When preparing a specification for the purchase of a pumper, there are a variety of options to consider. This includes raw materials that are used to build the body, the fabrication methods and the body styles.
Furthermore, one carefully must evaluate the hose complement, the tools and equipment to be carried and the size of the water tank of the pumper. These items can have a significant effect on the design of the body of the pumper.
Body construction
A variety of choices exist for the construction of pumper bodies. Type 304 stainless steel and aluminum are the two most frequently used materials in pumper body construction, while galvanneal steel and plastic composites are used to a lesser degree. However, generally speaking, each of these materials/construction choices has its advantages and disadvantages.
Stainless steel is the most corrosion-resistant of the four materials, but it also is the most expensive material.
Aluminum generally is lighter but isn’t as corrosion-resistant. It’s the most common body material and is adequate for most applications in the fire service. An exception to that would be in areas of severe weather, where road chemicals and salt are used to treat roads, in which case stainless steel might be a better option.
Galvanneal steel is the least expensive of the four materials, but it also is the least corrosion-resistant of the materials.
Plastic composites are the most corrosion-resistant of the four materials for constructing pumper bodies, but they are the most difficult to repair in case of damage.
All apparatus manufacturers have their preferred methods of fabrication, although some of them offer multiple options. The most common methods of body fabrication that are offered are extruded bodies and formed bodies.
Extruded bodies are built with extrusions that form a skeleton frame, with like materials finishing the compartment floors, sides and top on both the interior and exterior of the framing material. Extruded bodies require the most manhours in design and fabrication and use the most material and, thus, are heavier and more expensive than are formed bodies. Extruded bodies generally are considered to be the strongest of the body designs. These extruded bodies usually are placed on the apparatus chassis assembly in one piece and then are attached directly to the frame of the vehicle.
A formed body uses sheet material that is bent and welded to its desired size and shape. Formed bodies are mounted onto the chassis using a support structure that’s designed to carry the formed body structure and help to support the load of tools and equipment. Generally, formed bodies are lighter in weight and less expensive to fabricate.
Extruded bodies and formed bodies have well-established records of success in the fire service.
Modular bodies are built with each compartment made as a single component most often using the formed fabrication methods. These individual components are bolted together to complete the apparatus body. As with formed bodies, modular bodies are mounted on the chassis using a support structure that's designed to carry the body structure. The advantage with modular bodies is that a compartment can be unbolted and replaced as a result of damage. Ultimately, the bigger decision that a department must make is the style of the body that’s desired.
Body styles
Unsurprisingly, compartment body styles differ significantly. Traditional pumper bodies have approximately 24-inch-deep low compartments on both sides, approximately 12-inch-deep high-side compartments on one side and a ladder rack on the other side. As the need to carry more equipment has grown, more compartment space has become desirable. This has brought about the increased popularity of rescue-style pumper bodies that have approximately 24-inch-deep compartments full height. Some departments have opted for a modified rescue-style body, with approximately 24-inch-deep compartments full height on one side and 24-inch-deep compartments in the lower compartments and 12-inch-deep high-side compartments on the other side.
One must be mindful that, as compartment space is added, water tank size and shape can be affected; hosebed design might change; ground ladders must be relocated from the side of the vehicle; and the height of the body might grow. As an example, by adding full-depth (approximately 24-inch) compartments above the chassis rails, the compartments will occupy the space that the booster tank and hosebed normally would occupy, thus displacing water and hose. As a result, the booster tank must be reconfigured to maintain the department-specified water capacity, which often means that the hosebed floor must be raised and the hose load must be stacked in a narrower area with a higher stack height. (More information in this vein is covered in “Hosebeds: The Domino Effect”.)
Additionally, ground ladders must be stored on a rack that’s above the compartments or in a ladder chute that’s in back of the body of the vehicle, which, once more, potentially can affect the booster tank.
Again, prior to preparing specifications for a pumper, it’s important to carefully inventory all of the tools, equipment and hose that will be carried on the vehicle. Other constraints that must be considered are any height limitations in the station or the response district and any overall length limitations of the vehicle. The combination of the equipment inventory and the height and length constraints will dictate the style of the compartments that will be necessary to store equipment.
Inside storage of equipment is becoming more popular, particularly in areas where the climate is harsher and road chemicals are used to treat roads in inclement weather. This includes carrying ladders in chutes that are in the back of the vehicle. Of course, this reduces the space that’s available for the booster tank and the hose complement and potentially can raise the height of the hosebed.
Growth trend?
As departments try to do more with less, the importance of the size and layout of a pumper increases. The importance of careful planning and of exploring all options increases, too. Don't try to engineer the apparatus. Articulate the needs, how much equipment/weight each compartment must hold, the water tank and hose load capacities and let the manufacturer engineer the apparatus.
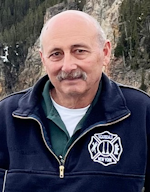
Jeffrey D. Gaskin
Jeffrey D. Gaskin is president of Big Red Trucks Fire Apparatus Consultants. He is a retired captain from the Scarsdale, NY, Fire Department. Throughout his career, Gaskin has been involved in apparatus acquisitions, from needs assessment through specification-writing. He also is a fire apparatus mechanic and holds certifications from Allison Transmission, Detroit Diesel, Hale Pump, Smart Power, Spartan Chassis, Sutphen Fire Apparatus and others. Gaskin is certified by the Emergency Vehicle Technician Certification Commission in six areas: Fire Apparatus Inspection, Maintenance and Testing (F-1); Design and Performance Standards of Fire Apparatus (F-2); Fire Pumps and Accessories (F-3); Aerial Fire Apparatus (F-5); Allison Automatic Transmission (F-6); and Hydraulic Systems (F-8). He can be reached at [email protected].
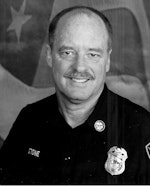
Greg Stone
Greg Stone is a retired 33-year veteran of the Los Angeles Fire Department. His assignments with the department included apparatus and equipment purchasing responsibilities. Additionally, Stone has 25 years of apparatus purchasing experience assisting other departments with their purchasing needs.