Any time an air-bag lift is performed, cribbing is a necessary part of the operation. Cribbing is a temporary framework, usually constructed of timbers, that provides a solid base of support to material above. This framework provides the means to support the object being lifted as well as the air bags themselves. It is essential for members to crib properly in order to ensure that the load does not shift and potentially fall on the victims or rescuers.
Cribbing Types
Cribbing comes in a variety of shapes, sizes, and materials. The most common material is wood, however there is composite cribbing available on the market. Common timber sizes used are 2-inch x 4-inch, 4-inch x 4-inch, and 6-inch x 6-inch (see Photo 1). The timbers can be cut to various lengths, but departments should try to standardize the cribbing length to ensure compatabilty when building crib stacks. A good standard length is 24 inches, which provides a good stable base.
In addition to straight timbers wedges should be available at incidents. Wedges allow members to ensure there is little to no movement during operations when larger timbers cannot be placed due to space constriants. Like straight timbers, wedges should be cut to standard lengths and degrees to ensure compatability.
Step chocks are another convenient form of cribbing for incidents requiring stabilization. Step chocks are constructed of 2-inch x 6-inch cut to varying lengths forming steps (see Photo 2). Step chocks are especially useful to quickly crib a vehicle.
Box Cribs
Box cribs are the most common type of cribbing system used in air-bag operations. Box cribs are constructed of a series of timbers placed perpendicular to one another to support a load (see Photo 3). Box cribs are not just used to support and stabilize the load being lifted, but the air bags themselves.
Box cribs are typically constructed using 4-inch x 4-inch timbers, but 6-inch x 6-inch timbers can be used to support heavier loads. Each layer, or tier, is placed perpendicular to each other until the desired height is reached or the system becomes unstable. The weight of the load to be supported will determine if there will be two timbers per tier, or three timbers per tier (see Photo 4).
Wood Types and Load Capacities
The capacity of any cribbing system greatly depends on the type of wood and size of the timbers used. Wood can be divided into two broad categories – hardwoods and softwoods. Hardwoods come from deciduous trees, whereas softwoods come from coniferous trees. Softwood is sort of a misnomer as the wood itself is very hard and capable of supporting heavy loads.
The most common types of structural timber used in the United States are Douglas Fir or Southern Pine, both of which are softwoods. Softwoods are ideal for cribbing because the object being stabilized bites into the surface of the timber, thus minimizing movement. Softwoods are desirable for unknown weight-load situations because they provide warning signs of failure. They tend to fail by cracking and splitting slowly, and this produces a loud crushing noise.
In order to calculate the weight capacity of the cribbing system, we need to know the timber size being used, the type of wood used, and the number of timbers per tier. Timbers purchased from a lumber yard have a nominal size and a dimensional size. The nominal size, such a 4 inches x 4 inches, is the label applied to indicate the size of the green lumber when it was initially sawn. The dimensional size is the actual size of the timber once it is cut to size, planed, and dried. For example that same 4 inches x4 inches is now truly a 3.5 inches x 3.5 inches (see Photo 5). It is critical that we use the actual dimensions of the timber for our calculations.
Weight capacity of cribbing is based on perpendicular to grain loading of the system. The perpendicular loading capacity depends on the type of wood being used and can range from 200 pounds per square inch (PSI) to 1000 PSI. The commonly accepted value for Douglas Fir or Southern Pine is 500 PSI, which is what we will use for our calculations.
The final variable we need for our calculations is the number of timbers per tier. The more timbers, the more points of contact the system has. For example a two per tier system has four points of contact (see photo 3).
Cribbing Capacity Formula:
PSI of Timber’s Perpendicular Load Capacity x Timber Dimension x Timber Dimension x Number of Points of Contact = Crib System’s Capacity in pounds (LBS)
Cribbing Capacity Math – Example 1:
4-inch x 4-inch being used for the system – Realizing true dimensions of 3.5-inch x 3.5-inch
Douglas Fir is the wood being used – 500 PSI perpendicular load capacity
Two timbers per tier construction – 4 points of contact
500 PSI x 3.5 inches x 3.5 inches x 4 Points of Contact = 24,500 pounds, rounded down to 24,000 pounds (12 tons)
Cribbing Capacity Math – Example 2:
Same variables as Example 1, but using three timbers per tier construction – 9 points of contact
500 PSI x 3.5 inches x 3.5 inches x 9 Points of Contact = 55,125 pounds, rounded down to 55,000 pounds (27.5 tons)
Commonly Accepted Capacities – Using 500 PSI Perpendicular Load Capacity:
Timber Size |
Timbers per Tier – Points of Contact |
Capacity in LBS |
4” x 4” |
2 per tier – 4 points of contact |
24,000 LBS (12 tons) |
4” x 4” |
3 per tier – 9 points of contact |
55,000 LBS (27.5 tons) |
6” x 6” |
2 per tier – 4 points of contact |
60,000 LBS (30 tons) |
6” x 6” |
3 per tier – 9 points of contact |
136,000 LBS (68 tons) |
It is critical to understand that these capacities are based on weight of the load being distributed across all points of contact on the system. The capacity of the system is reduced if the load is placed between the points of contact.
Conclusion
Cribbing is a vital part of any safe air-bag operation. It is essential for members to understand the capacity of cribbing systems. Without the proper crib system in place, the object being lifted could shift or fall and crush the victim or members. Much more on the use of cribbing will be discussed in the next article.
For the full series of Air Bag Operations
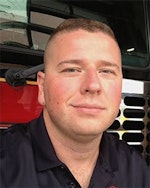
Jonathan Hall
Jonathan Hall, who is a Firehouse contributing editor, has more than 24 years of fire service experience. He currently is a captain with the St. Paul, MN, Fire Department assigned to Engine Company 14. Hall also serves as a lead instructor in the department's Training Division; he teaches hands-on skills to members of all ranks. Hall is the co-owner of Make The Move Training LLC and teaches engine company operations throughout the country.