The Apparatus Architect: The Apparatus Industry: A Year in Review
The past 14 months presented a number of challenges for apparatus manufacturers, for component suppliers to those manufacturers and for fire department’s that are planning new vehicle acquisitions.
Beginning in early 2022, several apparatus manufacturers announced price increases that would take effect during the first quarter of 2023. These costs must absorb the effect of future labor and material increases and are, essentially, the cost to produce a new rig that will be completed in late 2024 and 2025. This resulted in a large influx of new orders from departments of all sizes as those departments sought to beat the price increases. This, in turn, affected production backlogs, which pushed out new deliveries to 18–20 months in some cases.
As manufacturers began to review their production capacity, it became apparent that, because of supply chain limitations and a limited workforce pool, the extended delivery times wouldn’t improve in the short term.
As the price increases by the apparatus manufacturers were rolled out, surprisingly, the fire service reaction was to step up and place additional orders, particularly those fleet departments that order units on an annual basis, with the timing of the orders based on when funds become available each fiscal year.
By the fourth quarter of 2022, several apparatus manufacturers quoted delivery times in excess of 33 months. Departments that planned to acquire apparatus on commercial chassis found themselves in a position that was similar to that of businesses that rely on the heavy truck market. The latter, with production capacities that are far larger than fire apparatus builders, is experiencing similar supply chain and workforce issues.
Fixed-price contracts for commercial chassis are increasingly difficult to find. The major chassis builders are unwilling to provide a firm price on a chassis that won’t be produced for a few years. Understandably, apparatus manufacturers are gambling on their material costs for apparatus that won’t be produced for an extended period of time. The same goes for being able to provide a guaranteed delivery date for rigs, given the uncertainty of when a commercial chassis would be shipped to them.
The forecast for the balance of 2023 is that the equipment and component supply chain issues will continue. This will result in little improvement on production cycle times. Departments that plan to move frontline apparatus to reserve service or to retire older units will need to continue to operate and maintain those vehicles for longer than they calculated.
Alternatives to new
There are alternatives to ordering a new apparatus at this time, particularly if your department’s apparatus fleet is wearing out, with increased reliance on having reserve units operating with frontline companies. Apparatus that are less than 10–12 years old that have solid drivetrain components and good service records might be candidates for rebuilding, with the goal of extending their life cycle by several years.
Numerous areas of the country have cooperative purchasing agreements by which municipalities can piggyback onto existing orders for apparatus. These cooperative purchasing agreements permit departments to take advantage of the cost savings for units that are ordered. In some cases, these rigs were engineered to confirm the design requirements.
If your department has a preferred manufacturer, your apparatus committee should inquire with the manufacturer’s sales representative to see which units are included on the list of existing orders, to review their configuration to see whether the rigs could meet the committee’s operational needs. A number of county fire departments operate a standardized fleet of engine company and ladder company apparatus. These vehicles might meet your department’s requirements, at a considerable savings compared with the cost of designing a one-off rig that has an extended delivery time.
Another alternative is to review the available stock model or program apparatus that already are built and are immediately available. By researching apparatus builder websites, you can determine the basic vehicle configuration, principal dimensions and production availability. Engine, truck and some wildland units generally are available in common configurations that represent the most frequently requested designs. These vehicles, which might have been built for use as demonstrator units, can save you both time and money.
Proposal review timing
Depending on which platform that your department utilizes to acquire new apparatus, the current market conditions affected portions of the purchasing process.
First, because of the variability in component and material costing, there can be significant price adjustments, with little or no advance warning from the suppliers.
Second, in consideration of numerous new inbound orders by departments, the production backlog can expand by several months in a relatively short period of time. It’s difficult for manufacturers to balance the workflow through both engineering and production for single, one-of-a-kind orders compared with multiple orders for identical units.
For these reasons, once a formal proposal that includes a fixed price is submitted for consideration to your department, a vehicle’s price will be valid for a maximum period of 30 days. Your department’s process should take this into consideration when planning to send specifications for response by the vendors. This enables all of the required legal and political stakeholders to have time to review the proposals and to sign a contract for the new vehicle.
Emissions standards
In March 2022, an executive order, “Strengthening American Leadership in Clean Cars and Trucks,” directed the U.S. Environmental Protection Agency to develop regulations over the next three years to set stronger standards for nitrogen oxide and greenhouse gas emissions from heavy trucks and many classes of vocational vehicles. This will affect the fire apparatus industry.
All diesel engine manufacturers that provide powerplants to the Class 7 and Class 8 truck market are beginning to design the new engine technology to meet the planned standards that are set for 2027. This time frame is important, because many apparatus manufacturers already have production backlogs out to 2025.
Once the new engine emissions technology is developed and tested, apparatus manufacturers that build custom cabs will have to reengineer the engine packaging into their cab structure. The result will have some effect on the cost of custom chassis apparatus and the resulting electronic monitoring systems that will be required.
Although it’s too early to forecast the technological and financial effects of these changes on the apparatus themselves, this might serve as incentive for departments to adjust their fleet replacement schedule, to acquire new vehicles prior to these planned engine emission changes go into effect. Based on how earlier engine emission technology changes affected fleet readiness and out-of-service times, a proactive approach should be considered.
The new NFPA 1900
NFPA’s program to consolidate many fire service standards into a single document was completed with the Technical Committee review and acceptance of the new NFPA 1900: Standard for Aircraft Rescue and Firefighting Vehicles, Automotive Fire Apparatus, Wildland Fire Apparatus, and Automotive Ambulances. The new document replaces the former NFPA 414, NFPA 1901, NFPA 1906 and NFPA 1917 standards. Each of these documents had its own Technical Committee to oversee its document.NFPA 1900, although formally adopted, takes effect for all vehicles that are contracted after Jan. 1, 2024, to allow sufficient time for all parties to review the material and take the appropriate time to adjust to the new requirements. A future The Apparatus Architect article will discuss all of the changes that are incorporated into the new document; however, two areas deserve immediate attention.
Unlike currently, the requirement for a vehicle data recorder (VDR) is omitted from the main text of the new standard. Instead, it’s in Annex A for consideration by the purchaser. The reasoning for the removal of this component varies; however, we highly recommend that any department, regardless of size, consider including a VDR in its requirements, along with other safety equipment, such as frontal and side air bags, a reinforced steel front bumper and aggressive nonslip step surfaces on all areas of the apparatus.
Another change in the new standard is the removal of basic hand tools and equipment that must be carried on the vehicle, whether purchased new with the apparatus or provided by the department prior to the rig being placed into service. This change makes sense: Each jurisdiction and response area has different hazards and structural conditions that affect the type of equipment that must be carried on engines, rescue-engines, trucks and special service units.
The change places all of the responsibility on the purchasing authority and the fire department to provide a detailed hose, tool and equipment list that’s planned to be carried on the apparatus, along with weights for all of these components. This ensures that the chassis gross vehicle weight rating, the axle capacities and other components are appropriately engineered for application.
For departments that are planning new aerial or tower apparatus, the ground ladder complement must be determined up front. This information should be supplied to the manufacturer to verify that the ground ladder banking can be accommodated.
With the high cost of any aerial device, the ground ladder complement should be a minimum of 200–240 feet in various lengths and sizes to meet the needs of the response area. You can stretch hose, but you can’t stretch a ladder if you pull up short.
Neighbors Helping Neighbors
Smaller departments that have modest size fleets and don’t have the resources to provide a spare or reserve engine apparatus should consider working with neighboring jurisdictions to provide regional reserve apparatus for use at several departments. The tools, hose and equipment as well as the maintenance, fuel and insurance costs can be shared by the participating departments to enable a ready reserve engine apparatus to be available for use.
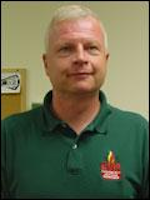
Tom Shand
TOM SHAND, who is a Firehouse contributing editor, is a 36-year veteran of the fire service. He works with Michael Wilbur at Emergency Vehicle Response, consulting on a variety of fire apparatus and fire department master-planning issues. Shand is a member of the Firehouse Hall of Fame.
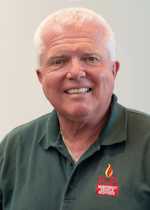
Michael Wilbur
MICHAEL WILBUR, who is a Firehouse contributing editor, retired as a lieutenant in FDNY, where he was last assigned to Ladder Company 27 in the Bronx. He has served on FDNY's Apparatus Purchasing Committee and consults on a variety of apparatus-related issues around the country. Wilbur is a member of the Firehouse Hall of Fame. For further information, access his website at www.emergencyvehicleresponse.com.