The overhead speaker sets your company in motion: You are dispatched to a residential area for an odor of gas, with multiple calls reporting the same odor. While you are responding, you bring up the area in your mobile data terminal (MDT), look for surrounding hydrants, and notify headquarters to confirm that the gas company is responding to the scene. Suddenly, a loud explosion is heard, and a visible column of smoke is now seen coming over the tree line. This is no longer an odor of gas call; this is a technical rescue assignment for an explosion with collapse, secondary to the reported gas odor. Upon arrival at a chaotic scene, you see that two buildings have been leveled and multiple structures show significant damage. What will you do when you are faced with this?
Scenarios like this play out more often than you might think. As such, it’s important to understand the potential for a large-scale collapse event in your own community. Here we’ll offer some tactical and strategic considerations for the collapse response, reviewing personnel capabilities, resources, and building construction factors, and we’ll define the phases of collapse rescue.
Personnel capabilities and resources
In developing the specific collapse response needs of your community, the best starting point is an operational capability check. Specifically, what type of incidents are your resources capable of handling with local support? Your in-house capabilities should be categorized by the following levels:
- Awareness: Minimum abilities for assessment and requesting resources, surface victim removal, content removal, etc.
- Operations: Minimum level to operate in most unreinforced masonry (URM)-constructed structures, conduct entry and removal operations, plus some limited shoring.
- Technician: Abovementioned skills, plus capabilities to operate in concrete/steel/reinforced frame structures.
In addition to personnel, resources and PPE will be needed to adequately protect the rescuers. While turnouts provide some protection during the collapse response, they can become bulky and cumbersome during the operational period. Many departments have outfitted their rescue companies with lightweight urban search and rescue (USAR) turnouts or Nomex coveralls for these responses.
At a minimum, personnel should be outfitted with helmets, work gloves, eye protection, dust masks and half-face respirator masks, body substance isolation (BSI) equipment, hearing protection, flashlights, steel toe boots with ankle support, knee and elbow pads, radios, and atmospheric monitoring equipment. Most importantly, when your department makes the investment in this equipment, ensure that there is a policy in place that enforces its usage.
Most departments have resource lists that are available for handling single-point responses that are dealt with on the local level, but multiple-point responses are a different story. Multiple-point responses are spread out over a larger area, involve many locations, and will require a larger resource pool, including outside agency support, large-scale incident management support, and technical expertise. An inventory of the surrounding communities can help identify critical resources, such as mutual-aid companies, engineers, logistical support, and state or local experts for response. This review should be done annually in order to keep the operational plan updated and accurate. Sunday morning, at 2 a.m. is not the time to start shopping around for a crane to respond to the scene. Do your homework before the incident.
The collapse scene is not the place for freelancing and separation of crewmembers. Things can go wrong in an instant, and injuries and fatalities are often the result. It is vital that all the responders understand that scene safety is an integrated part of training and discipline. Personnel must foster an attitude that identifies their skills and limitations and embraces the “Team Efficiency Concept.” In his book, “Engineering Practical Rope Rescue Systems,” Mike Brown defines the Team Efficiency Concept as “refining team member interaction to be productive without waste in every team endeavor” (Brown, 2000, p.36). This concept enforces the maximization of the members’ efficiency while considering safe operations as of equal importance. Working as a team for safer operations, staying focused on the assigned task and bringing the right equipment initially during the response are all examples of team efficiency. Your “team” should strive to coordinate, train and respond together with other local resources in a professional and commonly acceptable fashion.
Building construction
One of the most significant areas of proficiency for all firefighters is building construction. From a rescuer’s standpoint, it will become necessary to push, pull, cut, breach, lift or tunnel through the materials that make up the collapsed structure. Over the years, construction methods and techniques have changed, but what haven’t changed are the laws of physics.
It is imperative that firefighters have a thorough understanding of how buildings are constructed and, more importantly, how they can collapse. Many officers have learned their decision-making process through experiences on the fireground; however, the clues that existed in the past, such as sagging floors, racking windows and doors, and smoke coming from separations in walls may all serve to be “too little, too late.” Today, buildings are built with approximately half the materials used years ago but are creating almost five times the potential rate of heat release, resulting in faster destruction of structural components—and quicker collapse. It is critical to understand the physical aspects of construction, mainly gravity, loads and forces.
Gravity has been called the greatest of firefighter enemies, as it is unforgiving, unpredictable and always a factor for consideration. Twenty-four hours a day, seven days a week, gravity is continually exerting forces on a structure. Overall, these stresses may not be visible, but they are still in place.
Loads can be defined as a force or action that is a result of the weight all building materials, occupants, environmental effects, and movement and changes that are applied during the normal use of the structure. Some loads are simply defined, such as a dead load, which includes the weight of structural components and all materials attached to the structure, and live load, which include anything not permanently affixed to the structure, such as furnishings, occupants, and transient (temporary) materials and occupants. Some can be environmental, like wind loads and distributed loads of snow on a structure’s roof.
When discussing forces, it is important to define two separate concepts: stress and strain. Stress, mostly measured in pounds per square inch (psi), is the result from the external force that is applied to the structural component. Conversely, strain is the actual deformation of the component when it is stressed. Strain is usually measured per inch of original length of the component. Generally, there are a few types of forces to be identified:
- Compression: a squeezing, compressive force that is placed on an object, pushing both ends toward each other (e.g., a loaded upright column)
- Tension: a pulling force that is placed on an object, pulling both ends apart (e.g., a steel cable on a suspension bridge)
- Bending: a directional force placed on the end of an object, with an opposing force placed in the middle of an object (e.g., a load placed on the center of a floor joist or continuous beam)
- Shearing: a force tangential to the object on which it is acting upon (e.g., a pair of scissors, a rivet in an I-beam, with a downward force on the rivet)
- Torque: a twisting or torsional force placed on a structural component (e.g., a nut on a bolt)
It is also important that the responders are well versed in the signs and characteristics that a collapse may occur in their jurisdiction, such as:
- Age of the building: Most buildings, as a rule of thumb, have a life span of 75 to 100 years. Lack of proper maintenance will drastically reduce their life span.
- Weather: Buildings that are left open to the elements will deteriorate and rot more quickly.
- Improper alterations: Building owners who take shortcuts or alter structural components without a proper knowledge of construction are inviting trouble.
- Natural disasters: Hurricanes, tornadoes and other storms can wreak havoc on a community, and can lead to a large collapse response, quickly overwhelming local resources.
- Construction collapses: There have been incidents where accidents on construction sites have resulted in catastrophic failures of structures.
- Vehicles into buildings: While most responders treat these incidents as nothing more than “nuisance” alarms, the damaged component can result in a domino effect, bringing down the rest of the structure without any warning.
- Gas explosions: The routine “smell of gas” call can turn deadly for responders. There have been cases across the country where firefighters have been injured and killed while investigating the source of the smell.
- Fires: The incident commander is faced with two problems at these incidents. The first problem is the access to the firefighters who may be trapped due to the collapse. The second problem is that the fire still must be extinguished. Many departments have focused all their resources on rescue and none on suppression, with catastrophic results.
Knowing what materials were used in the construction process of these buildings will better prepare the rescuer to defeat the materials.
Types of collapse patterns
After responding to the collapse, identifying the type of collapse that occurred will be vital. Knowing what type of collapse will help identify the type of voids created—voids that may provide some safe havens for victims. It will also help identify the shoring that will have to be incorporated prior to the rescuers making entry into the debris pile. Finally, it will allow the incident commander to evaluate the scene to determine the safest areas for operations, staging, and logistical needs of the incident.
- Lean-to floor collapse: This collapse occurs when the roof or floor supports fail on one side of the structure, and the opposite side of the floor is still connected to the wall. It results in a void space that is close to the remaining wall.
- V-shape floor collapse: This collapse occurs when lower walls or floor joists fail due to heavy loads located in the center of the floor. It results in two voids, one near each exterior wall.
- Pancake floor collapse: Destruction of the load-bearing walls will cause the floor supports to fail, dropping the floors and the roof on top of each other. Voids will be created between the floors where there is debris, allowing for spacing between floors.
- Cantilever floor collapse: This collapse occurs when one or more walls have failed, and the other end of the floor is still attached to the other bearing wall. Voids will be sporadic throughout the debris. This is the most dangerous type of collapse to operate in, and adequate shoring must be in place before operations can commence.
- A-frame (tent) floor collapse: This collapse occurs when the flooring separates from the exterior bearing walls, but still is supported by one or more interior walls or partitions. Voids are created near the center of the structure.
On scene operations
Let’s now take a look at the actual response to the incident, specifically the five phases of the collapse operation at any given incident:
1. Reconnaissance: This may be the most important phase of the operation. Setting the pace for the rest of the incident, this phase involves determining what happened that led to the collapse, including a six-sided approach (front, rear, both sides, top and bottom) and it can include:
- Nature of the event (terrorism, structural failure, gas leak, tornado, etc.)
- Type of construction and materials used
- Use of the building (occupancy)
- A rough estimate of potential victims (this will vary depending on occupancy)
- Potential additional hazards
- Incident scene control
- Identifying potential survival locations
- Utility control (local control at first, but start the utility company representatives responding in)
- Fire concern (Suppression is a constant responsibility and concern at the incident, regardless of whether fire caused the collapse or was secondary to the collapse)
- Develop the formal Incident Action Plan (IAP)
- Initiate the Emergency Response Plan (ERP)
In the reconnaissance phase, responders are converging on the scene. Unfortunately, responses like this result in resources self-dispatching to the incident. It is imperative that all personnel on scene are identified, accounted for, and properly assigned based on the priorities of the incident. The ERP should have already identified who is responding; now all that needs to be done is to assign them.
Before being deployed, the crews attend a scene safety briefing that should cover LCES (Lookouts, Communications, Escape routes and Safe havens):
- Lookouts: These are safety officers whose critical functions include identifying potentially dangerous conditions and how to mitigate these issues.
- Communications: The formal plan includes what channels each division or group will be operating on. There should also be an agreed upon method of evacuation—make sure everybody knows it.
- Escape routes: A pre-established path to an area of safety is chosen prior to entering. Make note that the safest exit may not always be the fastest, but it is still the safest. Considering scene dynamics, this route may change as conditions change.
- Safe havens: Identify an area of safety immediately. This could be within the Hot Zone and needs to be passed on to everyone working in the area, especially during changes at the end of operational periods.
2. Surface Area Rescue: Initial responders may be faced with multiple victims at the surface, and they may be incapacitated, walking wounded, lightly entrapped or fatally injured. The removal of these victims will take priority, but further evaluation of the pile, along with searching for possible victim locations, should take place simultaneously. This will help identify areas where the search will start so appropriate resources can be deployed there.
3. Void Search: Personnel will be checking areas where survivability may be more likely. Some of these areas include closets, under stairs, basements and cellars, rooms with blocked exits, loose piles of debris, and voids that were created by the collapse. Furniture and belongings that were in the structure prior to the collapse can serve as load-bearing supports for debris, creating voids where victims may seek refuge. Rescuers and technical experts will be constructing emergency shoring in the areas that they enter and build them in the victim’s location to assist in disentanglement operations inside the void spaces.
4. Selective Debris Removal: During the search for victims and survivors, materials and debris will be removed from the pile and replaced with emergency shoring as rescuers traverse deeper into the pile. The direction of travel is determined by the Recon Report and the results of the surface area search. It is wise to stop and go “all quiet” during the operations and listen for sounds coming from victims in the pile. Calls for help, shouts, tapping on metal pipes and beams have all resulted in successful rescues of survivors in many collapses worldwide.
5. General debris removal: Transition into this phase of the operation usually marks the end of the “rescue period,” and the beginning of the “recovery period.” In this phase, the pile is divided into sections for identification purposes. The debris from the pile is removed and sent to another location for further examination. The debris is evaluated for physical remains, personal artifacts and identification, clues to the cause of the collapse, further crime scene analysis, etc. No stone should be left unturned when all potential victims are unaccounted for. Once the material has been thoroughly searched, it should be marked to avoid duplication.
Keep learning
This article has only scratched the surface when it comes to the topic of building construction and collapse. In my own experiences, I have been blessed by having been trained by and with some of the best in the business, and as a fellow emergency service responder, I still am continuing my education in this field.
If this area of responsibility is within your jurisdiction, I highly recommend that you gather all the training and education that you can to prepare yourselves for this type of response, and continue to further your education regularly. Keeping pace with the construction industry is one way to stay current; there are constant changes in the ways these building go up, and some of those changes are the primary reasons why these buildings come down.
In the end, you are responsible for your own safety so continue to do all that you can to protect yourself. Until next time, stay focused and stay safe.
Bonus Material: 5 Types of Building Construction & Inherent Hazards
Type 1: Fire-Resistive
These structures are made from non-combustible materials that do not add to the fire load of the structure. They are usually massive steel components that are encased in concrete and that provide a higher fire rating on the components. There may be cast-in-place concrete, or the slabs may be poured off-site and hoisted into place. These structures are considered the most resistant to collapse.
Inherent Hazards: Concrete takes approximately 28 days to fully cure to a point that collapse is no longer a threat. However, the pace of construction moves much faster than that. There have been cases where collapses have occurred when the formwork has failed when the compressive load from the upper floors has over-taxed the pre-cured floor. Further, when the slabs are laid into place, they are connected in a variety of methods. Some of these connection points have been the result of a catastrophic failure of the structure. Inspection of these types of structures may reveal deteriorating concrete, spalling that is deep enough to expose support rods, and cracks that can lead to a collapse.
Type 2: Non/Limited Combustible
These structures are similar to Type I structures, with one major difference: The structural steel is encased with a light fire-resistive coating, such as sheetrock or a sprayed-on coating. These structures employ a lightweight parallel steel bar joist system that holds up a corrugated steel roof deck. Because much of the structural steel can be exposed to the properties of fire, these types of structures are considered the least resistant to collapse.
Inherent Hazards: The classification of “limited” combustible comes from the materials that make up the roof covering, which, when involved in fire, can lead to a rapid failure of the roof. This type of structure is commonly used for commercial occupancies that require a large open space, such as strip malls. These malls have many windows in the front wall, and that opening is spanned with a steel lintel that will support a free-standing parapet wall. If this lintel is compromised in any fashion, it can result in a complete failure of the parapet wall. Furthermore, there are larger buildings of this type that employ a tilt-slab construction method, which employs a pre-cast wall slab that is tilted into place. Each slab is braced with steel rods or rebar and insulated at the sides with each other, using a foam insulator strip and caulking. Anchor plates are then used to attach the roof steel bar joists to the exterior walls, tying the integrity of the walls and the roof into each other. The result will be a catastrophic failure of either a large portion or all of the structure.
Type 3: Ordinary
These structures use load-bearing walls of masonry construction, while the roof and the floor can be made of wood. Older buildings of this design can be either balloon-frame or braced-frame construction on the interior.
Inherent Hazards: Similar to Type 2 structures, older buildings may also have a parapet wall at the roof line, but with a twist: There may also be a cornice, a decorative extension of the roof boards to give the appearance of an overhang from below. The cornice may also stand alone without the presence of a parapet wall. But, the cornice may be as old as the building and be unstable due to its age and its exposure to the elements. Also, these structures that span over 25 feet will have an additional steel I-beam support called a channel rail installed in the walls to aid in supporting the compressive load of the floors. Braced walls are another sign that the wall has been compromised. Spreader plates, in the shape of stars, plates or channel sections, are used on the outside of masonry walls to provide some stability to the structure. These plates are connected with the use of unprotected steel or steel cable. Generally, spreader plates that were installed when the building was designed will be in some symmetrical fashion, but beware the spreader plates that are irregular in placement; they will signal a severe problem.
Type 4: Heavy Timber
These structures resemble the construction methods as described in Type 3 buildings, but the difference is in the size of the materials used in construction. Exterior walls are brick or other type of masonry, but are often doubled in width, compared to similar Type 3 construction. The interior wood members are larger as well, with the columns being a minimum of 8 inches by 8 inches in diameter, and joists must be at least 6 inches by 10 inches in diameter. These buildings used to house commercial occupancies, but can now be found as condominiums, churches and museums. The large materials used in their construction make these structures the second-most resistant to collapse.
Inherent Hazards: The larger surface-to-mass ratios of their structural components make these buildings more resistant to collapse. However, years of neglect, shoddy renovations, and weak connection points can cause complete failure of these buildings. The floor systems are of the self-releasing type, made up of fire-cut beams. The ends of the beams are cut at an angle and sit in a pocket in the wall. The principle here is that if the floor were to fail, the joists would not lever the exterior masonry walls, causing them to break and collapse. However, these fire-cut joists limit the amount of operational time that suppression crews have during a structural fire. Furthermore, once the floors fail, these massive walls become free-standing and can fail.
Additional hazards in these structures include the heavy timber truss. These trusses can be parallel chord or bowstring. Many times, they are hidden behind a parapet wall, but identifying these hazards is vital. These trusses can span up to 20 feet on center, so if one section fails, it will open a hole in the roof that spans 40 feet wide. These trusses incorporate the use of hip rafters, which connect the last trusses to the front and rear walls of the structure. When the roof fails, these rafters transfer the roof load to the front and rear walls, pushing them out violently. Anyone who is in this collapse zone is in immediate danger.
Type 5: Wood-Frame
These structures contain walls, floors, roofs and other structural members made entirely of wood. Wood is the primary load-bearing material within the structure. The size of the wood board will vary depending on its use and type of construction. These structures can be made up in one of the following methods:
· Braced frame: Also referred to as “post and beam” or “post and girt,” these buildings are made up of vertical posts and horizontal beams/girts. They are held in place using a “mortise and tenon” connection, pinned together with a pin called a “trunnel."
· Balloon frame: This structure incorporates wall studs that run continually from the foundation all the way up to the eaves line, with no inherent fire stopping between floors.
· Platform frame: This type is constructed using a framing system, which all studs terminate at one story in height, and the floors provide some sort of fire-stopping.
Inherent Hazards: As these structures are all wood, there is no consideration made to the lower floors to help support the additional load of the upper floors. The 2 x 4 wall studs may in fact be holding up an entire upper floor, with no built-in compensation supports to consider. Further, many of these structures have a veneer wall, made of decorative masonry materials, to accent the front side of the building. These walls are attached to the wood wall, placing an eccentric load on the wall that it is not designed to handle. Lightweight construction components, such as trusses, truss joist I-beams (TJIs) and oriented strand board (OSB) can be found in all types of construction, but are much more prevalent in Type 5 buildings. Additionally, buildings are being built with larger square footage but are being constructed with half of the materials that were used in the past, creating a structure that will collapse much faster than earlier construction methods.
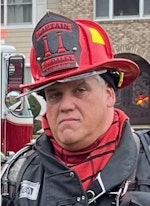
Michael Daley
MICHAEL DALEY, who is a Firehouse contributing editor, is a 37-year veteran who serves as a captain and department training officer in Monroe Township, NJ. He is a staff instructor at multiple New Jersey fire academies and is an adjunct professor in the Fire Science Program at Middlesex County College. Daley is a nationally known instructor who has presented at multiple conferences, including Firehouse Expo and Firehouse World. His education includes accreditations as a Chief Training Officer and a Fire Investigator, and he completed the Craftsman Level of education with Project Kill the Flashover. Daley is a member of the Institution of Fire Engineers and a FEMA Instructor and Rescue Officer with NJ Urban Search and Rescue Task Force 1. He operates Fire Service Performance Concepts, which is a training and research firm that delivers and develops training courses in many fire service competencies.