West Coast Type 3 Design, Layout & Safety
One of the most exciting things for a fire chief has to be replacing or building a fleet of apparatus. Years ago, one of my mentors and a great fire chief, Ray Picard of the Huntington Beach, CA, Fire Department, told me that besides color, “A fire chief’s only input into apparatus design should be the budget limit.” However, a good fire chief must choose the right people—the apparatus committee—to pass that budget to. I have been on numerous apparatus committees. Some were good, and some were very, very bad.
In 2021, my agency needed a new Type 3 fire apparatus. I knew that the decision that the committee and, ultimately, I made would affect our agency for a minimum of 10–15 years. Further, our decisions would affect the overall effectiveness of the crews that responded to urban wildland incidents and their overall safety while they engaged in firefighting operations. As fire chief, you have no greater mission than to ensure that your personnel are safe and that they have the tools to do their job effectively. We all struggle with budgets, but it’s the fire chief’s job to find the appropriate amount of funding to ensure that those needs are met.
The wildland apparatus committee
As our aging Type 3 apparatus, or what’s commonly referred to as a brush engine, neared the end of its service life, a group of personnel was assembled to build a new Type 3 apparatus.
I assigned a senior fire captain to chair the committee. The choice was obvious, because he led our wildland division; had 31 years of experience, including with a strong emphasis on the wildland (part of a Type 1 incident management team); and was one of the foremost sought-after safety officers in the state of California.
To round out the committee, two engineers, a firefighter/paramedic and a firefighter/EMT were assigned.
All of the personnel had been on numerous wildland incidents, assigned to either a Type 3 initial attack incident, a Type 3 strike team/task force or a single role working with Type 3 apparatus. The depth of knowledge would provide sufficient input to design a solid apparatus.
All personnel had an equal vote, with the committee chair providing any tiebreaker vote should it be required.
We all have seen agencies try to reinvent the wheel or put their own spin on apparatus design, only to find that they ended up with a huge albatross that they had to deal with for decades.
In my career, I have seen three agencies purchase truck companies that were too big to fit into their fire station, because the committee didn’t think things through when it designed the apparatus. One agency had to sell the apparatus at a loss of funds—not to mention of credibility—and the other two had to perform station modifications that cost tens of thousands of dollars.
I always have found that when there’s something that works, go with the known, because the unknown likely will bite you in the butt. So, when it was time for us to design and spec the Type 3 apparatus, we took a page out of the book of commonsense. This included reaching out to our partners at CAL FIRE to ask them for their thoughts and ideas on new Type 3 apparatus. CAL FIRE does things very well when it comes to design and application of Type 3 apparatus. A big plus is their capability to service those apparatus up and down the state at a moment’s notice.
In addition, previously, we found success in cooperation with the Los Angeles City Fire Department on the replacement of our engines, truck and rescue ambulances. So, gaining perspective and input from those two agencies, what with their large fleets and some of the best fleet mechanics in the business, we sought to alleviate future problems.The core of Type 3s
When it came down to the nuts and bolts of design, the factors that are noted below played into our journey. By in large, these factors are common throughout the West Coast, particularly in California, for most all fire agencies that operate Type 3 apparatus, although each agency will have modifications or changes.
Of course, Type 3 apparatus typically are used in the wildland setting, but, more and more, they also are used in urban settings where homes—increasingly more—are in areas that have large vegetation growth, such as hillsides and canyons, that can create an urban wildland fire.
Type 3 apparatus commonly sit on a commercial 4x4 chassis because of the need to climb steep rocky terrain and to provide off-road capabilities when they are assigned to strike teams. Nevertheless, they are maneuverable.
Type 3 rigs must be able to get as close to the fire as possible or into areas for structure defense while maintaining stability, vehicle control and the capability to engage in firefighting operations.
Typically, GVWR is more than 26,000 lbs., and the vehicle must be equipped to carry at least three passengers (ideally, four).
NFPA standards require a Type 3 engine to have a minimum of a 500-gallon water tank and a pump that’s capable of a minimum of 150 gallons per minute at a pressure of 250 psi.
Type 3 apparatus usually are equipped with a power take-off (PTO) pump so that the vehicle can deliver pump-and-roll capability: The engineer drives the vehicle while firefighters operate hoselines outside of the vehicle and the fire captain supervises for safety and looks to extinguish fires while moving along a flank or roadway.
Our Type 3 apparatus and most all that we know of also feature an auxiliary pump. It can be powered by a separate diesel engine that’s connected to the pump or by an additional PTO hydraulic circuit that has its own pressure governor.
Storage
Because Type 3 apparatus also operate in an “all-risk” capacity, maximizing storage is key.
All four positions on the rig must have an SCBA and spare bottle.
In the state of California, most Type 3 responses include at least one firefighter/paramedic, which necessitates the need for a complete or, at minimum, a line-paramedic cache to utilize in the event of an ALS emergency.
Operating a Type 3 apparatus—and being part of the California State Master Mutual Aid Program—usually means that personnel and apparatus will be assigned out of city, district or area for 14–21 days multiple times per year. Personnel will take a host of items with them to operate for a minimum of 72 hours without support. Therefore, we ensured that there’s space for all structural PPE, out-of-county bags, an ice chest, hygiene kits, MREs, tents, sleeping bags and cots. This is in addition to all of the wildland equipment, hose and tools that are required by California’s Office of Emergency Services.
Safety and comfort
Safety is a huge concern. Most Type 3 rigs include technology to prevent extreme damage in the event of a rollover accident. Also, most manufacturers produce apparatus that have enhanced safety features: cabs that provide enhanced protection; rear- and side-mounted cameras for the engineer; rollover indicator alarms; and enhanced seat belts.
We also must include all of the creature comforts in the apparatus. This might sound silly, but it’s critical to address comfort for personnel to operate effectively over extended deployment. We want all personnel to have air-ride seats, moderate capability to recline seats, USB ports, a solid and well-working climate control system, roominess in the cab and even Wi-Fi capability.
Small investment, great significance
With more and more homes and developments encroaching into the wildland, the need for more and more Type 3 apparatus will become the norm in fire departments across the nation.
In our agency, it isn’t uncommon for personnel to be assigned to a fire or series of fires up and down the state for 21 consecutive days, only to return and be reassigned withing 48–96 hours to another 21-day deployment.
Their ability to safely and effectively do their job protecting the people, property and environment requires a safe operating platform. So, when my department’s apparatus committee asks for items such as those that are noted above, I listen. Those might be little expenses in the overall budget, but they pay huge dividends when personnel are away from their family and the agency for extended time frames.
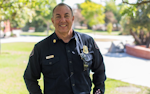
Edward Hadfield
Edward Hadfield recently served as the fire chief and fire coordinator for the Weatherford College Fire Academy in Weatherford, TX. He previously served as the fire chief for the Rincon Fire Department in San Diego. Hadfield is a 38-year veteran of the fire service in southern California. He established regional fire command programs, mentoring models, and health and safety programs. As a researcher, Hadfield collaborated with Underwriters Laboratories and NIST on studies that advanced firefighting tactics, safety protocols and building code developments.