Industry Insights: Particulate-Blocking Hoods - Testing for Durable Protection
Editor's note: Industry Insights are sponsored blogs submitted by manufacturers and suppliers serving the fire service industry.
In addition to traditional hoods, the 2018 edition of the NFPA 1971 Standard now includes an option for certifying hoods with particulate-blocking protection. When you are selecting a particulate-blocking hood, it is important to understand the test requirements for this certification because it is relatively new to the industry. It is also important to understand what other tests are being done in the industry to evaluate product construction and performance during use.
NFPA testing requirements
The tests for certification to the Particulate-Blocking Option include the Total Heat Loss (THL) test and the particulate-blocking test. You are probably familiar with the THL test that is used for turnout gear; however, the THL requirement for hoods is higher (325 W/m2 minimum) compared to turnout gear (205 W/m2 minimum).
The particulate-blocking test requires blocking at least 90 percent or more of the particulates with a size from 0.1 to 1.0 microns (µm). This test is performed on six specimens cut from rolls of new materials used to make the hoods. Three of the specimens are preconditioned, which includes 20 launderings and two convective heat cycles. The other three specimens are tested without preconditioning. If the average percent efficiency of each set of specimens is 90 percent or greater, the hood meets the requirement. The higher this percentage is, the more protection the hood is likely to provide. For example, the GORE® Particulate Hood blocks 99.9 percent of the particulates per this test.
Additional industry testing
While the particulate-blocking test provides good information about the material specimen’s ability to block particulates, the test does not evaluate the hood’s performance at the system level (i.e., when being worn as part of an ensemble).
You may be familiar with the Fluorescent Aerosol Screening Test (FAST) that some manufacturers are using to evaluate their hood’s ability to provide protection while being worn. This test is not part of the Standard’s requirement for particulate-blocking hoods. However, it is important because donning the hood correctly, wearing it as part of an ensemble, and how it interfaces with other components can affect the hood’s particulate-blocking performance.
For example, at W. L. Gore & Associates, we employed two additional testing methods that go beyond the Standard to further verify performance. First, we used FAST to verify the system-level performance and durability of the GORE® Particulate Hood when new and after being washed 100 times at a verified ISP. The results showed virtually no fluorescence for either the new hoods or the hoods that had been washed 100 times. We then repeated the particulate-blocking test to compare new materials with materials that had been washed 100 times. The results for the hoods after the 100 washes were the same as the results for the new hoods — 99.9 percent particulate-blocking efficiency.
Seam testing
The particulate-blocking test is performed on specimens cut from rolls of materials used to make the hoods. The test does not evaluate the impact of the hood’s design and construction on the particulate protection performance. For example, the seams of the finished hood are not tested to determine whether particulates are able to pass through the stitch holes.
At Gore, we decided to test some particulate hoods, including their seams, so we contracted with an independent, third-party laboratory to perform a smoke test on the seams. The lab tested the seams from four different hoods that were on the market as of early December 2017.
Samples of hoods were cut and measured to ensure that their seams could be adequately tested. A smoke machine was used to determine whether smoke was able to pass through the seams. The airflow and pressure drop was set to achieve conditions as close as possible to those identified in the NFPA particulate-blocking test for each hood. If smoke could pass through the seam, particulates specified in the range for the particulate-blocking test of the NFPA 1971 Standard could likely also pass through the seam.
It’s important that the hood continues to provide protection from fireground particulates even after laundering. Therefore, we asked the lab to repeat the smoke testing on hoods that had been washed 100 times at a verified ISP.
The results of these tests were very interesting. Watch this video to learn more.
When you are selecting a particulate-blocking hood, it is important to understand what testing methods are used in the industry, including those required by standards and those that test performance beyond the standard. The results of both of these types of tests are important in helping you differentiate among particulate hoods available on the market today. For more information about these test methods, visit GOREHoods.com to download a white paper, Ensuring Certified Protection and Long-Lasting Durability in Particulate Hoods.
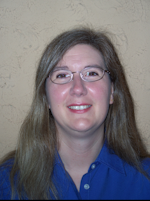
Holly Blake
Holly Blake is a product manager with W. L. Gore & Associates. For approximately years, Holly has focused on developing new technologies for the fire industry, with primary responsibility for CROSSTECH® moisture barriers and the GORE® PARALLON™ liner system. She also works with other research teams on breathable technologies for the fire industry — the most recent being the new GORE® Particulate Hood. Holly holds a Bachelor of Science degree in chemical engineering from Lehigh University. For information about Gore’s products, visit GoreProtectiveFabrics.com.