Tools & Technologies: The Evolution of Breathability in Turnout Gear
Research has always been a key component of change in the fire industry, with the primary goal of improving the safety and performance of firefighters. After new research is completed, the industry comes together to consider its impact, which frequently leads to updating the appropriate NFPA standards.
In the past 50 years, the evolution of protective barriers in turnout garments has had a significant impact on firefighter safety and performance at the fire scene (download graphic here). Originally, barriers were incorporated into turnout gear to prevent hot liquids from entering the gear, because these liquids reduced the thermal liner’s ability to protect against heat and burns. These barriers—made of rubber, such as Neoprene—did a good job of blocking the liquids. However, they also affected the firefighter’s ability to manage heat stress by preventing perspiration vapor from passing through the barriers. The result of adding these early barriers was better protection against liquids, but they significantly increased weight and heat stress.
Introduction of breathability
In the mid-1970s, the International Association of Fire Fighters (IAFF) began advocating for reduced heat stress from firefighter turnout gear. Working with several government agencies, the IAFF researched the evolving role of the firefighter and the gear being used in various emergency situations. The result of this endeavor was the 1983 Project FIRES report(1) that recommended lowering firefighter heat stress by replacing heavy, non-breathable barriers with lighter-weight barriers that were moisture-vapor breathable. Additionally, in the 1980s, multiple firefighter physiological field trials were conducted to compare the Neoprene moisture barrier to a GORE-TEX® moisture barrier. With varying degrees of impact, each of these studies reported that gear with the GORE-TEX® moisture barrier helped reduce firefighter heat stress when compared to gear with Neoprene moisture barriers. With the data from these reports and trials, the IAFF supported changing the industry standards to include minimum performance requirements of the turnout gear.
The first industry mention of breathability testing for turnout garments was in the Annex of the 1991 Edition of NFPA 1971: Standard on Protective Ensembles for Structural Fire Fighting and Proximity Fire Fighting. The Annex included the Total Heat Loss (THL) test, which measures the total amount of heat transferred through turnout composites (i.e., outer shell, moisture barrier and thermal liner) in a controlled environment of 77 degrees F and 65 percent relative humidity. The total heat transfer measurement combines both conductive heat transfer and evaporative heat transfer (i.e., breathability). However, this original reference to the THL test method was removed in 1997 when the NFPA Technical Correlating Committee voted to remove any test methods contained only in the appendices of its Standards.
At that time, a few studies were evaluating the physiological effects of turnout gear on firefighters. In one particular study, the IAFF and the Indianapolis Fire Department collaborated with W. L. Gore & Associates (Gore) and E. I. DuPont de Nemours (DuPont) to correlate and validate the predictive capability of the THL test methodology against the physiological responses of firefighters in simulated fireground activities. Based on the positive results of this study, the firefighter community again lobbied for the THL test to be incorporated as a minimum performance requirement into the next edition of the NFPA 1971 Standard. Seventeen years after the first reports about heat stress were published, this research and testing methodology became an integral part of the Standard’s 2000 Edition.
Further recognition of the improved physiological effects of breathable turnout gear led to increasing the minimum performance value for THL in the 2007 Edition of NFPA 1971, and that minimum value remains the same today. And throughout the 1990s and 2000s, several types of breathable barriers were offered in the industry.
Combining breathability with protection and durability
In 1991, the Occupational Safety & Health Administration (OSHA) began requiring employers to provide protection against blood-borne pathogens for their employees. To comply with this OSHA requirement, the medical fabrics industry developed a new test method for evaluating barriers against penetration of blood and body fluids, which ultimately became an approved ASTM test method(2). The fire industry added this test method to the 1997 edition of NFPA 1971 along with a moisture barrier test for common chemical liquid penetration resistance.
Also in the early 1990s, durability and care of turnout gear started to become a focus of the industry. As an independent organization, the Fire Industry Equipment Research Organization (F.I.E.R.O.) committee began developing guidelines for use by individual firefighters, fire departments, and turnout gear PPE manufacturers. In 1994, it published PPE Care and Use Guidelines, which became the basis for the first edition of NFPA 1851: Standard on Selection, Care, and Maintenance of Protective Ensembles for Structural Fire Fighting and Proximity Fire Fighting seven years later. Overall, the increased industry focus on durability and care of turnout gear led to the introduction of several new moisture barriers that provided added durability while maintaining high breathability.
In the early 2010s, a significant realization occurred regarding the THL test method. Although this test was a great addition to the Standard when it was first introduced, more recent industry research has shown that the THL test does not go far enough in representing real-world conditions in which firefighters operate. Research in moisture barrier and turnout gear performance began focusing on testing in conditions that simulated a broader range of fireground environments rather than just those used in the THL test method (i.e., 77 degrees F and 65 percent RH). Results showed that two identical composites that perform equally in THL conditions can have very different breathability levels in warmer conditions or in conditions with low-level radiant heat (e.g., heat from the sun, a hot roadway, or a tar roof that needs to be vented).
The future of turnout gear composites
The industry knows that water in turnout gear can compromise thermal protection, and recent research on the performance of turnout gear in sub-flashover conditions has proven this. Testing has shown that thermal protection of wet gear often decreased when compared to protection provided by the same gear when dry, with some composites losing as much as 34 percent of its thermal protection.
Selecting turnout gear composites has traditionally required a trade-off between thermal protection and breathability. Increasing one typically means sacrificing some aspect of the other. The direction for new technology in turnout composites is to address both breathability in broader conditions and enhanced thermal protection—gear that doesn’t compromise one for the other.
Conclusion
Through research and the guidance of the NFPA Standards, the role of the moisture barrier has evolved from a non-breathable barrier that blocked hot liquids to a breathable barrier that significantly reduces heat stress and protects against blood, body fluids, common chemicals and water. In fact, the latest advancements have resulted in systems that provide even higher breathability while improving thermal protection.
Studies of the physiological impact of turnout gear will continue to advance technology for firefighters. Research is an ongoing process and can eventually lead to changes in performance standards for breathability and thermal protection.
References
1. Project Fires Report. http://www.cdc.gov/niosh/npptl/pdfs/ProjectHEROES.pdf
2. ASTM F1671 – Standard Test Method for Resistance of Materials Used in Protective Clothing to Penetration by Blood-Borne Pathogens Using Phi-X174 Bacteriophage Penetration as a Test System
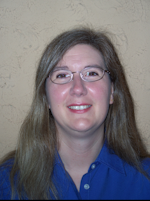
Holly Blake
Holly Blake is a product manager with W. L. Gore & Associates. For approximately years, Holly has focused on developing new technologies for the fire industry, with primary responsibility for CROSSTECH® moisture barriers and the GORE® PARALLON™ liner system. She also works with other research teams on breathable technologies for the fire industry — the most recent being the new GORE® Particulate Hood. Holly holds a Bachelor of Science degree in chemical engineering from Lehigh University. For information about Gore’s products, visit GoreProtectiveFabrics.com.