South Metro, CO, Fire Buys Used Tiller to Train Firefighters Before New Ladder Arrives
When the South Metro, CO, Fire District, south of Denver, prepared to take delivery of a new tractor-drawn aerial (TDA) ladder, they purchased a used tiller to provide their drivers with extensive training to prevent costly accidents.
Ahead of the delivery of their new TDA, which was outfitted with a large cache of heavy rescue equipment, crews took to the training grounds to practice the cumbersome skills needed for driving, tilling and communicating between the two drivers.
Tiller combines two apparatus
Both of South Metro’s fire stations with heavy rescue staffing are located in busy areas. As the fire district grows, they each take on additional duties.
“We realized that every time that aerial (Ladder 34) was out on a call, the rescue wasn't cross-staffed,” Division Chief Scott Richardson told Firehouse.com. “And with a lot of that we're not getting to have that (rescue) equipment with us.”
Station 34’s technical rescue resources were carried on a heavy rescue rig and a tractor-trailer outfitted by Hackney to carry their collapse rescue equipment.
“When we decided to combine two apparatus, this allowed us to have all the equipment for our rapid response and needs. It’s got the technical rescue tools for the initial operation.”
The new tractor-drawn Ladder 34 was the first of two, replacing mid-mount tower ladders.
Buying a used tiller
As departments across the country are facing long out-of-service times with what seems to be an uptick in apparatus crashes and longer manufacturing or repair times, the department adopted a protective approach.
After running the numbers, they realized that costs and down time for front-line apparatus can create a burden on the firefighters who rely on the equipment. Richardson, for example, said they found that the cost to repair damage to the rear compartments out of a mid-mount tower ladder was in the range of $80,000. At a minimum, that’s about six months of out-of-service time, forcing crews to carry less equipment or use multiple rigs and slowing the vital resources from arriving.
During the planning process, Richardson said they spoke with departments in the Northwest who operate tillers, and they recommended that early training would be paramount, but they did not have access to any TDAs locally.
“Understanding that and knowing that a new tiller costs over $2 million, we wanted to try to take advantage of firefighter’s eagerness and see if we could find a tiller,” he explained. “That the credit goes to the technical team coordinator at the time.”
Chief Brett Pickford began searching for a new-to-them tiller and, after extensive research and an exhaustive search, he found one for sale in Oxford, CA.
They pitched the concept to their fire board, who agreed to move forward with the purchase.
The 1990s Seagrave tiller came with a price tag of $30,000, but the experience gained from that price tag would provide South Metro firefighters with training that was worth it, Richardson said.
Richardson added that while the mechanical parts of the truck are in working order and the aerial passed its annual testing, the TDA is not suitable to serve as a frontline apparatus.
The rig was equipped with the old communication style of bells, which signal movements and headsets to allow more concise communications.
Driver training with the used TDA
Each operator, Richardson said, received more than 50 hours of operating time on the used TDA.
“The tillering position required extensive training, which we took to heart.”
He said they were fortunate to have some members, who were tiller operators previously in California fire departments, who gave them a chance to start training with their experiences.
Each driver was given a task book, compiled by the seasoned tiller operators, to complete during training. Check boxes included communications and language/terms, operations and driving skills.
The training started with practical time on the drill pad, learning the little things and then they spent hours on the roadways, driving, backing, turning and positioning. Each driver was training during both daytime and nighttime hours to hone their skills.
Richardson said the ability to train someone in the tiller position at the rear proved invaluable, because the need to turn in the opposite direction does not come naturally.
Even those drivers experienced with operating the tractor-trailers in the department were challenged, he said. “When you're backing a tractor trailer, if you turn the wheel right, the back of the truck goes right, if you turn left, the back of the trailer goes left. It’s the opposite for these tiller operators.”
“Muscle memory for tractor trailer drivers was the hardest part,” Richardson added.
By the end of the training, Richardson said, “The biggest change for them was learning on a 1990s Seagrave aerial and then moving to a brand-new Pierce tiller, which is like going from a Volkswagen bus to the space shuttle. It has all the different bells and whistles and cameras and mirrors."
Still the training with the older rig proved valuable with the basics of a two-person operating crew, allowing them to focus on steering and communications. He said they learned about spatial awareness, which is often overlooked when you’re not accustomed to tillering.
“The principles of driving—whether it's the most high-tech vehicle or the most low-tech vehicle—and the principles of driving a tiller, the operations, the communications to collaborate to make those turns were still the same.”
Communication is vital during operations, training
Richardson said one of the lessons they learned was that communications between both drivers is key to ensure they are coordinating their next move. Taking it one step further, they outfitted the used tiller with another headset for the trainer to be involved in the communications.
“We realized that having a David Clark headset for a trainer on the back while they're on the drive pad is extremely helpful,” Richardson said.
Each tiller will have three engineers assigned to the tractor and three to the tiller—a pair for each shift—and while they may not always work together, that training on the front end allowed them to work out the kinks.
Richardson said that if a run that comes in just 30 seconds into the shift, it doesn’t allow them time to understand each driver’s nuisances.
“From a communication and a collaboration standpoint, it's a great team-building exercise because the person in the front and back have to be on the same page, even if they haven't spent a lot of time working together.”
What’s next for the training tiller?
“It can’t really be a reserve apparatus for us because it doesn't have a pump or water,” Richardson said. “However, we have trained hundreds of hours with all of our tiller operators with that $30,000 investment before the $2.2 million tiller got here.”
Since the used TDA will not be used as a frontline apparatus, they will keep it for training their members on driver operations and fireground skills.
Richardson said a nearby department that was purchasing their first tiller inquired about using the old Seagrave for training.
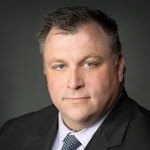
Peter Matthews | Editor-in-Chief/Conference Director
Peter Matthews is the conference director and editor-in-chief of Firehouse. He has worked at Firehouse since 1999, serving in various roles on both Firehouse Magazine and Firehouse.com staffs. He completed an internship with the Rochester, NY, Fire Department and served with fire departments in Rush, NY, and Laurel, MD, and was a lieutenant with the Glenwood Fire Company in Glenwood, NY. Matthews served as photographer for the St. Paul, MN, Fire Department and currently is a photographer for the Fort Worth, TX, Fire Department.