On Dec. 27, 1983, our nation suffered a tremendous tragic loss when five Buffalo, NY, firefighters were killed in the line of duty. These brave men answered their final alarm at the Chimera Radiator Co., located at North Division and Grosvenor streets. The cause of this disaster was an illegally stored propane cylinder inside of the building that would leak that day and become the fuel source for a major explosion.
Shortly after the devastating explosion, Firehouse® Magazine dispatched Harvey Eisner (assistant editor at the time of the event) to cover this very sad, but important story. Shortly after Eisner's return from Buffalo, he called me with a request to prepare an article to provide guidance to firefighters that would aid their response to gas leak situations. It was a personal honor then to share this information and it is an equal honor to prepare this updated version now. This article is dedicated to those incredibly brave Buffalo firefighters that gave the ultimate sacrifice to their community that day because of an illegally stored and used LPG cylinder. To those members and all of our brothers and sisters who have lost their lives in the line of duty protecting their communities, may God's perpetual light shine upon them all.
Situation Status
America's fire-rescue departments respond to hundreds of "gas leaks" each day. Because of the very nature and repetition, most departments let their guard down a bit. Although most departments would place a gas leak situation in a high-frequency/low-risk event, that is simply not correct. The risk of damage and injury is extremely high at all gas leaks. Sometimes, because of our familiarity with these types of alarms, they do breed contempt and we are complacent.
The stark reality is that a simple "gas leak" can turn horribly deadly very quickly. In fact, our history is dotted with incidents that have caused many lives to be lost (both civilians and firefighters) and millions of dollars of property have been lost as well. This article will once again (see Firehouse®, February 1984, pages 48-50) review the response to "gas leaks." Without a thorough understanding of the basics of the physical properties and operational practices, an effective and safer response is impossible.
Starting the Response
As with all alarms, the initial companies responding must obtain as much information about the incident as possible. First things first — make it a point to determine whether the response is for natural gas (methane); liquefied petroleum gas (typically propane and butane) or gasoline. Your dispatch center should have a protocol that clearly indicates that the "call-taker dispatcher" questions the person requesting help in a way that the product is identified with as much detail as possible. The goal should be that the dispatcher "paints the initial picture" with as many facts as possible from the beginning of the response. This mission-critical information (initial product identification) will set the stage for how companies respond and operate at "gas leak" events.
Over the years, I have attended calls that have been dispatched for a gas leak and have turned out to be gasoline that was spilled. The difference between the various products is expressed in different tactical operations that are dictated by very different vapor densities. This aspect of the physical properties of these chemicals will be discussed later.
Natural gas (methane; Ch4) is the most common utility gas. Typically, methane is distributed, stored and used in the gaseous state. It is highly flammable and much lighter than air with a vapor density of 0.6. In its original form, it is odorless, colorless and tasteless. For safety's sake, a powerful odorant is added to assist in detecting its presence. Usually, ethyl mercaptan (C2H5SH) is the pungent odor additive, and is said to smell like "garlic and onions." The natural gas service agency generally adds the odorant at the point of distribution. In practical terms, this means that a leak at a major transmission pipeline may (most likely will) carry the odorless product, compounding the problem.
In contrast, liquefied petroleum gas (LPG) is transported, stored and distributed in the liquid form, under pressure, and it is highly flammable. The gaseous propane and butane are compressed to change their physical state from gaseous to liquid, making storage and transportation easier and cheaper.
To liquefy the gases at 70 degrees Fahrenheit, the critical pressure for propane is 120 pounds per square inch gauge (psig); for butane it is 17 psig. This is the first major difference between the two families of gases (natural or LPG). Specifically, the LP gases possess a relatively high liquid to gas expansion ratio (propane 270:1; butane 230:1), while natural gas typically exists in the gaseous state (1:1).
The second major difference is the vapor density. Both of the LP gases are much heavier than air (propane 1.5, butane 2.0), which drastically changes the fire operations at an incident. LP gases are odorless, colorless and tasteless, and have ethyl mercaptan added to them.
Operations
In firefighting operations, two factors must be noted as soon as possible: the gas involved and the exact size of the leak. These two size-up factors probably will be the heaviest weighted factors in initial operations. Life safety of both the occupants and the firefighting forces is, of course, our first incident priority. Demand that the operating firefighters wear full protective clothing including self-contained breathing apparatus (SCBA). Rescue or extrication must be performed under the protection of a hoseline (air bleed off) supported by a dependable, adequate and continuous water supply. Move the affected people to a safe area, away from the gas cloud, as soon as possible. If the situation involves LPG, evacuation of a half-mile is not unreasonable. Don't overlook the bystanders; set up fire lines to protect them from the hazard zone.
Fire apparatus placement is one of the first mission-critical operational factors that must be considered. Extreme care must be used upon approach and a proper tactical placement of apparatus is a must. Remember, fire apparatus is an excellent ignition source as well as a very expensive exposure. Ideally, apparatus should be parked at least 500 feet away, on the upwind side, which means that you will be walking in from a distance, using an explosion meter to test the atmosphere distal to the leak.
LPG Tanks
When LPG tanks are involved in the incident, avoid the tank ends. The ends of the cylinders are thought to be the weakest because of the welds to the container and are most likely to fail. Apparatus as well as personnel should never enter a gas vapor cloud, for the danger is too great. If a victim is in a vapor cloud, disperse the cloud with a hoseline using fog spray, first, and then enter. Water supply is another factor to be considered when placing apparatus. If the gas leak is inside the building or involves an LPG cylinder, a reliable, continuous, uninterrupted water supply becomes a must.
If the gas leak is not burning, begin atmosphere monitoring, ignition source elimination, ventilation and leak control operations to resolve the problem. Proper gas detection equipment should be dispatched on the initial alarm to all gas leaks (perhaps the device is stored on a ladder truck or heavy rescue).
To briefly review the typical explosion meter operation, the meter indicates from 0 to 100% of the lower flammable limit of a particular gas to air mixture. In simple terms, when the average explosion meter reads 100%, the gas-air mixture has reached its lower flammable limit and is ready to ignite. Some meters will peg 100% and return downscale to indicate atmospheric concentrations above the lower flammable limit. Determine the vapor density of the gas involved, and use this information in both the detection and ventilation efforts. Thoroughly check and vent the areas (high — natural gas; or low — LPG) where the gas is expected to stratify as the priority area. Use and have an operational understanding of proper gas detection and air-monitoring equipment.
When to Ventilate
Ventilation will likely be required early into the alarm. Use explosion-proof equipment, making all electrical connections away from the gas leak in a fresh-air area. Use the circuit breaker at the generator or make the final electrical connections at the apparatus and avoid using on/off switches in a combustible atmosphere. If the explosive range has exceeded the upper flammable limit (too rich to burn) by ventilating, the mixture will pass through the entire explosive range. Proper precautions must be taken if this is the case. Eliminate ignition sources and have hoselines ready as a minimum.
Controlling the flow of gas can range from a simple to a complex operation. A proper selection of tools and leak plugs will be helpful. Departments should develop pre-plans for facilities that have extensive or unusual gas equipment. This information must be easily accessible and available for rapid fireground use. When you are ordered to shut down any type of gas service, make an earnest attempt to isolate the gas supply as close to the leak as possible. When this is accomplished, the leak will subside more quickly; an important factor, especially with LP gas products (remember the high expansion ratios). This step will avoid unnecessary disruptions of gas service to unaffected customers. For example, if a gas range is leaking in an apartment house, use the gas cock on the leaking appliance rather than the meter serving the entire apartment building. Generally, control of gas at street valves is performed by the local gas utility employees and not by the fire department.
BLEVE Concerns
In situations where the leak has ignited, deploy regular structural firefighting tactics. However, do not attempt to extinguish the burning gas as it may cause an explosion. Fully protect the exposures to the gas leak, and extinguish the gas leak by stopping the flow of gas. If the flames are impinging on an LPG cylinder, consider the BLEVE (boiling liquid expanding vapor explosion) potential. Some factors that can help evaluate the BLEVE potential are:
- Flame impingement on the vapor space of a cylinder. Without cooling water, this situation will stress the steel until failure occurs.
- Flame plume at the relief valve is intense or increases intensity. This valve opens at 250 psig, and the higher the internal pressure, the higher the flame plume will grow.
- Noise level at the relief valve is intense or increases intensity. Noise accompanies the flame plume for the same reasons.
- Change in tank color or shape. The metal of the cylinder can take on a white or red-hot appearance. Also, depressions in the tank shell may appear. When the cylinder shows this type of stress, failure will probably be imminent.
If any signs of a BLEVE present themselves, evacuate everyone using a minimum of a one half-mile radius. Establish incident command as soon as possible. Command must consider such factors as personnel, equipment, adequate and continuous water supply, evacuation and liaison with the local gas company. If the incident is large enough (three companies or more), command should consider establishing sectors.
Summary
The safe handling of a utility gas incident requires a blend of skills and knowledge before and during the incident. Consult your local or state training agencies and the local gas companies to provide realistic gas emergency drills and training programs. Review available case studies, which may be useful if a similar incident occurs in your jurisdiction. Finally, perform pre-fire surveys and use the data to better handle the actual incidents and to conduct in-station drills. Use all the resources possible to prepare and protect you and your members at gas leaks and related incidents.
DENNIS L. RUBIN, a Firehouse® contributing editor, is chief of the District of Columbia Fire and Emergency Medical Services Department. Previously, Rubin was chief of the Atlanta, GA, Fire and Rescue Department. He holds a bachelor of science degree in fire administration from the University of Maryland and an associate in applied science degree in fire science management from Northern Virginia Community College, and is enrolled in the Fire and Emergency Management Administration program at the graduate school of Oklahoma State University. Rubin is a graduate of the National Fire Academy's Executive Fire Officers Program, is a Certified Emergency Manager (CEM) and has obtained the Chief Fire Officer Designation (CFOD) from by the International Association of Fire Chiefs. He is an adjunct faculty member of the National Fire Academy since 1983. Rubin is the author of the book Rube's Rules for Survival.
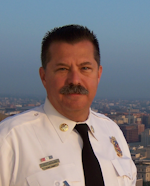
Dennis Rubin
Dennis L. Rubin is the interim fire chief for the Kansas City, KS, Fire Department. Rubin was the fire chief of the District of Columbia Fire and Emergency Medical Services Department and the Atlanta Fire Rescue Department. He holds a master’s degree from Waldorf University, a bachelor’s degree from the University of Maryland and an associate degree from Northern Virginia Community College. Rubin is a 1993 graduate of the National Fire Academy’s Executive Fire Officer Program and obtained the Chief Fire Officer and Chief Emergency Medical Services Officer designations from the Center for Public Safety Excellence. He is an adjunct faculty member at the National Fire Academy and the author of several fire service textbooks.