Firefighter Training Facilities: Members Deserve the Best
In May 2023, the Bentonville, AR, Fire Department (BFD) had a ribbon cutting for its new training facility. It provides training that members weren’t able to get unless they went elsewhere, which necessitated all of the procedures that are required for taking a company, etc., out of operation. Yes, a stair tower that’s attached to one of the department’s stations facilitates training in stairwells and on standpipe systems, but the tower isn’t fire-rated, and even the stairwell’s use provides only limited experience compared with the variety of stairwells that BFD firefighters encounter throughout the response district.
The new facility includes 12 burn rooms (10 of which are Class B); two hallways that are equipped to produce rollover, one of which leads to a bedroom fire prop; a balcony prop that includes a barbecue grill; and a fire-extension prop. Multiple stairwells of varying widths also are included in the facility’s design.
“We’ve had the building for nearly two years, and we haven’t even scratched the surface on all of the options for setting a fire in the building and various scenarios,” Fire Chief Justin Scantlin tells Firehouse.
Unsurprisingly, the evolution of the BFD’s training circumstance mirrors that of myriad departments. Although many might not be capable of procuring $3.9 million to build a fixed facility, as the BFD was, the good news is that the training facility and prop options and the scenarios that can be provided never have been more accessible or sophisticated.
More evolutions
Scantlin explains that his department’s desire for realism in the training environment was such a matter of focus that it specified the addition of a sound-generation system in several of the Class B burn rooms. Simulated Class A fire noise, commercial building alarms, a baby’s cry, a man coughing, a cat’s meow, screams and breaking glass are among 40 sounds that can be activated in different burn rooms.
“The ability to change up sounds and scenarios was paramount to keep things fresh in their training,” Pete Romero of Symtech notes.
Romero's company provided the sound-generation system. Its programmability provides the capability to add new sounds periodically.
“The system can be toggled between props mode and manual mode,” Romero explains, “where sounds occur automatically with initiation of selected fire or manually from a wireless remote.”
Symtech’s participation in the development of the BFD’s facility, which included aspects beyond the sound system, ties in with the former’s partnership with Fire Facilities, which spearheaded the project.
“A lot of departments are trending to cleaner-burning fuels, and Symtech has some excellent propane props that fit seamlessly with our burn room system,” Fire Facilities General Manager Zach Willard says. “We want the gas props in a controlled environment that can withstand heat, not just your typical wall panels, and that provide an excellent product that’s environmentally friendly.”
This means that training buildings or mobile training units can be located in residential areas instead of requiring a city to dedicate acres of land that’s blocked off or to go through the difficult assignment of setting up all that’s required for Class A burns at acquired structures.
“We used to get structures to burn,” Pete Webb, who is deputy chief of training for the Dothan, AL, Fire Department (DFD), tells Firehouse, “but that’s a lengthy process.”
As surely many departments can relate to, the DFD spent significantly more time in dotting the i’s and crossing the t’s for a live fire training at an acquired structure than the training time itself.
“We also knew that we had more things that we had to train for [than what’s provided via acquired structures],” Webb states. He also explains that the department wanted to save money and travel.
Although the department had a single four-story training tower, training in it couldn’t include Class A live fire, because, basically, it was a simple cinder block structure.
Furthermore, “The site of the tower was next to a recreational field, so it could be an eyesore,” Webb notes.
The DFD’s new facility, which is part of a regional training center for fire protection and law enforcement, includes Class A burn areas but a Class B building, too. The beauty of the latter, with its propane props (kitchen fire simulator, bedroom simulator, warehouse simulator with flashover, among others), is, of course, the nearly complete elimination of products of combustion. However, the capability to reset scenarios more quickly than what’s possible with Class A live fire training provides the means to facilitate many more repetitions than what’s possible with Class A training.
Gas props were supplied by Fireblast Global. Among the most recent elements of the company’s offerings is a new pilot system that has a more efficient ignition system than what was previously available. Hand in hand with that is a facilitation of easier servicing.
“Our Quick Burner is able to be removed within a couple of minutes without any tools,” the company’s CEO, Rick Egelin, shares. This eliminates the cost that a department otherwise would have to pay to have a field technician fly in and work on the system. Department personnel can remove the burner themselves and send it to Fireblast. Furthermore, in such a circumstance, the system is out of service for a shorter amount of time.
Maintenance
Ease of maintenance and cost reduction that’s associated with it are matters that numerous departments and firefighter training equipment/facility specialists raised when we spoke with them.
“A lot of the things that we do in both our fixed structures and our modular structures is to reduce the maintenance,” Joe Kirchner, who is chief operating officer of WHP Trainingtowers, tells Firehouse.
A case in point is the company’s development of its Padgenite Interlock.
“Our thermal lining system can withstand repeated training fires to protect structural members from damage,” Kirchner explains. “Interlocking tiles expand and contract during rapid heating and cooling cycles, so facility operators are going to see less cracks and less damage.”
Among reasons why this is important, Kirchner says, is the increasing use of smoothbore nozzles to shoot water against ceilings to let water rain down on fire.
“Padgenite Interlock was introduced to help support that type of training,” he adds.
Despite this innovation and others that developers of fixed facilities and mobile facilities and prop manufacturers have created, departments and their training divisions can put themselves in a predicament if they don’t consider maintenance from the get-go.
“If they treat their facilities and equipment like they treat their fire engines, [the facilities] always will perform at a high level and safely,” Egelin offers.
Although the BFD is highly complimentary of the customer service that Symtech provides on its propane props, the department recently added a fiber-optic network in its training facility.
“Now, Symtech’s engineers can troubleshoot their equipment remotely,” Scantlin says.
Webb offers that a big lesson learned for him and his department was failure not to program maintenance—even the most rudimentary—into the budget. “We should have identified on the front end maintenance costs.”
He believes that it’s natural for everyone to be excited to get this “Christmas gift” and for that excitement to distract them from considering what it will take and how much it will cost to keep it operating.
“You don’t want to miss that, because, if for some reason, the department runs into a financial downfall, you might lose your burn building until funding is found.”
Cost
Undoubtedly, training facility maintenance best practices correlate with the cost of operating a training facility, whether fixed or mobile. However, front-end matters are more consequential.
Surely, off-the-shelf solutions certainly can suit the needs of a department, but Randy Lammons, who is deputy chief-supplied services for Lubbock, TX, Fire Rescue (LFR), urges departments that are embarking on new or additional acquisitions to think beyond those.
“A lot of people want to sell you their product even if it doesn’t match your needs,” Lammons contends. “That’s one of the biggest things that WHP Trainingtowers allowed us to do: a stair-step design, by which we can grow and add as we see fit to better represent our community. It isn’t just a ‘box’ to light fire in.”
“The reality is that training systems across the country vary greatly depending on the resources available,” Dräger Fire Training Systems’ Paul Tarter adds. “Smaller departments often face challenges in securing funding for comprehensive setups.”
Tarter points out that NFPA 1403: Standard on Live Fire Training Evolutions now requires structural engineering approval for fire training systems.
“This approval can increase the cost of a system by more than $20,000 due to the need for state-regulated engineering stamps,” he explains. “We engineer our systems with detailed tolerances and lifecycle maintenance to meet these high standards.”
In the world of mobile props, ones that provide flexibility in training scenarios can be of major significance when it comes to cost. Recently, FDNY faced a limited budget for its new training facility in Staten Island. After meeting with the department to determine its most common fire scenarios, Symtech produced a multiburner stove prop with overhead kitchen cabinet extension and a prop that delivers bed, clothes dryer and boiler/water heater scenarios.
“The department only had a budget for two of our gas prop systems,” Symtech’s Romero says. By applying value engineering, “We came up with an interchangeable design so that they could have four different scenarios really for the cost of two.”
Although the core of Taylor’d Systems’ Series 12 provides 10 scenarios, the design is such that five more scenarios can be accommodated easily and inexpensively.
“Departments are starting to put our prop up against shipping containers, and they can stack containers and make entry ways to do search and rescue, which can result in a much more cost-effective price,” Taylor Rowan, who is president of Taylor’d Systems, states.
The cost discussion of training facilities isn’t complete without covering funding sources. Certainly, a main path is via the municipality or county, and with that comes the requirement to convince citizens of the necessity to advance their firefighters’ skill and acumen.
“With our trailers, we’ve seen some cool events where the cities, counties, whoever owns the trailer, bring a trailer to a parking lot, for example, to showcase the trailer and its benefits and even to educate on fire prevention,” Willard states, “because the first step is community buy-in.”
LFR’s Lammons tells Firehouse that his department was fortunate that a substantial portion of the funds that were provided through the American Rescue Plan Act were earmarked for public safety, and those who were involved in the construction of the department’s new training facility were able to tap into that.
A particularly intriguing instance of acquiring funding lies in the case of the DFD’s project. The fire chief and the chief of the Dothan Police Department had been considering options to upgrade training for their respective members. Word of this reached folks at Wiregrass Foundation, which provides grants to nonprofit community organizations that are located throughout the Wiregrass region of southeast Alabama. What ensued was a meeting between the two chiefs and a Wiregrass Foundation representative.
“It all started with writing some wish-list items on a cocktail napkin,” Webb recounts.
The two chiefs were conservative in listing what they sought, not wanting to overstep their request bounds. The Wiregrass Foundation representative’s response amazed and delighted them.
“‘We know your departments take care of a lot of the citizens of our communities,’” Webb paraphrases. “‘We want to enhance public safety.’”
The Wiregrass representative told the two chiefs to expand their thinking.
Webb believes that the initial circumstances of the conceptualization of the training facility, which officially is dubbed the Wiregrass Public Safety Center, should serve as food for thought for departments.
“Department fire chiefs must get out there to see what other funding opportunities might be possible,” Webb urges.
Flexibility
As noted above, training scenario flexibility can be immensely important, as long as a dedication to realism is included.
“These days, different communities have different styles of sloped roofs or multiple pitches. Being able to train on all of those different pitches and different roof materials is important,” Kirchner says. “A lot of the training props that we’ve been doing specific to roof ventilation training have been going to ones that are adjustable.”
The BFD’s training facility includes a garage burn room, to provide the opportunity to train on garage vehicle fires, garage content fires, flammable liquids fires, loading bay scenarios and industrial rack fires, among others. An SUV prop that Symtech introduced a couple of years ago also is included.
“The sides of an SUV typically are higher than the sides of a passenger car, so it’s more difficult for members to get their hands in the window. The angles are different,” Scantlin explains.
Fire Facilities’ Willard tells of how his company developed a 22-burn room trailer for the Fort Worth, TX, Fire Department for fire investigation training.
“There are different items in there for [students] to pick up on, whether it’s a circuit breaker fire, an electrical fire or power sources for different equipment failures,” he says. “This provides the opportunity to figure out where the fire originated, what do the smoke patterns indicate, where was the fire hottest and so forth.”
Realism was the basis for Fireblast Global’s development of new stainless steel burn pans in its new burner system into which water is injected to create humidity in the Class B room.
“It makes the training environment feel a lot warmer without the room temperature being accelerated,” Egelin states. This also falls in line with the company’s commitment to design training buildings to minimize the health risk to those who are going through training evolutions.
BFD’s Scantlin says, “The more real that we can make training, that’s one less thing to throw somebody off on the fireground.” To a person, all of the other eight experts who Firehouse sought out agree.
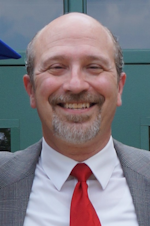
Rich Dzierwa | Managing Editor, Firehouse Magazine
Rich Dzierwa joined Firehouse Magazine in 2019 after four tenures with other publications. He was editor-in-chief of Consumers Digest/ConsumersDigest.com and of trade magazine Cutting Tool Engineering. He served as the consumer products reporter for BridgeNews and began his publishing career with an 11-year tenure at Appliance magazine, where he rose to managing editor after serving in other roles. Dzierwa's experience with consumer products, including furnishings, appliances, electronics and space design, has transferred to his Firehouse work regarding the magazine's Station Design columns and the Station Design Awards. Previous work also has contributed to his supervision of several surveys of fire service/EMS members, to produce unique reporting for Firehouse's audience. Dzierwa earned a bachelor's degree in English from Columbia College Chicago.