If you were alive in 1968, you might remember the phrase “You’ve Come a Long Way, Baby.” It was an advertising slogan for a brand of cigarettes. Having personally ridden the back step of fire apparatus in the 1970s and in the early 80s and having seen how far that the U.S. fire service has come since the NFPA required four-door enclosed cabs in 1991, that slogan surely fits today’s fire apparatus as it relates to vehicle and firefighter safety.
FDNY was an early leader in this safety effort, requiring four-door enclosed cabs after the riots in the late 60s, to prevent members from being struck by objects that were thrown by rioters, not to mention protection from gunfire. Some two decades later, the NFPA made it a requirement in NFPA 1901: Standard for Automotive Fire Apparatus.
Custom enclosed cabs today have roll cages as an integral part of their design to protect firefighters during rollover.
FDNY further strengthened its apparatus specifications by requiring a steel reinforced front bumper to prevent intrusion into the cab during apparatus accidents to protect personnel in the front of the cab.Braking
Apparatus have gotten faster (higher horsepower engines) and heavier (increased axle capacity). Along with that came a need for enhanced braking. The 1991 revision of NFPA 1901 required that every apparatus that weighs more than 33,000 lbs. must be equipped with an auxiliary braking system.
FDNY, using technology in conjunction with Seagrave, Telma (drive shaft, gearbox and drive axle retarders) and anti-lock braking systems, sought to have skid-free braking, including via an auxiliary braking system. FDNY specified in the apparatus an electric driveline retarder that interfaces with the computer that controls the anti-lock braking system. Initially, when the apparatus operator let off of the accelerator pedal, four electromagnets grabbed hold of the drive shaft at the same time to bring the apparatus to an abrupt stop. Realizing that wasn’t going to work, engineers who worked with FDNY set up the auxiliary braking system so that two electromagnets engage when the operator lets off of the accelerator pedal and the other two electromagnets engage once the operator depresses the top of the brake pedal before actuating the service brakes. There are no on/off switches for the auxiliary brake system; it always is on. The only way that the system shuts off is when the anti-lock brake computer senses wheel lockup, at which point the anti-lock brake computer shuts off the auxiliary braking system in milliseconds. Once the computer senses that the wheels again are spinning freely, the auxiliary braking system is restored in milliseconds.
Seat belts
Early in 2003, the first of many safety enhancements in the fire apparatus industry that were to emerge in a relatively short amount of time was unveiled. It used air bags, pyrotechnic buckles and electronic sensing technology. The RollTek system was a joint venture between seat belt manufacturer IMMI and Pierce Manufacturing.
When an imminent rollover of the apparatus is sensed, advanced safety systems activate. This safety system activation includes buckle pretensioners and side air bags. When deployed, the system protects firefighters’ head and neck.
In 2007, IMMI introduced frontal air bags, marketed as 4Front. Although similar to what you might find in an automobile, the system is more complex because of the heavy-duty construction and different variations of fire apparatus cabs. The 4Front system comprises a steering wheel air bag and an officer knee airbag. (A driver knee air bag is optional.) When a sensor determines a frontal crash, the frontal air bags deploy.
When purchasing an apparatus, RollTek, 4Front or both systems can be specified.
Unfortunately, under the revision to NFPA 1901 that’s underway, the VDR requirement is dropped. A reference to VDR will be contained in the annex as a recommendation. The reason that was given was to reduce the cost of apparatus—and that “nobody used it anyway.” Perhaps nobody used it because there never was an explanation as to all that the VDR could do and that, in most cases, no training was offered or given. This prompts the question: How many expensive components are installed on apparatus today with little or no explanation or training?
To continue its leadership in cab safety, starting in 2010, FDNY conducted research on seat belts and their lack of use in FDNY apparatus. It was determined that firefighters weren’t wearing seat belts—not because they didn’t want to but because the seat belts that were installed in apparatus didn’t work very well or, in some cases, not at all.
In 2010, IMMI and FDNY developed seat belts that account for the mass of bunker gear, to provide more retraction of the seat belt, so the belt won’t get caught in the Nadar pin and fray.
In 2007, the National Institute for Occupational Safety and Health (NIOSH) authorized a series of anthropometric studies.
Anthropometrics is the science that defines physical measures of a person’s size, form and functional capacities. Applied to occupational injury prevention, anthropometric measurements are used to study the interaction of workers with tasks, tools, machines, vehicles and PPE. This is done in particular to determine the degree of protection against dangerous exposures, whether they are chronic or acute.
NIOSH’s series of studies were historical in nature: Firefighters never had occupational anthropometric studies conducted in their workplace. More than 1,000 firefighters from all over the United States were studied. Most of those individuals got full body scans. Some of the findings of the studies were applied to the seat belt project that was undertaken by FDNY and IMMI. For example, when firefighters are dressed in bunker gear, their body mass is increased by 30 percent.
Over the course of 18 months, more than 500 FDNY apparatus underwent retrofitting to have the new seat belt installed.
Improvements to Come
Over the course of my fire service career, the improvements in firefighter safety, in general, and fire apparatus, in particular, have been dramatic and have prevented firefighter injuries and deaths. What does the future hold for fire apparatus safety?
It would seem that the application of onboard electronics that’s used to warn fire apparatus of the approach of other fire apparatus or other emergency vehicles at intersections is in the offing. Technology already exists to warn civilian vehicles via dashboard display of the approach of fire apparatus and other vehicles, to prevent intersection collisions.
With the continued dedication of fire apparatus manufacturers, with the development of new technology, and with the commitment of fire service leaders in the United States and Canada, safety improvements are evolving continually. This evolution will offer significant improvements to apparatus and firefighter safety for years to come.Roll Cages in Fire Apparatus
Because of their high center of gravity, water weight in motion, speed and vehicle design, fire apparatus have a high propensity to roll over. Fire apparatus rollovers—and the lack of seat belt usage—have been a consistent source of line-of-duty deaths (LODDs) since LODDs first were recorded in 1977. Commercial fire apparatus cabs never have been built with the inherent roll cages that are built into custom apparatus cabs.
The Bureau of Land Management (BLM), which is an arm of the U.S. Department of the Interior, provides fire protection on federal lands in the wildland urban interface. The BLM recently bid a specification that requires the manufacturer that upfits the commercial chassis to build a roll cage within the cab of the commercial chassis. It certainly is hoped that the roll cage that’s upfitted in the commercial chassis for the BLM becomes the new normal for commercial cabs and will be replicated throughout the fire apparatus manufacturing sector.
Protection Against Cancer
The rate of and the variety of exotic cancers within the firefighting community is growing. Science confirmed that the soot that covers a firefighter’s bunker gear and equipment is laced with carcinogens. As a result, the fire service is adopting a strategy of clean side and dirty (contaminated) side, whether in stations or on board apparatus, to combat the cancer scourge.
Among the latest phrases in the apparatus industry is the Clean Cab concept. The idea is to keep cancer-ladened soot that accumulates on bunker gear and firefighting equipment out of the cab. Although no one actually defined what constitutes a clean cab, some manufacturers created storage areas in compartments that are outside of the cab to store and transport contaminated gear, including SCBA.
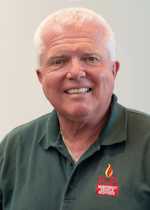
Michael Wilbur
MICHAEL WILBUR, who is a Firehouse contributing editor, retired as a lieutenant in FDNY, where he was last assigned to Ladder Company 27 in the Bronx. He has served on FDNY's Apparatus Purchasing Committee and consults on a variety of apparatus-related issues around the country. Wilbur is a member of the Firehouse Hall of Fame. For further information, access his website at www.emergencyvehicleresponse.com.