Designing Your Pumper Fleet to Meet the Mission
Most fire departments, regardless of size and demographics, operate and staff at least one engine company. The response district partly dictates the operational needs for apparatus. Rural departments rely on tankers, tenders or static water supplies to develop adequate fire flows for structural fires. Suburban communities, which are protected by fire hydrants, can develop different tactics to support water supply on the fireground, with the first-due pumper responsible for laying a supply line to establish water supply.
Many departments develop a mission statement to focus the organizations goals. It might read something like this: “To professionally provide and enhance life safety and fire protection services in a safe and respectful manner for all community partners.” From this statement, anyone who is in the organization can understand how the department desires to conduct business to meet the mission. When it comes to fire apparatus and fleet replacement policies, what’s the mission of the department’s engine company vehicles?
One of the operational benchmarks for the first-due engine company should be to rapidly develop a reliable water supply and to stretch an appropriate size attack line to protect life safety and to initiate fire control and extinguishment. The late Andy Fredericks, who lectured nationally on engine company operations, stated, “The prompt control and extinguishment of a serious fire is the single most effective lifesaving action a fire department can perform.”
With this in mind, every pumper should be set up to meet this mission with sufficient hose, tools and appliances to develop the target fire flows, ranging from a single attack line in the 150–180-gpm range to master streams of 700–1,000 gpm. How this is accomplished is a combination of apparatus design, adequate staffing and training. All three of these components are essential, because a well-designed pumper can’t make up for an understaffed company.
Replacement components & inspection
Keeping front-line pumpers in service depends on several factors. These include having some degree of standardization with respect to major components, such as drivetrain, fire pump and valves, running and warning systems, cab seating and body configuration. Maintaining a stock of replacement components enables front-line pumpers to remain in service. Additionally, standardized pumper designs and hose loads enable personnel to safely operate on the units regardless of station assignments.
Managing an apparatus fleet to maintain operational readiness for all vehicles starts with personnel conducting a daily pre-trip inspection on the apparatus to confirm the rigs’ capability to perform their mission safely. Generally, this inspection is conducted by the driver/engineer who’s responsible for operating the apparatus for the duration of the shift.
Reviewing the major components, both inside of the cab and under the vehicle, including all fluid levels, running and warning lighting, and tire pressures (with a gauge), is mandatory to confirm that all systems are operating properly in conformance with the manufacturer’s recommendations. Nonfunctional components or damaged equipment should be noted following the department’s guidelines along with NFPA 1910: Standard for the Inspection, Maintenance, Refurbishment, Testing, and Retirement of In-Service Emergency Vehicles and Marine Firefighting Vessels, to ensure the safe operation of the apparatus.
Apparatus committee
Critical to the success of designing rigs to meet the department’s mission is the formation of the apparatus committee. The expression “too many cooks spoil the broth” is appropriate with respect to the number of personnel who serve on the apparatus committee. The committee should consist of no more than four or five personnel who represent a cross section of department members and should, at minimum, include company officers, drivers/engineers who will operate the vehicle, department fleet maintenance personnel and at least one member who has experience participating in the apparatus procurement process.
Department staffing should influence the size of the cab, the required seating arrangement and how much equipment must be secured inside of the cab, at times depending on whether the unit operates at a BLS or ALS level.
If the department developed operational requirements for standard chassis components, tool and equipment layouts, and hose deployment practices, these must be included in the overall pumper design.
All of this input can assist the apparatus committee to develop specifications that enable the pumper to meet the department’s mission while addressing concerns that will enhance the in-service time and reducing unwanted mechanical repairs.
Standardization
A standard platform for pumper design creates a benchmark for the minimum requirements, to enable the rig to work seamlessly within the department. An example of this style of apparatus is working with the Prince William County, VA, Fire & Rescue System. The department operates from 22 stations that are staffed by both career and volunteer personnel from the eight volunteer corporations. It responds to more than 53,000 incidents annually.
The department’s apparatus and equipment committee developed a 24-page document that’s titled “Pumper Fire Apparatus Standards & Equipment Requirements.” The document covers all aspects of the pumper design, including minimum vehicle dimensions, cab seating, chassis safety systems, in-cab camera, pump piping for intakes and discharges, body and hosebed configuration, and the equipment complement for each vehicle.
Historically, each of the volunteer departments acquired apparatus based on its operations, with rigs acquired from its preferred manufacturer. For example, some stations utilized crosslay hosebeds, while others ran all attack lines from the rear hosebed. The county standards allowed for each organization to acquire new vehicles from whichever manufacturer that it preferred while meeting the operational standard as a minimum benchmark.
As the department opened new stations that would be staffed by career personnel, new apparatus was ordered to provide units for these facilities. The result was apparatus being acquired from several manufacturers, including KME, Pierce Manufacturing and Seagrave, using a standardized pump module. Because of differences in cab lengths of these rigs, the wheelbase ranged from 183–194½ inches combined with a body length of 152–155 inches.
After several years of operation of these pumpers, certain components were reviewed to evaluate their use at incidents and their effect on the operational cost of having this equipment on the rig. The standard initially required an electronic foam system with dual 40-gallon foam cells along with a hydraulic generator and single electric cable reel. With enhancements that have come in the realm of scene lighting technology and battery-powered ventilation fans, newer pumpers no longer require these components. The use of Class A and Class B foam agents was reviewed. As a result, the newer vehicles no longer have this system, with the county having a dedicated foam engine on order that will serve the entire response area.
Pump panels
For departments that work on new pumpers, the number of intakes and discharges and the make and model of fire pump all affect the width of the pump panel, which drives the vehicle wheelbase and overall length. The pump piping and valve size for attack lines should be determined based on the department’s desired gpm target flows for both small- and large-caliber streams. When properly designed, these target flows can be confirmed during the final inspection or delivery training based on the hose and nozzle appliances that are used by the organization.
A review of pump panel layouts differs greatly from manufacturer to manufacturer. Therefore, this area should be scrutinized carefully at preconstruction meetings to make sure that all of the panel components, most of which are purchased by the builder, are located properly for ease of operation on the fireground as well as providing easy access for the fleet maintenance personnel to conduct routine repairs, including access from the right side and front of the pump module.
Optimal fireground operations
Developing a pumper to meet the department’s operational requirements with respect to vehicle dimensions (e.g., safe step access to the cab and rear body, low hosebed layouts that don’t require personnel to climb on the vehicle to advance attack lines, and standardized tool and equipment locations) can affect fireground operations positively. The adage “As the first line goes, so goes the fire” should help to keep the apparatus committee on task when developing the requirements for its next pumper.
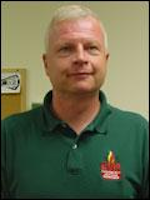
Tom Shand
TOM SHAND, who is a Firehouse contributing editor, is a 36-year veteran of the fire service. He works with Michael Wilbur at Emergency Vehicle Response, consulting on a variety of fire apparatus and fire department master-planning issues. Shand is a member of the Firehouse Hall of Fame.
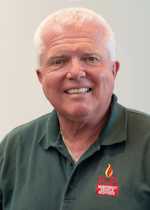
Michael Wilbur
MICHAEL WILBUR, who is a Firehouse contributing editor, retired as a lieutenant in FDNY, where he was last assigned to Ladder Company 27 in the Bronx. He has served on FDNY's Apparatus Purchasing Committee and consults on a variety of apparatus-related issues around the country. Wilbur is a member of the Firehouse Hall of Fame. For further information, access his website at www.emergencyvehicleresponse.com.