During the design and specification process for new pumpers, members often focus on the concepts that are important to them depending on their riding assignments and on-the-job experience. One of the challenges for members who sit on the apparatus committee is to consider all of these concepts without losing focus on the mission of the vehicle. Many of these ideas will appear to benefit the apparatus design, until the initial blueprint is completed and someone on the committee comments on the vehicle dimensions and remarks, “We can’t access some points of our first-due area now. How are we going to improve if the new pumper is 33 feet, 9 inches long, with a 212-inch wheelbase?”
Numerous questions must be answered when developing baseline requirements for a new pumper. Depending on the personnel on an apparatus committee, there might be a wide range of interests in what those folks believe is important from an operational perspective. A driver/engineer might focus on interior dash panel layout and windshield visibility. The officer might have concerns about the amount of space on the right side of the cab, the location of the radio and mobile data terminal (MDT) hardware, and access to his forcible entry tools. Crew members might have opinions on the arrangement of rear cab seats, locations of handrails to permit safe access, and the height of crosslay and rear-body attack lines.
Three distinct areas affect a pumper’s wheelbase and overall length. Apparatus positioning and placement on the fireground largely depends on the size of the apparatus and of the training and experience of drivers/engineers. If the design of a new pumper appears to be quite large on paper, I can assure you that the rig won’t be any smaller or more maneuverable once you take delivery of it.
The size of the cab and the desired seating arrangement affect front-axle-to-rear-of-cab dimensions, ranging from 54–84 inches from most custom chassis builders. The length of the apparatus body depends on the water tank size and the desired compartment configuration and hose load, with this area having the greatest degree of options to accommodate the department’s requirements.
After the criteria for the cab and body are determined, the design of the pump panel and the required width to accommodate the pump, intakes, discharges, gauges and instrumentation along with foam systems and components, which must be housed over the pump, all have an effect on the final design. The layout and design of the pump panel is one of the most important pieces of real estate on the apparatus but often is overlooked during the specification and design process.
Options other than standard
Although many manufacturers have a standard pump panel design, to include piping runs and termination points for discharges, the apparatus committee should specify the location of certain pump instrumentation, suction and discharge valve controls, and other components. The pump panel design on a pumper should be laid out in a logical fashion that meets the operational needs and standard operating guidelines of the department.
As a committee reviews pump panel layouts at trade shows or during inspections of different manufacturers’ new deliveries, it will become apparent that there are numerous concepts as to how pump panels should be designed. The location of major controls, such as the governor, throttle, tank-to-pump, tank fill and master gauges, often are in different locations, as determined by the manufacturer’s engineering staff based on manufacturing efficiencies and predetermined standard locations. Some of these designs might work for your department. However, understand that the layout of the left- and right-side pump panels, along with the piping runs and placement of gauge lines, are based on ease of manufacturing and might not consider a department’s desired flow and friction loss through the piping, particularly with large-diameter and rear-body discharges.
The preconstruction conference is the time to review how pump panel gauges, intakes and discharges will be laid out, considering the width of the pump panel and the degree of complexity of the pump system, including foam systems. The department should include requirements with its bid for the successful manufacturer to provide a detailed layout of the pump panel at the preconstruction conference for review and approval. This documentation isn’t provided as standard. In some instances, there’s a cost to provide this level of detail prior to the start of production.
Pump panel width
The width of the pump panel affects the wheelbase and overall length of the vehicle and can range from 38–60 inches, depending on the make and model of fire pump, piping arrangement, number of crosslay hosebeds and foam system components. On aerial devices, room for the cradle support also is a factor. Although the concept should be to keep the pump width as compact as possible, consideration should be given to pump access for repairs and maintenance. This can be accomplished in several ways, including by providing removable panels for the left-side panel discharges, a full-height, vertically hinged door on the right side above where the drain valves are positioned, and front access on custom chassis that are equipped with a tilt cab. Depending on the amount of fixed equipment that’s used as booster reels, hydraulic generators and electric cable reels are located above the fire pump; removable floors can be provided to gain access to valves and piping.
Electric valve controllers
When compared with manual pull rod controls or gear-operated valves, which require straight-line runs from the panel to the valve, the use of electric valve controllers can reduce the size of the pump panel. Depending on which valves are outfitted with electric controllers, consideration should be given to providing access points to manually override the valve in the event of an electrical malfunction.
Although electric valve controllers generally have proven to be reliable, wherever possible, manual controls should be utilized, particularly for tank-to-pump, tank fill and discharges where preconnected lines are utilized.
Pedestal-style pumps
One current trend is to utilize pedestal-style fire pumps that have compact suction and discharge manifolds. This can shrink the size of the panel and, when combined with electric valve controllers, can require less than half of the space of the traditional pump panel. If this design permits your department to carry more equipment or to reduce the overall length of the apparatus, this design might have some merit.
When evaluating this style of panel design, pay attention to the location of intakes and discharges and their capability to support large-capacity fire flows with multiple large-diameter intakes and a minimum of 4-inch full flow valves and piping for large-diameter-hose discharges.
The position and size of intake and discharge gauges should be given consideration by the committee. Although the apparatus industry largely has standardized on 2½-inch gauges with a pressure range of 30-0-600 psi, master gauges are available in 4½- and 6-inch sizes with different pressure ranges. There is a nominal cost difference to specify the larger 3½-inch gauges, which might be beneficial for a department’s operations.
Hosebeds’ affect
If a department utilizes crosslay or transverse hosebeds, the height from the ground and clear width of each hosebed should be detailed in a specification.
Transverse hosebeds should be no more than 62–64 inches from the ground to permit safe and rapid deployment.
How a department loads attack lines has an effect on how the transverse beds should be arranged, along with the position of the discharge piping. Consider having the transverse bed discharge terminate directly under the respective hosebed, which permits rapid extension of the line when needed and reduces the friction loss in the chiksan swivel.
Large-diameter intakes
The pump piping and valve size for attack line should be determined based on a department’s desired gpm target flows for both small- and large-caliber streams. These flow rates and desired pressure loss must be called out in specifications and then verified at the final inspection.
To develop its rated pump capacity, a pumper should be designed with multiple large-diameter intakes to supply the fire pump. Front-, side- and rear-suction inlets should have the capability to control at least two of these intakes from the left-side pump panel area. Using a power-operated valve that has an air bleeder and manual override enables the pump operator to control the water supply without having to run around the apparatus.
The location and length of attack lines depend on a department’s response district and the standard staffing for the engine company. Some departments rely on multiple preconnected attack lines that range in length from 100–400 feet, with static bulk beds or 2½- or 3-inch hose to fill out extended hose lays. If an organization has a standard attack line complement, this can be integrated easily into the vehicle design. (The dimensions of existing apparatus can be replicated for use on the new rig.)
Consider the driver/engineer
One of the greatest challenges for an apparatus committee is to determine the desired panel configuration that will meet the operational and training needs of the organization—as opposed to just throwing all of the components into the smallest available space. The engine company driver/engineer has one of the most important jobs on the fireground. Anything that can be done to make this person’s job safer and easier enhances the overall operation greatly to ensure success.
Pump Panel Lighting
The pump panel area should have adequate panel lighting to illuminate both the left- and right-side panel areas (red arrows). This lighting should extend to the top area above the pump, particularly when the unit is equipped with a deck gun or wagon pipe. Depending on the width and layout of the panel, the manufacturer’s standard lighting configuration might not be sufficient to illuminate all of the working area.
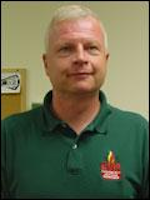
Tom Shand
TOM SHAND, who is a Firehouse contributing editor, is a 36-year veteran of the fire service. He works with Michael Wilbur at Emergency Vehicle Response, consulting on a variety of fire apparatus and fire department master-planning issues. Shand is a member of the Firehouse Hall of Fame.