans and rookies, are on board, implementation can run smoothly.
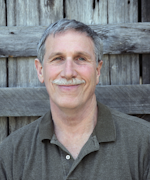
Robert Mitchell
Robert Mitchell is senior architect at Mitchell Associates Architects, which is teamed with Five Bugles Design as part of Wendel, which is a full-scope architecture and engineering firm. Mitchell has 30 years of experience designing fire stations and has been involved directly in more than 190 fire station and emergency services facilities projects, affecting more than 330 fire stations. More than 40 of his stations were recognized in national fire service magazines; seven won national gold prizes. Mitchell recently developed the “basis of design” for future fire stations for Philadelphia that addressed new stations and renovations, dealing directly with firefighter safety and health and decontamination. He is the author of the chapter on fire station renovation and additions for the "Fire Station Design Handbook," which was published by the International Association of Fire Chiefs Foundation, and his design ideas for incorporating training features into fire stations are featured in the "FEMA Fire Station Design Manual." Mitchell is licensed in nine states and is certified with the National Council of Architectural Boards.