The Apparatus Architect: Fleet Replacement Considerations & the Hicksville Fire Department Experience
Fire departments of all sizes are struggling to manage their fleet replacement program because of extended delivery times and increased costs for new apparatus. Changes in diesel engine technology because of the Environmental Protection Agency’s (EPA) 2027 emissions standards further complicate circumstances.
Departments that have a modest fleet that routinely obtain one new vehicle at a time are considering multiple acquisitions.
Twenty years ago
The Hicksville Fire Department (HFD) in Nassau County, NY, protects a 7-sq.-mi. response area that has a population of 45,000 with four stations. A volunteer force operates five engines, two trucks, one heavy rescue and other support vehicles. The administrative functions are under the auspices of the Board of Fire Commissioners for Hicksville Fire District, which, among other tasks, oversees the department’s apparatus fleet in conjunction with a district manager and mechanic.
During 2023, the HFD responded to 1,864 incidents, including 17 working fires.
Prior to 2004, each company acquired a new apparatus individually. Designs were specific to each vehicle, based on input of company members and an apparatus committee. Past engines were built by several manufacturers. There was little standardization, bowing to each company’s input.
With three engines approaching 20 years old, the decision was made to acquire three identical engines, which would enhance safety and fireground operations via standardized equipment locations, hose loads and major components.
The result: Delivery in 2004 of three Sutphen 2,000-gpm pumpers for Engines 933, 934 and 937. The vehicles included front intakes, electric valves with flowmeters for each discharge and a stainless-steel body. Tilt cabs and access panels that were located on the pump panel (to permit maintenance and repair work with minimal vehicle downtime) and identical major components proved to be an improvement over managing five different vehicle designs.
It’s true that multiple-apparatus purchases can provide efficiencies and cost reductions because of engineering resources and coordination to manage the acquisition process (e.g., bid process, engineering conference and final inspections), but outfitting several rigs all at once can overwhelm a department shop. Another consideration: Time to train individual companies and to wrap up all warranty concerns.
It’s vital for a department to have a good working relationship with the apparatus maker, its salesperson and the service provider for optimized engineering, production and after-delivery warranty services.
Today’s challenges
After 20 years with the uniformly designed/equipped engines, Hicksville Fire District set out to replace the rigs. An apparatus committee sought input from the district mechanic based on the experience from the existing engines. (The other two engine companies operate vehicles acquired in 2007 and 2014. Those purchases reinforced the effect of major components, piping and equipment locations on vehicle downtime, training and fireground operations.)
Ordering an updated version of a current engine is difficult, if not impossible, because of changes in engine emissions and electronic components. Technology that leans toward more standardized cab and body designs is a factor, too.
Over the past decade, EPA emissions regulations have affected availability of diesel engine models and cab designs for apparatus makers. The EPA changes for January 2027 further will affect engine components and their packaging into custom cabs.
As a result, some apparatus makers set up different production lines based on the degree of customization, which influences production time and the engineering resources required for each new rig. As production times have increased to more than three years for some vehicles, departments have had to alter their fleet replacement schedules to adapt to the extended delivery times and dramatic cost increases.
HFD’s results
The three new Sutphen Monarch engines are identical but for minor exceptions in paint colors and graphics. They were produced to allow for the district’s mechanic to outfit each rig with tool mounting, radio installation and other initial upfit work.
The new engines were built on a 199-inch wheelbase. Their raised-roof, four-door, extended cab seats eight. An exterior compartment is designed for storage of a pressurized water extinguisher and forcible entry tools. The front bumper is extended 24 inches to accommodate a 5-inch front suction, a 1¾-inch trash line and individual hose wells.
The rigs have a 500-hp Cummins X12 engine and an Allison EVS 4000 transmission. Auxiliary braking is provided by a three-speed Jacobs engine brake and a focal-mounted Telma driveline retarder. The front and rear axles are rated at 23,000 lbs. and 27,000 lbs., respectively.
A Hale Qmax single-stage, 2,000-gpm pump has 6-inch inlets that have master intake valves that have manual overrides. There are no discharges on the left-side pump panel; two 2½-inch and one 4-inch large-diameter-hose (LDH) discharges are on the right side. The LDH and deck gun discharges have electric controls; the remaining discharges have Trident hand-crank controls. All discharges, including the two crosslay and four rear-body discharges, are outfitted with FRC combination pressure gauges and flowmeters.
Each engine has a mounted Akron 2,000-gpm, manually operated deck gun, a portable monitor and a four-way hydrant valve. Each engine carries 1,000 feet of 5-inch supply line, two beds of 2½-inch hose for back stretches, a 100-foot bumper line and four preconnected 1¾-inch lines. Each rig’s 140-inch-long stainless-steel body is outfitted with standard engine company appliances, tools and equipment, which are mounted in standardized locations.
Our thanks to the Board of Fire Commissioners and the district manager for information for this article.
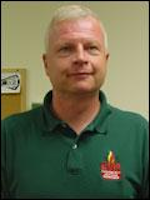
Tom Shand
TOM SHAND, who is a Firehouse contributing editor, is a 36-year veteran of the fire service. He works with Michael Wilbur at Emergency Vehicle Response, consulting on a variety of fire apparatus and fire department master-planning issues. Shand is a member of the Firehouse Hall of Fame.
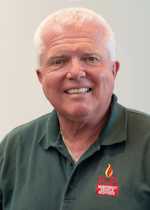
Michael Wilbur
MICHAEL WILBUR, who is a Firehouse contributing editor, retired as a lieutenant in FDNY, where he was last assigned to Ladder Company 27 in the Bronx. He has served on FDNY's Apparatus Purchasing Committee and consults on a variety of apparatus-related issues around the country. Wilbur is a member of the Firehouse Hall of Fame. For further information, access his website at www.emergencyvehicleresponse.com.